The sintering temperature plays a critical role in determining the density and hardness of a sintered material. Optimal sintering temperatures ensure maximum density and hardness by minimizing porosity and promoting uniform grain growth. Deviations from the ideal temperature range can lead to defects, such as excessive grain growth or insufficient densification, which degrade material properties. For example, sintering zirconia at around 1500℃ maximizes its strength, while deviations of 150℃ above or below this temperature can significantly reduce strength due to grain growth. Additionally, the sintering atmosphere and time also influence these properties, as improper conditions can lead to oxidation or incomplete densification.
Key Points Explained:
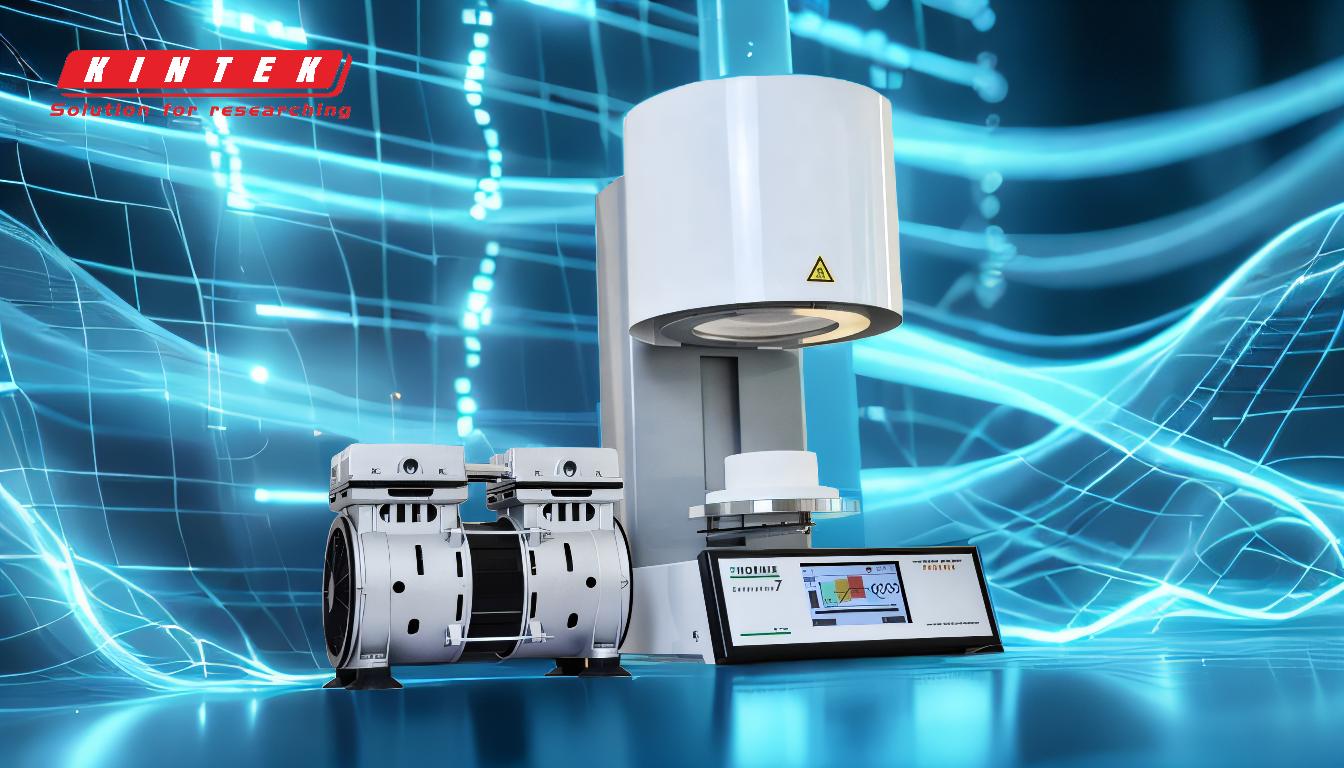
-
Optimal Sintering Temperature for Density and Hardness:
- Sintering at the correct temperature ensures maximum densification, reducing porosity and enhancing hardness.
- For materials like zirconia, a specific temperature (e.g., 1500℃) is critical to achieve the desired properties. Deviations from this temperature can lead to grain growth, which reduces strength and hardness.
-
Effect of High Sintering Temperatures:
- Excessive sintering temperatures can cause overgrowth of grains, leading to a coarser microstructure.
- This grain growth increases porosity and reduces the overall density and hardness of the material.
- High temperatures may also introduce defects, such as cracks or voids, further degrading material properties.
-
Effect of Low Sintering Temperatures:
- Insufficient sintering temperatures result in incomplete densification, leaving the material with higher porosity.
- Low temperatures prevent proper bonding between particles, leading to weaker mechanical properties and lower hardness.
- The material may not achieve the desired strength or durability, making it unsuitable for high-performance applications.
-
Role of Sintering Time:
- Prolonged sintering times at high temperatures can exacerbate grain growth and defect formation, reducing density and hardness.
- Insufficient sintering times may not allow for complete densification, leading to suboptimal material properties.
- Balancing sintering time with temperature is crucial to achieving the desired microstructure and properties.
-
Influence of Sintering Atmosphere:
- The sintering atmosphere (e.g., reducing, oxidizing, or inert) affects the final properties of the material.
- A reducing atmosphere prevents oxidation and allows for the reduction of surface oxides, promoting densification and improving hardness.
- An improper atmosphere can lead to oxidation or contamination, negatively impacting density and hardness.
-
Microstructural Changes During Sintering:
- Sintering directly impacts grain size, pore size, and grain boundary distribution in the material's microstructure.
- Smaller, uniform grains and minimal porosity contribute to higher density and hardness.
- Excessive grain growth or irregular pore distribution weakens the material, reducing its mechanical properties.
-
Practical Implications for Material Selection:
- Understanding the relationship between sintering temperature, density, and hardness is essential for selecting the right material for specific applications.
- For high-strength and durable components, precise control of sintering conditions is necessary to achieve optimal properties.
- Deviations from ideal sintering parameters can lead to material failure or reduced performance in demanding environments.
By carefully controlling sintering temperature, time, and atmosphere, manufacturers can optimize the density and hardness of sintered materials, ensuring they meet the required performance standards for their intended applications.
Summary Table:
Factor | Impact on Density & Hardness |
---|---|
Optimal Temperature | Ensures maximum densification, reduces porosity, and enhances hardness. |
High Temperature | Causes excessive grain growth, increases porosity, and reduces density and hardness. |
Low Temperature | Leads to incomplete densification, higher porosity, and weaker mechanical properties. |
Sintering Time | Prolonged times at high temps worsen grain growth; insufficient times hinder densification. |
Sintering Atmosphere | Reducing atmospheres promote densification; improper atmospheres cause oxidation or defects. |
Microstructural Changes | Smaller, uniform grains and minimal porosity enhance density and hardness. |
Need help optimizing sintering conditions for your materials? Contact our experts today!