Sintering temperature plays a critical role in determining the hardness of a material by influencing its microstructure, including grain size, porosity, and grain boundary characteristics. Optimal sintering temperatures, such as 1500℃ for zirconia, maximize hardness and strength by achieving a dense, fine-grained structure. Deviations from this temperature, either higher or lower, can lead to grain growth, increased porosity, or incomplete densification, all of which degrade hardness. Additionally, the sintering atmosphere and heating time are important factors that interact with temperature to affect the final material properties. Understanding these relationships is essential for optimizing sintering conditions to achieve desired hardness and overall material performance.
Key Points Explained:
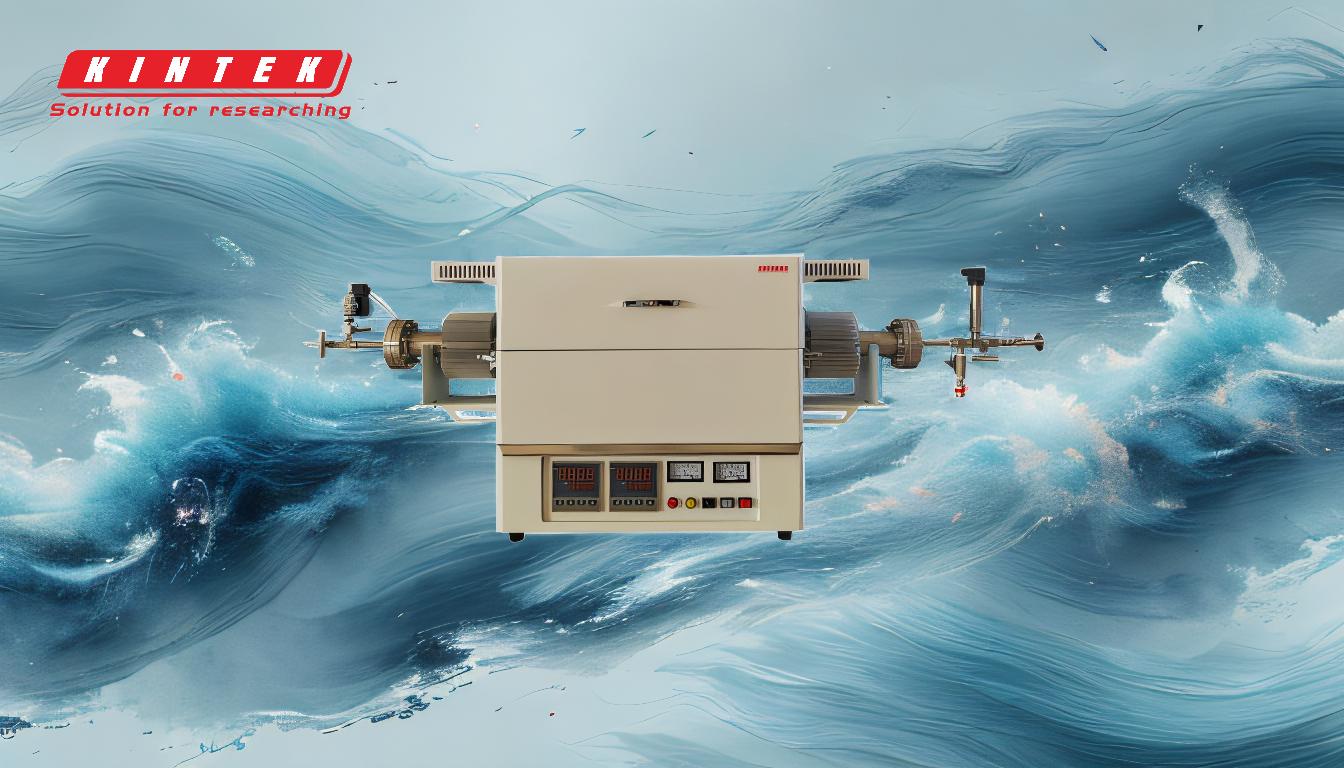
-
Relationship Between Sintering Temperature and Microstructure:
- Sintering temperature directly influences the microstructure of a material, including grain size, pore size, and grain boundary distribution.
- A higher sintering temperature can lead to grain growth, which reduces hardness due to larger, less tightly packed grains.
- Lower sintering temperatures may result in incomplete densification, leaving pores that weaken the material and reduce hardness.
-
Optimal Sintering Temperature for Maximum Hardness:
- For materials like zirconia, sintering at approximately 1500℃ maximizes hardness and strength by achieving a fine-grained, dense structure.
- Deviations from this optimal temperature, even by 150℃, can significantly reduce hardness due to grain growth or incomplete sintering.
-
Effects of Excessive Sintering Temperature:
- High sintering temperatures can cause excessive grain growth, leading to a coarser microstructure and reduced hardness.
- Prolonged exposure to high temperatures can also introduce defects, such as cracks or voids, further degrading hardness and overall material properties.
-
Effects of Insufficient Sintering Temperature:
- Low sintering temperatures may fail to fully densify the material, leaving residual porosity that weakens the structure and reduces hardness.
- Insufficient heating times at low temperatures can exacerbate this issue, resulting in poor material properties.
-
Role of Sintering Atmosphere:
- The sintering atmosphere, such as a reducing atmosphere, can prevent oxidation and promote densification, indirectly affecting hardness.
- A controlled atmosphere ensures that the material's surface properties are preserved, contributing to better hardness and strength.
-
Interaction Between Sintering Temperature and Time:
- Sintering temperature and heating time are interrelated factors that influence hardness.
- High temperatures combined with long heating times can lead to grain growth and defects, while low temperatures with insufficient time can result in incomplete densification.
-
Practical Implications for Material Selection and Processing:
- Understanding the relationship between sintering temperature and hardness is crucial for selecting appropriate processing conditions for specific materials.
- For materials requiring high hardness, such as ceramics or metals used in structural applications, optimizing sintering temperature and time is essential to achieve the desired properties.
By carefully controlling sintering temperature and other related factors, manufacturers can tailor the hardness and overall performance of materials to meet specific application requirements.
Summary Table:
Factor | Effect on Hardness |
---|---|
Optimal Sintering Temperature | Maximizes hardness (e.g., 1500℃ for zirconia) by creating a dense, fine-grained structure. |
Excessive Temperature | Causes grain growth and defects, reducing hardness. |
Insufficient Temperature | Leads to incomplete densification and porosity, weakening the material. |
Sintering Atmosphere | Prevents oxidation and promotes densification, enhancing hardness. |
Heating Time | Interacts with temperature; excessive time at high temps can degrade hardness. |
Optimize your material's hardness with precise sintering conditions—contact our experts today!