The efficiency of a crucible furnace depends on several factors, including its design, insulation, combustion system, and the use of advanced technologies like waste heat recovery systems. Crucible furnaces are generally energy-efficient due to their thick steel construction, high-quality refractory materials, and optimized combustion systems. However, their efficiency can vary significantly based on operational conditions, such as burner settings, crucible size, and proper maintenance. Innovations like ceramic matrix recuperators can enhance efficiency by up to 50% by preheating combustion air using waste heat from exhaust gases. Overall, crucible furnaces are well-suited for small-scale melting applications, offering a balance between energy efficiency and operational simplicity.
Key Points Explained:
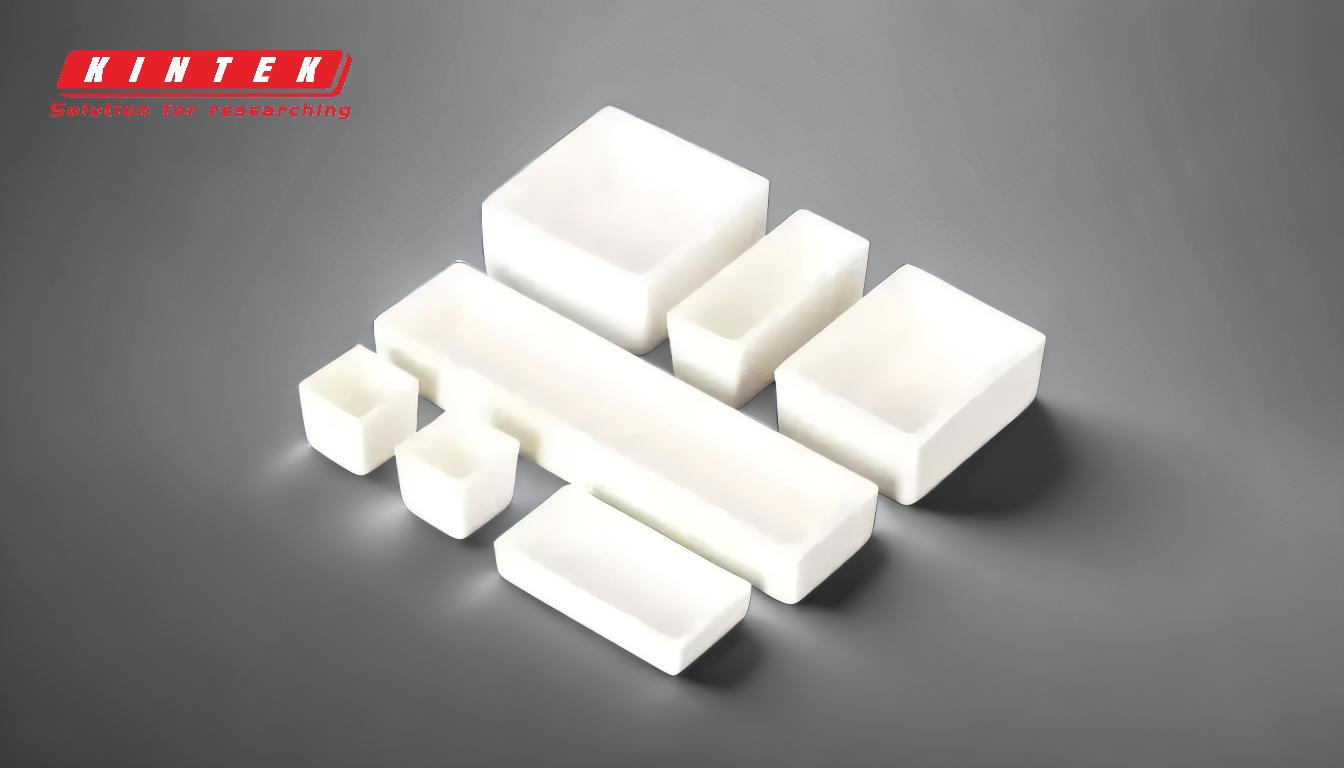
-
Design and Construction:
- Crucible furnaces are built with thick steel boilers and top-quality refractory materials to withstand high temperatures and minimize heat loss.
- The design ensures optimal heat retention, contributing to higher energy efficiency.
-
Combustion System:
- The combustion system in crucible furnaces is optimized to ensure complete fuel combustion, reducing energy waste and emissions.
- Proper burner settings and air-to-fuel ratios are critical for maintaining thermal efficiency.
-
Insulation and Heat Retention:
- High-quality insulation materials are used to reduce heat loss, ensuring that more energy is directed toward melting the metal.
- Effective insulation is a key factor in improving the overall energy efficiency of the furnace.
-
Waste Heat Recovery:
- Adding a ceramic matrix recuperator to the exhaust system can recover waste heat and use it to preheat combustion air, improving efficiency by up to 50%.
- This technology significantly reduces energy consumption and operating costs.
-
Operational Factors:
- The size of the crucible and its precise adjustment to the furnace compartment influence energy consumption.
- Aging crucibles or improper maintenance can reduce efficiency, highlighting the importance of regular upkeep.
-
Environmental Impact:
- Higher energy efficiency not only reduces operating costs but also minimizes the environmental impact by lowering emissions and fuel consumption.
- Innovations like waste heat recovery systems contribute to more sustainable furnace operations.
-
Applications and Suitability:
- Crucible furnaces are ideal for small-scale melting applications, such as jewelry making or hobbyist projects, due to their simplicity and efficiency.
- Their design makes them suitable for indirect heating, ensuring consistent and controlled melting processes.
By considering these factors, crucible furnaces can achieve high energy efficiency, making them a reliable choice for small-scale metal melting applications.
Summary Table:
Factor | Impact on Efficiency |
---|---|
Design & Construction | Thick steel and refractory materials minimize heat loss, ensuring optimal heat retention. |
Combustion System | Optimized for complete fuel combustion, reducing energy waste and emissions. |
Insulation | High-quality insulation reduces heat loss, directing more energy to melting. |
Waste Heat Recovery | Recuperators preheat combustion air, improving efficiency by up to 50%. |
Operational Factors | Crucible size, burner settings, and maintenance significantly influence efficiency. |
Environmental Impact | Higher efficiency lowers emissions and fuel consumption, supporting sustainability. |
Applications | Ideal for small-scale melting, offering simplicity and consistent performance. |
Maximize your crucible furnace's efficiency—contact our experts today for tailored solutions!