CVD coated stands for Chemical Vapor Deposition coated. It refers to a surface treatment process where thin films are applied to various materials using a method called Chemical Vapor Deposition. This process involves chemical reactions in a controlled environment, typically a vacuum chamber, where a reactive gas mixture is introduced and heated to a reaction temperature. The gas reacts or breaks down to deposit a thin film onto the substrate's surface. This method is widely used in industries to enhance material properties such as durability, corrosion resistance, and thermal stability.
Key Points Explained:
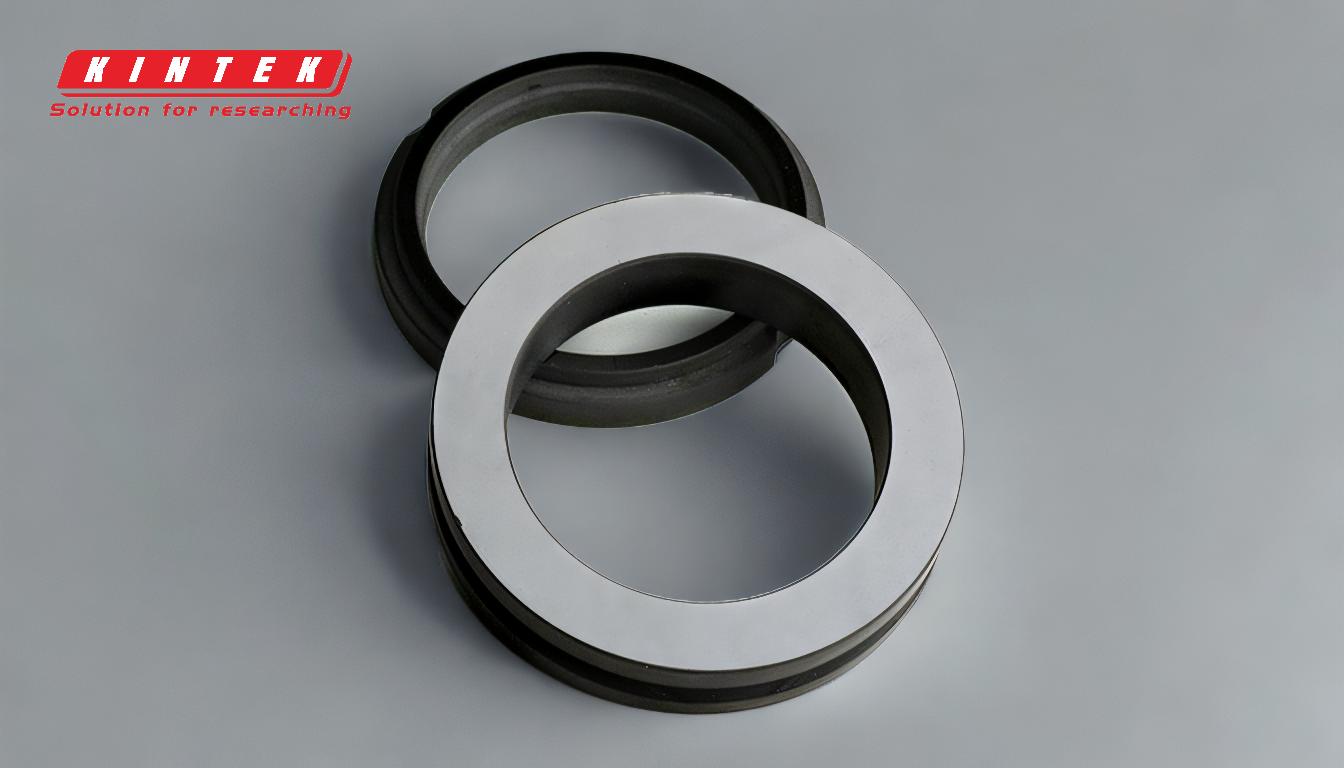
-
Definition of CVD Coated:
- CVD coated stands for Chemical Vapor Deposition coated.
- It is a surface treatment process used to apply thin films onto various materials.
-
Process of Chemical Vapor Deposition:
- Controlled Environment: The process takes place in a vacuum chamber to ensure precise control over the chemical reactions.
- Reactive Gas Mixture: A gas mixture containing the necessary chemical precursors is introduced into the chamber.
- Thermal Activation: The substrate is heated to a specific reaction temperature, causing the gas to react or decompose.
- Film Deposition: The resulting chemical reactions deposit a thin film onto the substrate's surface.
-
Applications of CVD Coating:
- Enhancing Material Properties: CVD coatings are used to improve properties such as hardness, wear resistance, and thermal stability.
- Industrial Uses: Commonly applied in industries like aerospace, automotive, and electronics for protective and functional coatings.
- Laboratory-Grown Diamonds: CVD is also used to create synthetic diamonds in a laboratory setting.
-
Advantages of CVD Coating:
- Uniformity: The process allows for the deposition of highly uniform and consistent thin films.
- Versatility: Can be used on a wide range of materials, including metals, ceramics, and polymers.
- Precision: Offers high precision in controlling the thickness and composition of the deposited films.
-
Considerations for Equipment and Consumable Purchasers:
- Chamber Specifications: Ensure the vacuum chamber can maintain the required pressure and temperature conditions.
- Gas Delivery Systems: Reliable gas delivery systems are crucial for consistent and controlled introduction of reactive gases.
- Substrate Compatibility: Verify that the substrate material is compatible with the CVD process and the intended coating.
- Safety Measures: Implement safety protocols for handling reactive gases and high-temperature operations.
By understanding these key points, purchasers can make informed decisions when selecting CVD coating equipment and consumables, ensuring optimal performance and application results.
Summary Table:
Aspect | Details |
---|---|
Definition | CVD coated stands for Chemical Vapor Deposition coated. |
Process | - Controlled environment in a vacuum chamber |
- Reactive gas mixture introduced and heated | |
- Thin film deposited onto the substrate | |
Applications | - Enhances hardness, wear resistance, and thermal stability |
- Used in aerospace, automotive, electronics, and lab-grown diamonds | |
Advantages | - Uniform and consistent thin films |
- Versatile for metals, ceramics, and polymers | |
- High precision in film thickness and composition | |
Considerations | - Chamber specifications, gas delivery systems, substrate compatibility |
- Safety measures for reactive gases and high temperatures |
Discover how CVD coating can elevate your material performance—contact us today for expert guidance!