Brazing is a metal-joining process that involves heating a filler metal above its melting point and distributing it between two or more close-fitting parts by capillary action. The filler metal, which has a lower melting point than the adjoining metal, flows into the gap between the parts, creating a strong, durable bond upon cooling. Unlike welding, brazing does not melt the base metals, which allows for joining dissimilar materials and maintaining the integrity of the base metals. This process is widely used in industries such as automotive, aerospace, and HVAC for creating leak-proof joints, repairing components, and assembling complex structures with precision.
Key Points Explained:
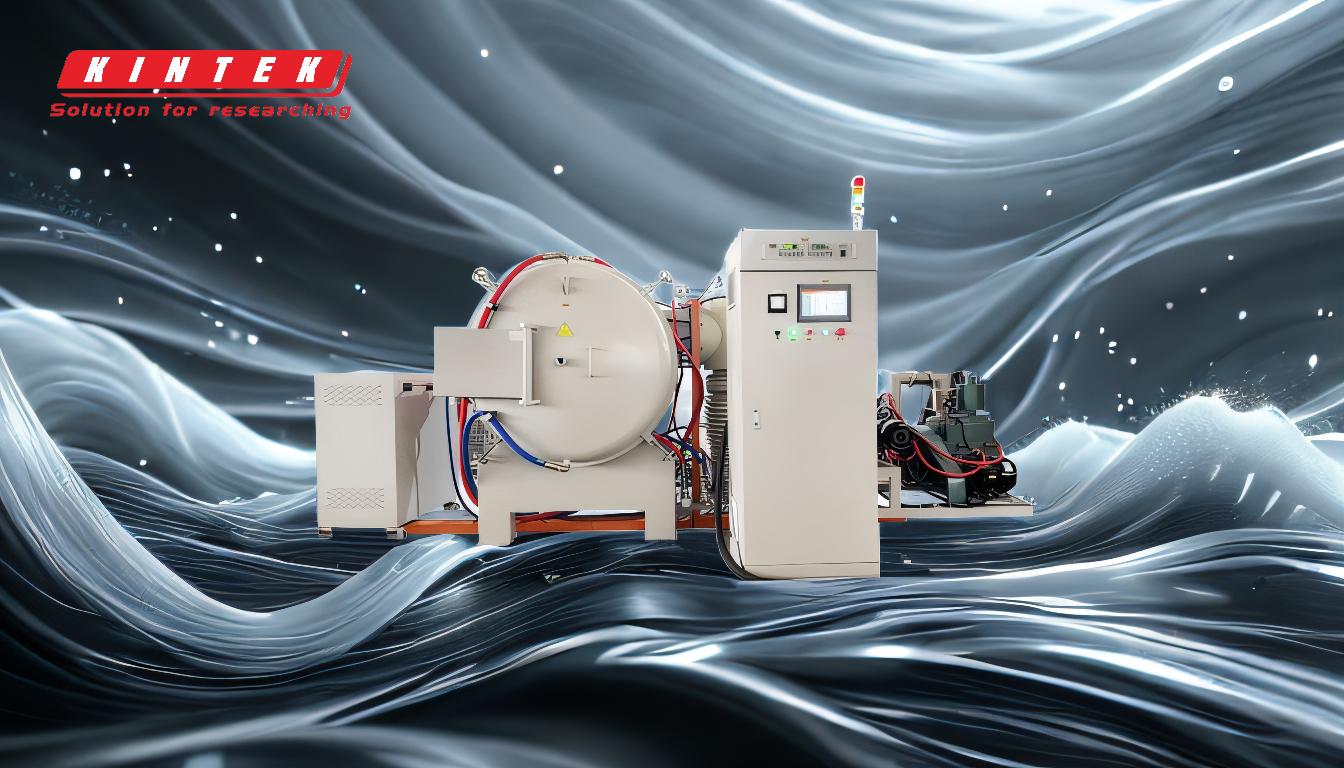
-
Definition and Process of Brazing:
- Brazing is a thermal joining process that uses a filler metal to bond two or more metal parts together.
- The filler metal, typically an alloy like silver, copper, or aluminum, is heated to a temperature above its melting point but below the melting point of the base metals.
- The molten filler metal is drawn into the joint by capillary action, ensuring a uniform and strong bond.
-
Advantages of Brazing:
- Joining Dissimilar Metals: Brazing allows for the joining of different types of metals, such as copper to steel or aluminum to stainless steel, which is not possible with welding.
- Minimal Distortion: Since the base metals do not melt, there is minimal distortion or warping, preserving the dimensional accuracy of the parts.
- Strong and Durable Joints: The joints created by brazing are strong, leak-proof, and resistant to vibration and thermal stress.
- Versatility: Brazing can be used to join complex shapes and assemblies, making it suitable for a wide range of applications.
-
Applications of Brazing:
- Automotive Industry: Brazing is used to join components such as radiators, air conditioning systems, and fuel lines.
- Aerospace Industry: It is employed in the assembly of jet engines, heat exchangers, and other critical components.
- HVAC Systems: Brazing is essential for creating leak-proof joints in refrigeration and air conditioning systems.
- Electronics: It is used to join electrical contacts and heat sinks in electronic devices.
-
Types of Brazing:
- Torch Brazing: Uses a gas flame to heat the filler metal and base metals.
- Furnace Brazing: Involves heating the assembly in a controlled atmosphere furnace, suitable for mass production.
- Induction Brazing: Uses electromagnetic induction to heat the filler metal, offering precise control and fast heating.
- Dip Brazing: The assembly is immersed in a molten salt or metal bath to achieve the brazing temperature.
-
Filler Metals and Fluxes:
- Filler Metals: Common filler metals include silver-based alloys, copper-based alloys, and aluminum-based alloys, chosen based on the base metals and application requirements.
- Fluxes: Fluxes are used to clean the metal surfaces and prevent oxidation during the brazing process. They also promote the flow of the filler metal into the joint.
-
Comparison with Welding:
- Temperature: Brazing operates at lower temperatures than welding, reducing the risk of thermal damage to the base metals.
- Joint Strength: While brazed joints are strong, welded joints are generally stronger due to the fusion of base metals.
- Material Compatibility: Brazing is more versatile in joining dissimilar materials, whereas welding is typically used for similar metals.
-
Quality Control in Brazing:
- Joint Design: Proper joint design is crucial for ensuring a strong bond. Common joint types include lap joints, butt joints, and scarf joints.
- Surface Preparation: Cleaning and preparing the metal surfaces are essential to ensure proper wetting and bonding of the filler metal.
- Inspection: Non-destructive testing methods, such as X-ray or ultrasonic inspection, are used to verify the integrity of brazed joints.
In summary, brazing is a versatile and effective metal-joining process that offers numerous advantages, including the ability to join dissimilar materials, create strong and durable joints, and maintain the integrity of the base metals. Its applications span across various industries, making it an essential technique in modern manufacturing and repair processes.
Summary Table:
Aspect | Details |
---|---|
Definition | A thermal joining process using a filler metal to bond metal parts. |
Key Advantages | Joins dissimilar metals, minimal distortion, strong joints, versatile. |
Applications | Automotive, aerospace, HVAC, electronics. |
Types of Brazing | Torch, furnace, induction, dip brazing. |
Filler Metals | Silver, copper, aluminum alloys. |
Comparison to Welding | Lower temperature, joins dissimilar materials, less thermal damage. |
Quality Control | Proper joint design, surface preparation, non-destructive testing. |
Learn how brazing can enhance your manufacturing process—contact our experts today!