The sintering atmosphere plays a critical role in the sintering process by influencing the quality, properties, and performance of the final sintered product. It involves the use of specific gases or gas mixtures to control various factors such as oxidation, decarburization, and contamination. The atmosphere is carefully selected based on the material being sintered and the desired application, ensuring optimal sintering conditions. By regulating the sintering atmosphere, manufacturers can prevent undesirable chemical reactions, enhance the reduction of surface oxides, and achieve the desired mechanical and physical properties of the sintered parts. This careful control also helps balance operational costs while achieving high-quality results.
Key Points Explained:
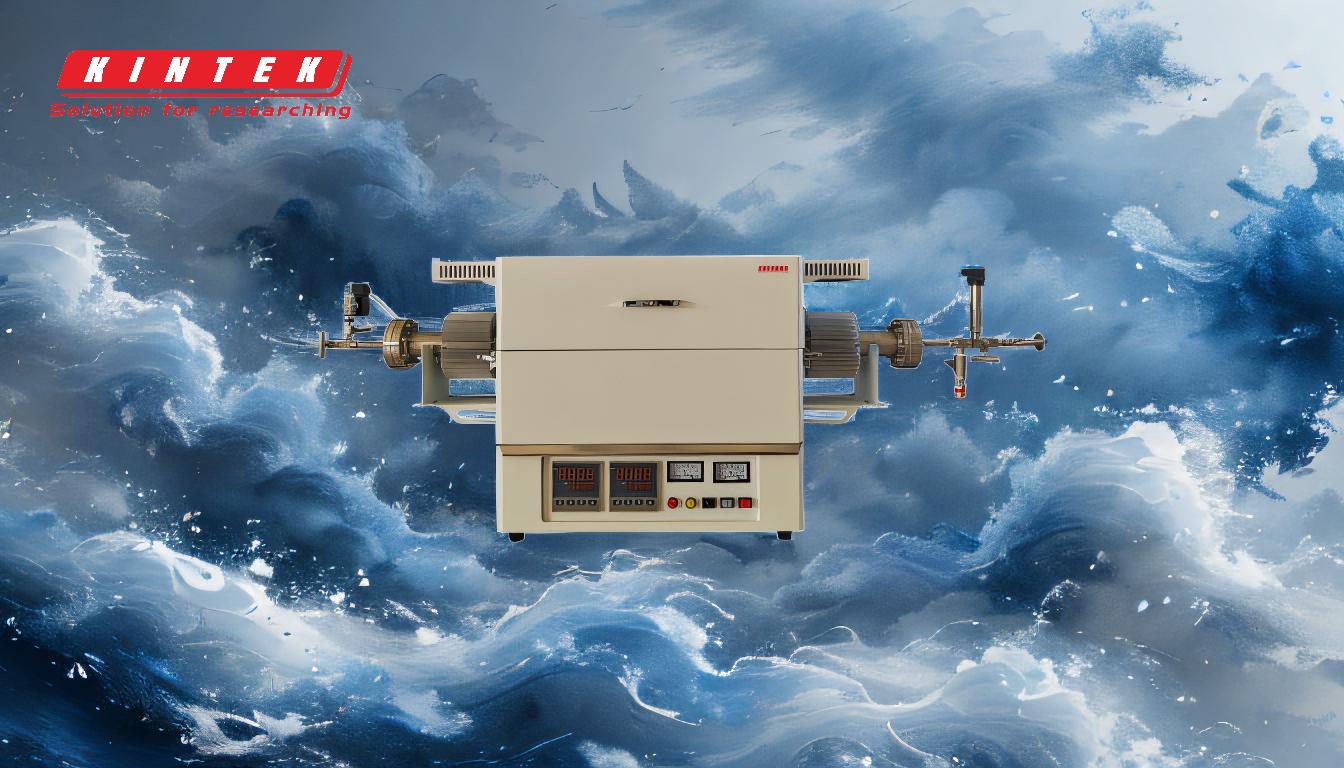
-
Control of Oxidation and Decarburization:
- The sintering atmosphere prevents oxidation and decarburization of the powdered metals during the sintering process. Oxidation can degrade the material's properties, while decarburization can reduce the carbon content in steel, affecting its hardness and strength.
- Example: A reducing atmosphere (e.g., hydrogen or nitrogen-hydrogen mixtures) is often used to minimize oxidation and maintain the integrity of the material.
-
Surface Oxide Reduction:
- The sintering atmosphere facilitates the reduction of surface oxides on the powdered metal particles. This is crucial for achieving strong metallurgical bonds between particles during sintering.
- Example: In a reducing atmosphere, oxides on the surface of metal particles are chemically reduced, improving the sintering quality and final product strength.
-
Prevention of Contamination:
- The atmosphere helps prevent contamination from external elements, such as oxygen or moisture, which can negatively impact the sintering process and the final product's properties.
- Example: Inert gases like argon or nitrogen are used to create a contamination-free environment, especially for reactive materials like titanium or aluminum.
-
Optimization of Sintering Vectors:
- The sintering atmosphere is tailored to control specific sintering vectors, such as temperature, pressure, and gas composition, to achieve the desired microstructure and mechanical properties.
- Example: Different zones in the sintering furnace may use varying gas compositions to optimize the sintering process for different stages, such as preheating, sintering, and cooling.
-
Material-Specific Atmosphere Selection:
- The choice of sintering atmosphere depends on the material being sintered and its intended application. For instance, ferrous materials may require a reducing atmosphere, while non-ferrous materials might need an inert or vacuum environment.
- Example: Sintering stainless steel often involves a hydrogen-nitrogen mixture to prevent oxidation and maintain corrosion resistance.
-
Cost-Effectiveness and Operational Efficiency:
- Selecting the right sintering atmosphere helps balance the trade-off between achieving high-quality results and minimizing operational costs. The use of cost-effective gas mixtures can reduce expenses while maintaining product quality.
- Example: Nitrogen-based atmospheres are often preferred for their cost-effectiveness and ability to provide adequate protection against oxidation.
-
Impact on Final Product Properties:
- The sintering atmosphere directly influences the mechanical, physical, and chemical properties of the sintered body, such as density, strength, and surface finish.
- Example: Sintering in a controlled atmosphere can enhance the density and strength of the final product, ensuring it meets the required specifications for its application.
By understanding and optimizing the sintering atmosphere, manufacturers can achieve consistent, high-quality sintered products tailored to specific material and application requirements. This ensures both performance and cost-effectiveness in the sintering process.
Summary Table:
Key Aspect | Description | Example |
---|---|---|
Oxidation & Decarburization | Prevents oxidation and carbon loss, maintaining material integrity. | Hydrogen or nitrogen-hydrogen mixtures for reducing atmospheres. |
Surface Oxide Reduction | Reduces surface oxides, improving particle bonding and final product strength. | Reducing atmosphere for oxide reduction. |
Contamination Prevention | Protects against external contaminants like oxygen or moisture. | Inert gases (argon or nitrogen) for reactive materials. |
Sintering Vectors Optimization | Controls temperature, pressure, and gas composition for desired properties. | Varying gas compositions in different furnace zones. |
Material-Specific Atmosphere | Tailored atmosphere based on material and application needs. | Hydrogen-nitrogen mix for stainless steel sintering. |
Cost-Effectiveness | Balances quality and operational costs using cost-effective gas mixtures. | Nitrogen-based atmospheres for oxidation protection. |
Final Product Properties | Enhances density, strength, and surface finish of the sintered product. | Controlled atmosphere for improved mechanical and physical properties. |
Discover how the right sintering atmosphere can elevate your product quality—contact our experts today for tailored solutions!