Chemical Vapor Deposition (CVD) is a widely used technique for depositing thin films and coatings onto substrates. The process involves the chemical reaction of gaseous precursors to form a solid material on a substrate. The fundamental steps of CVD include the transport of reactants to the substrate, surface reactions, and the removal of by-products. These steps can be broken down into more detailed processes such as gas-phase reactions, adsorption, surface diffusion, nucleation, and desorption. Understanding these steps is crucial for optimizing the CVD process to achieve high-quality films with desired properties.
Key Points Explained:
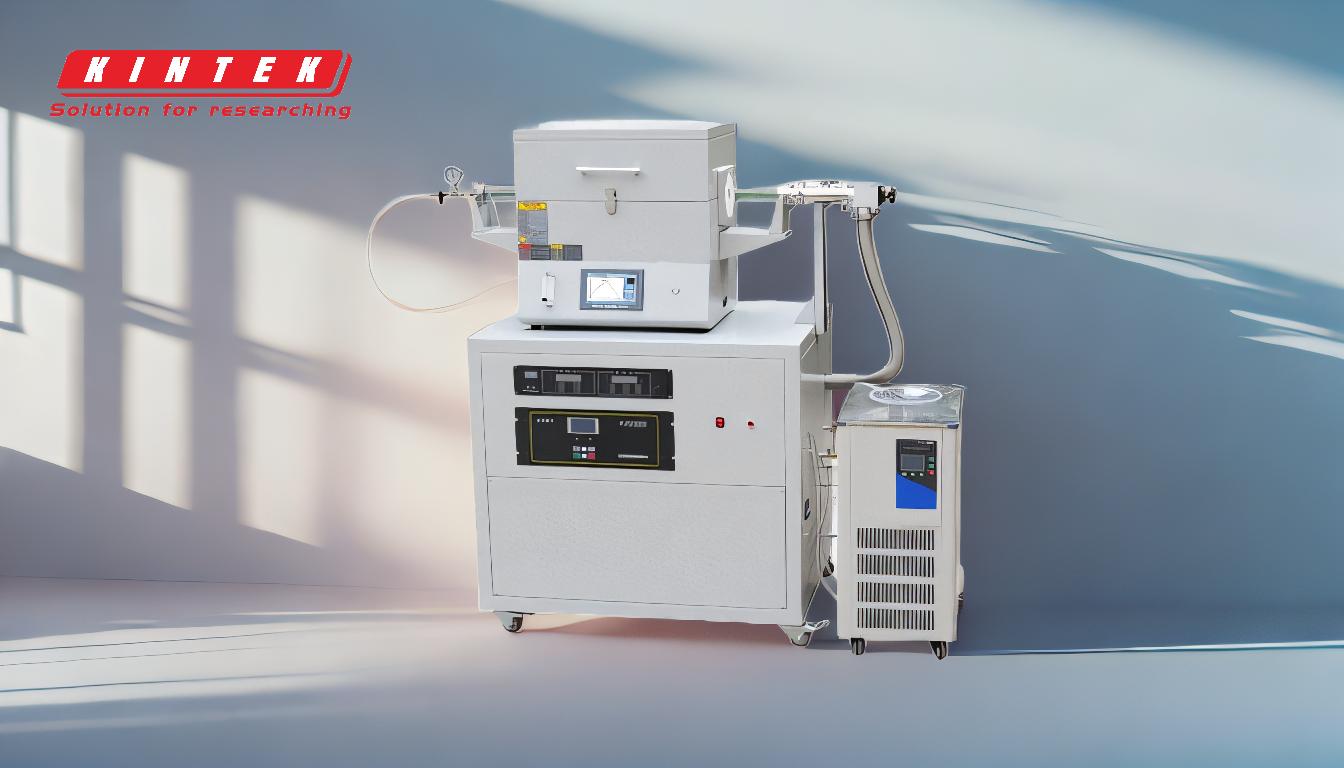
-
Transport of Reactants to the Reaction Chamber:
- The first step in CVD involves the movement of gaseous reactants into the reaction chamber. This can occur through either convection (bulk movement of gas) or diffusion (movement of gas molecules from high to low concentration). The reactants are typically volatile compounds that can be easily vaporized and transported.
-
Gas-Phase Reactions:
- Once inside the reaction chamber, the reactants undergo chemical reactions in the gas phase. These reactions can produce reactive species that are essential for the deposition process. By-products may also form during this stage, which need to be managed to avoid contamination.
-
Transport Through the Boundary Layer:
- The reactants must then move through the boundary layer, a thin layer of gas that forms near the substrate surface. This transport is usually driven by diffusion, as the concentration of reactants is higher in the bulk gas phase than at the substrate surface.
-
Adsorption on the Substrate Surface:
- Upon reaching the substrate, the reactants adsorb onto the surface. Adsorption can be either physical (weak van der Waals forces) or chemical (strong covalent or ionic bonds). This step is critical as it determines how well the reactants will interact with the substrate.
-
Surface Reactions:
- Heterogeneous surface reactions occur at the substrate surface, leading to the formation of a solid film. These reactions are often catalyzed by the substrate material itself or by a catalyst layer deposited on the substrate. The nature of these reactions can significantly affect the properties of the deposited film.
-
Nucleation and Growth:
- Once the surface reactions begin, nucleation sites form where the film starts to grow. These sites can be influenced by the substrate's surface energy, temperature, and the presence of impurities. The growth of the film continues as more reactants are adsorbed and react at these sites.
-
Desorption of By-Products:
- As the film grows, volatile by-products are formed and must be desorbed from the surface. These by-products diffuse through the boundary layer and are eventually removed from the reaction chamber. Efficient removal of by-products is essential to maintain the quality of the deposited film.
-
Removal of Gaseous By-Products:
- The final step involves the removal of all gaseous by-products from the reaction chamber. This is typically achieved through convection and diffusion processes, ensuring that the chamber is clean and ready for the next cycle of deposition.
In summary, the CVD process is a complex sequence of steps that involve the transport, reaction, and removal of various chemical species. Each step must be carefully controlled to achieve the desired film properties, such as thickness, uniformity, and adhesion. Understanding these fundamentals is essential for anyone involved in the design, optimization, or operation of CVD systems.
Summary Table:
Step | Description |
---|---|
Transport of Reactants | Movement of gaseous reactants into the reaction chamber via convection or diffusion. |
Gas-Phase Reactions | Chemical reactions in the gas phase produce reactive species and by-products. |
Transport Through Boundary Layer | Reactants diffuse through the boundary layer near the substrate surface. |
Adsorption on Substrate Surface | Reactants adsorb onto the substrate via physical or chemical bonding. |
Surface Reactions | Heterogeneous reactions form a solid film, often catalyzed by the substrate or a catalyst layer. |
Nucleation and Growth | Film growth begins at nucleation sites influenced by surface energy, temperature, and impurities. |
Desorption of By-Products | Volatile by-products desorb from the surface and diffuse through the boundary layer. |
Removal of Gaseous By-Products | By-products are removed from the chamber via convection and diffusion. |
Optimize your CVD process for superior film quality—contact our experts today!