Heat treatment of metals is a controlled process used to alter the physical and mechanical properties of metals, such as hardness, ductility, toughness, and strength. This is achieved through a series of steps involving heating, holding at a specific temperature, and cooling the metal in a controlled manner. The process can involve methods like annealing, quenching, tempering, case hardening, and more, each tailored to achieve specific material characteristics. Heat treatment is widely used in manufacturing to enhance the durability, versatility, and performance of metals for various applications.
Key Points Explained:
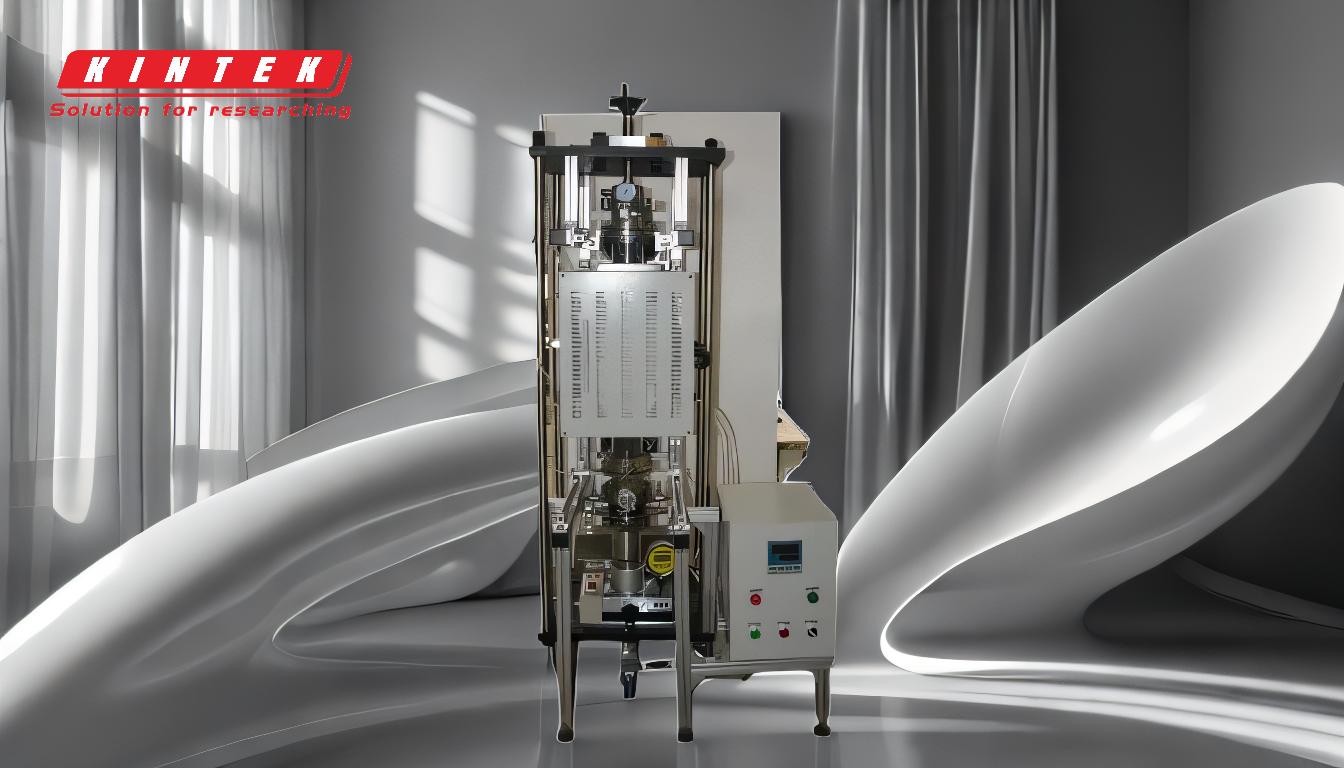
-
Definition of Heat Treatment:
- Heat treatment is a process that involves heating metals to a specific temperature, holding them at that temperature for a set period, and then cooling them in a controlled manner. This process modifies the microstructure of the metal, leading to changes in its physical and mechanical properties.
-
Purpose of Heat Treatment:
- The primary goal of heat treatment is to improve the properties of metals, such as:
- Hardness: Increasing resistance to deformation.
- Ductility: Enhancing the ability to deform without breaking.
- Toughness: Improving resistance to fracture under stress.
- Strength: Increasing the load-bearing capacity.
- Surface Hardness: Enhancing wear resistance on the surface.
- The primary goal of heat treatment is to improve the properties of metals, such as:
-
Basic Steps in Heat Treatment:
- Heating: The metal is heated to a specific temperature, which can range up to 2,400°F depending on the material and desired outcome.
- Holding: The metal is held at the specified temperature for a set period, which can vary from a few seconds to several hours.
- Cooling: The metal is cooled according to prescribed methods, which can include air cooling, oil quenching, or water quenching. The cooling rate is critical in determining the final properties of the metal.
-
Common Heat Treatment Processes:
- Annealing: This process involves heating the metal to a specific temperature and then slowly cooling it to soften the material, improve ductility, and relieve internal stresses.
- Quenching: The metal is rapidly cooled (often in water, oil, or air) to increase hardness and strength. However, this can make the metal brittle, so it is often followed by tempering.
- Tempering: After quenching, the metal is reheated to a lower temperature and then cooled to reduce brittleness and improve toughness.
- Case Hardening: This process hardens the surface of the metal while keeping the core soft and ductile. Techniques include carburizing, nitriding, and induction hardening.
- Precipitation Hardening: This involves heating the metal to a specific temperature to form precipitates that increase strength and hardness.
- Normalizing: Similar to annealing, but the metal is cooled in air to refine the grain structure and improve mechanical properties.
-
Applications of Heat Treatment:
- Heat treatment is widely used in various industries to enhance the performance and longevity of metal components. For example:
- Automotive Industry: To increase the strength and wear resistance of engine parts, gears, and axles.
- Aerospace Industry: To improve the toughness and fatigue resistance of aircraft components.
- Tool Manufacturing: To enhance the hardness and durability of cutting tools and dies.
- Construction: To strengthen structural steel components.
- Heat treatment is widely used in various industries to enhance the performance and longevity of metal components. For example:
-
Factors Influencing Heat Treatment:
- Temperature: The temperature to which the metal is heated is critical and varies depending on the type of metal and the desired properties.
- Time: The duration the metal is held at the specified temperature affects the extent of the microstructural changes.
- Cooling Rate: The rate at which the metal is cooled determines the final properties. Rapid cooling (quenching) increases hardness, while slow cooling (annealing) increases ductility.
-
Benefits of Heat Treatment:
- Enhanced Material Properties: Heat treatment can significantly improve the mechanical properties of metals, making them more suitable for specific applications.
- Versatility: Different heat treatment processes can be applied to achieve a wide range of properties, from soft and ductile to hard and wear-resistant.
- Cost-Effectiveness: By improving the properties of existing metals, heat treatment can reduce the need for more expensive materials or complex manufacturing processes.
-
Challenges and Considerations:
- Precision: Heat treatment requires precise control of temperature, time, and cooling rates to achieve the desired properties.
- Distortion: Rapid cooling can cause warping or distortion in the metal, which may require additional machining or corrective processes.
- Material Selection: Not all metals respond to heat treatment in the same way. The composition and initial microstructure of the metal play a significant role in determining the effectiveness of the process.
In summary, heat treatment is a critical process in metallurgy that allows for the customization of metal properties to meet specific application requirements. By carefully controlling the heating, holding, and cooling processes, manufacturers can produce metals with enhanced strength, durability, and performance, making heat treatment an indispensable part of modern manufacturing.
Summary Table:
Aspect | Details |
---|---|
Purpose | Improve hardness, ductility, toughness, strength, and surface hardness. |
Key Processes | Annealing, quenching, tempering, case hardening, precipitation hardening. |
Applications | Automotive, aerospace, tool manufacturing, construction industries. |
Benefits | Enhanced material properties, versatility, and cost-effectiveness. |
Challenges | Precision control, distortion, and material-specific responses. |
Discover how heat treatment can optimize your metal components—contact our experts today!