The hydraulic forging process is a manufacturing technique that uses hydraulic pressure to shape metal into desired forms. This process is highly efficient and precise, making it suitable for producing complex and high-strength components. Hydraulic forging involves the use of a hydraulic hot press machine, which applies controlled force to deform metal at high temperatures. This method is widely used in industries such as aerospace, automotive, and heavy machinery due to its ability to produce parts with superior mechanical properties and dimensional accuracy. The process is particularly advantageous for creating large or intricate components that require consistent quality and durability.
Key Points Explained:
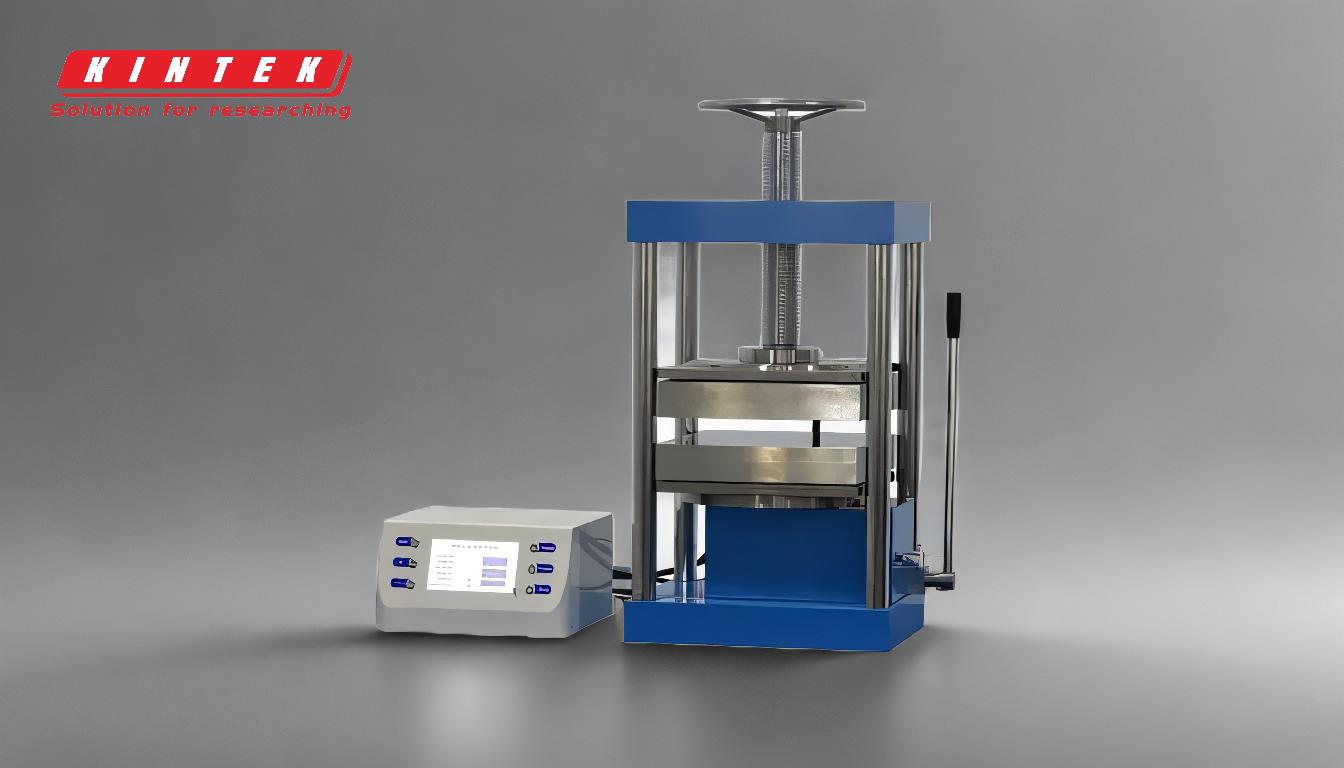
-
Definition of Hydraulic Forging
Hydraulic forging is a metalworking process that utilizes hydraulic pressure to shape and form metal. Unlike mechanical forging, which relies on mechanical force, hydraulic forging uses fluid pressure to apply a controlled and uniform force. This allows for precise control over the deformation process, making it ideal for creating complex geometries and high-strength parts. -
Role of the Hydraulic Hot Press Machine
The hydraulic hot press machine is the core equipment used in this process. It consists of a hydraulic system that generates high pressure to move a ram or piston, which then applies force to the metal workpiece. The machine is capable of delivering consistent pressure across the entire surface of the workpiece, ensuring uniform deformation and minimizing defects. -
Steps in the Hydraulic Forging Process
- Heating the Metal: The metal is heated to a specific temperature to make it malleable. This temperature varies depending on the type of metal being forged.
- Positioning the Workpiece: The heated metal is placed between the dies of the hydraulic press.
- Applying Pressure: The hydraulic system activates, and the ram applies pressure to the metal, forcing it to take the shape of the dies.
- Cooling and Finishing: After forging, the metal is cooled and may undergo additional processes such as machining or heat treatment to achieve the desired properties.
-
Advantages of Hydraulic Forging
- Precision and Control: The hydraulic system allows for fine control over the force applied, resulting in high accuracy and repeatability.
- Versatility: Suitable for a wide range of metals and alloys, including steel, aluminum, and titanium.
- Efficiency: Capable of producing large or complex parts in a single operation, reducing the need for multiple processing steps.
- Superior Mechanical Properties: The process enhances the strength, toughness, and fatigue resistance of the forged components.
-
Applications of Hydraulic Forging
Hydraulic forging is used in industries that require high-performance components, such as:- Aerospace: Forging critical parts like turbine blades and engine components.
- Automotive: Producing crankshafts, gears, and suspension components.
- Heavy Machinery: Manufacturing large gears, shafts, and structural components.
-
Comparison with Other Forging Methods
- Mechanical Forging: Relies on mechanical force, which can be less precise and more prone to variations.
- Drop Forging: Uses gravity-driven hammers, which are less controlled compared to hydraulic systems.
- Open-Die Forging: Suitable for simpler shapes but lacks the precision of hydraulic forging for complex geometries.
-
Considerations for Purchasing Hydraulic Forging Equipment
When selecting a hydraulic hot press machine, consider factors such as:- Capacity: Ensure the machine can handle the required tonnage and workpiece size.
- Control System: Look for advanced control features for precise operation.
- Durability: Choose machines made from high-quality materials to withstand high pressures and temperatures.
- Energy Efficiency: Opt for systems designed to minimize energy consumption.
By understanding the hydraulic forging process and the role of the hydraulic hot press machine, manufacturers can make informed decisions to optimize their production processes and achieve high-quality results.
Summary Table:
Aspect | Details |
---|---|
Definition | Metalworking process using hydraulic pressure to shape metal. |
Core Equipment | Hydraulic hot press machine for controlled force application. |
Steps | Heating, positioning, applying pressure, cooling, and finishing. |
Advantages | Precision, versatility, efficiency, and superior mechanical properties. |
Applications | Aerospace, automotive, and heavy machinery industries. |
Comparison | More precise than mechanical, drop, and open-die forging methods. |
Equipment Considerations | Capacity, control system, durability, and energy efficiency. |
Discover how hydraulic forging can enhance your manufacturing process—contact our experts today!