The impregnation method is a widely used technique in catalyst preparation, where a porous support material is soaked in a solution containing the active metal precursor. The solution penetrates the pores of the support, and upon drying and calcination, the metal precursor decomposes to form the active catalyst. This method allows for precise control over the metal loading and distribution, making it suitable for various industrial applications. The process involves several steps, including support preparation, impregnation, drying, and calcination, each of which can be optimized to achieve desired catalyst properties.
Key Points Explained:
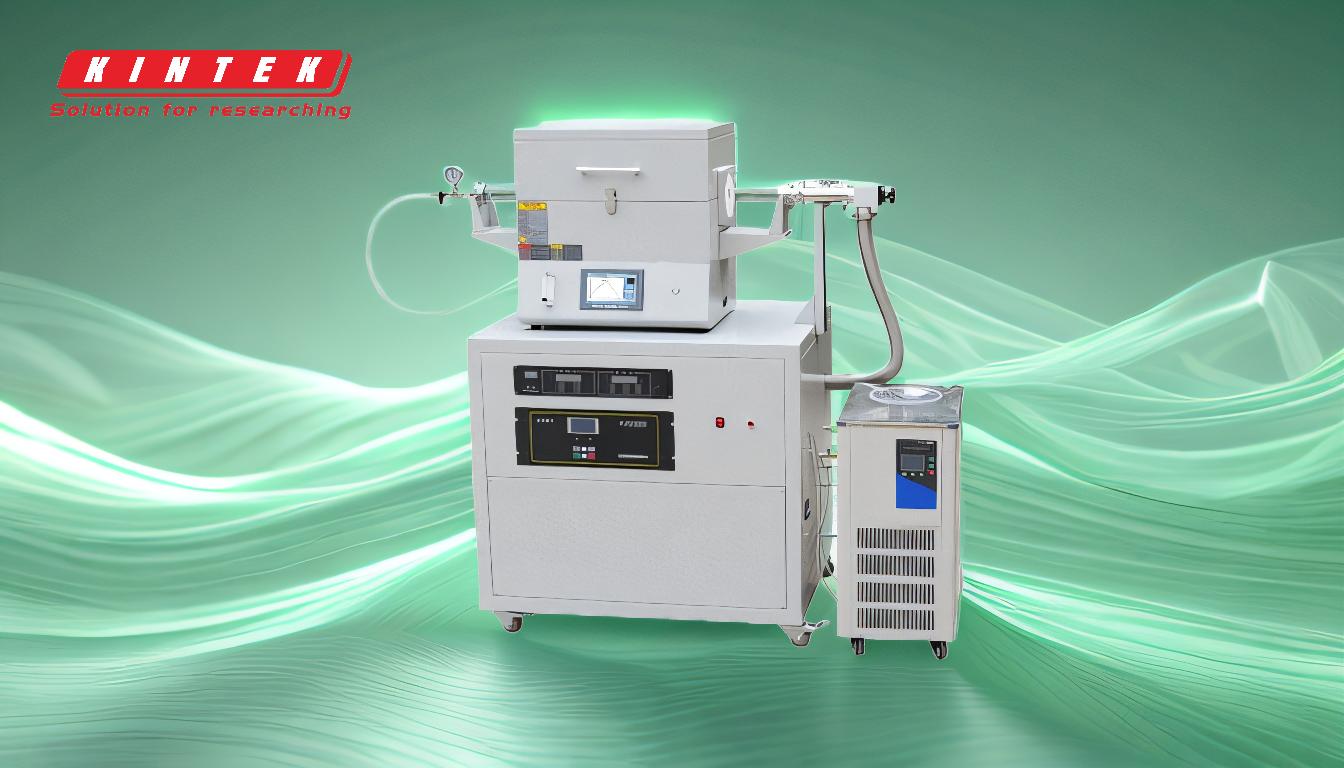
-
Support Material Preparation:
- The support material, often a high-surface-area porous solid like alumina, silica, or zeolites, is prepared to ensure it can effectively adsorb the metal precursor solution.
- The support is typically pre-treated to remove impurities and to create a uniform pore structure, which is crucial for even distribution of the active metal.
-
Impregnation Process:
- The support is immersed in a solution containing the metal precursor (e.g., metal salts like nitrates, chlorides, or acetates).
- The solution is allowed to penetrate the pores of the support, either by capillary action or under vacuum, ensuring that the metal precursor is evenly distributed throughout the support.
- The concentration of the metal precursor in the solution determines the final metal loading on the catalyst.
-
Drying:
- After impregnation, the wet support is dried to remove the solvent, leaving behind the metal precursor within the pores.
- Drying conditions (temperature, time, and atmosphere) are carefully controlled to prevent the migration of the metal precursor to the surface, which could lead to uneven distribution.
-
Calcination:
- The dried material is then calcined at high temperatures (typically 300-600°C) in an oxidizing atmosphere.
- During calcination, the metal precursor decomposes, forming the active metal oxide or metal phase.
- The calcination step also helps in stabilizing the catalyst structure and removing any residual organic compounds.
-
Reduction (if applicable):
- For catalysts requiring a metallic active phase, a reduction step is performed after calcination.
- The catalyst is treated with a reducing gas (e.g., hydrogen) at elevated temperatures to convert the metal oxide to the metallic state.
-
Advantages of Impregnation Method:
- Precise Control: The method allows for precise control over the metal loading and distribution, which is critical for achieving desired catalytic activity and selectivity.
- Versatility: It can be used with a wide range of support materials and metal precursors, making it suitable for various catalytic applications.
- Scalability: The process is easily scalable, making it suitable for industrial-scale catalyst production.
-
Limitations and Considerations:
- Pore Blocking: If the metal precursor concentration is too high, it can lead to pore blocking, reducing the effective surface area of the catalyst.
- Metal Distribution: Uneven drying or calcination can lead to uneven metal distribution, affecting the catalyst's performance.
- Cost: The method can be cost-intensive due to the need for high-purity precursors and controlled processing conditions.
-
Applications:
- The impregnation method is used in the preparation of catalysts for various industrial processes, including petroleum refining, chemical synthesis, and environmental catalysis.
- Examples include hydrotreating catalysts, oxidation catalysts, and automotive exhaust catalysts.
In summary, the impregnation method is a versatile and widely used technique for catalyst preparation, offering precise control over metal loading and distribution. However, careful optimization of each step is required to achieve the desired catalyst properties and performance.
Summary Table:
Key Steps | Description |
---|---|
Support Preparation | Pre-treating porous materials like alumina or silica for uniform metal distribution. |
Impregnation Process | Soaking the support in a metal precursor solution for even penetration. |
Drying | Removing the solvent under controlled conditions to prevent uneven distribution. |
Calcination | Heating to decompose the precursor into the active metal phase. |
Reduction (if needed) | Converting metal oxides to metallic states using reducing gases like hydrogen. |
Advantages | Precise control, versatility, and scalability for industrial applications. |
Limitations | Risk of pore blocking, uneven distribution, and higher costs. |
Applications | Used in petroleum refining, chemical synthesis, and environmental catalysis. |
Discover how the impregnation method can optimize your catalyst preparation—contact our experts today!