The growth of carbon nanotubes (CNTs) via Chemical Vapor Deposition (CVD) is a complex process that involves the decomposition of carbon-containing gases on a catalytic surface, leading to the formation of carbon nanotubes. The mechanism can be broken down into several key steps: the adsorption of carbon-containing gases onto a catalyst, the decomposition of these gases into carbon atoms, the diffusion of carbon atoms through or on the surface of the catalyst, and the nucleation and growth of carbon nanotubes. The catalyst, typically a transition metal like iron, cobalt, or nickel, plays a crucial role in this process by lowering the activation energy required for the decomposition of the carbon source and facilitating the formation of CNTs. The growth process is influenced by various factors such as temperature, pressure, the nature of the catalyst, and the type of carbon source used.
Key Points Explained:
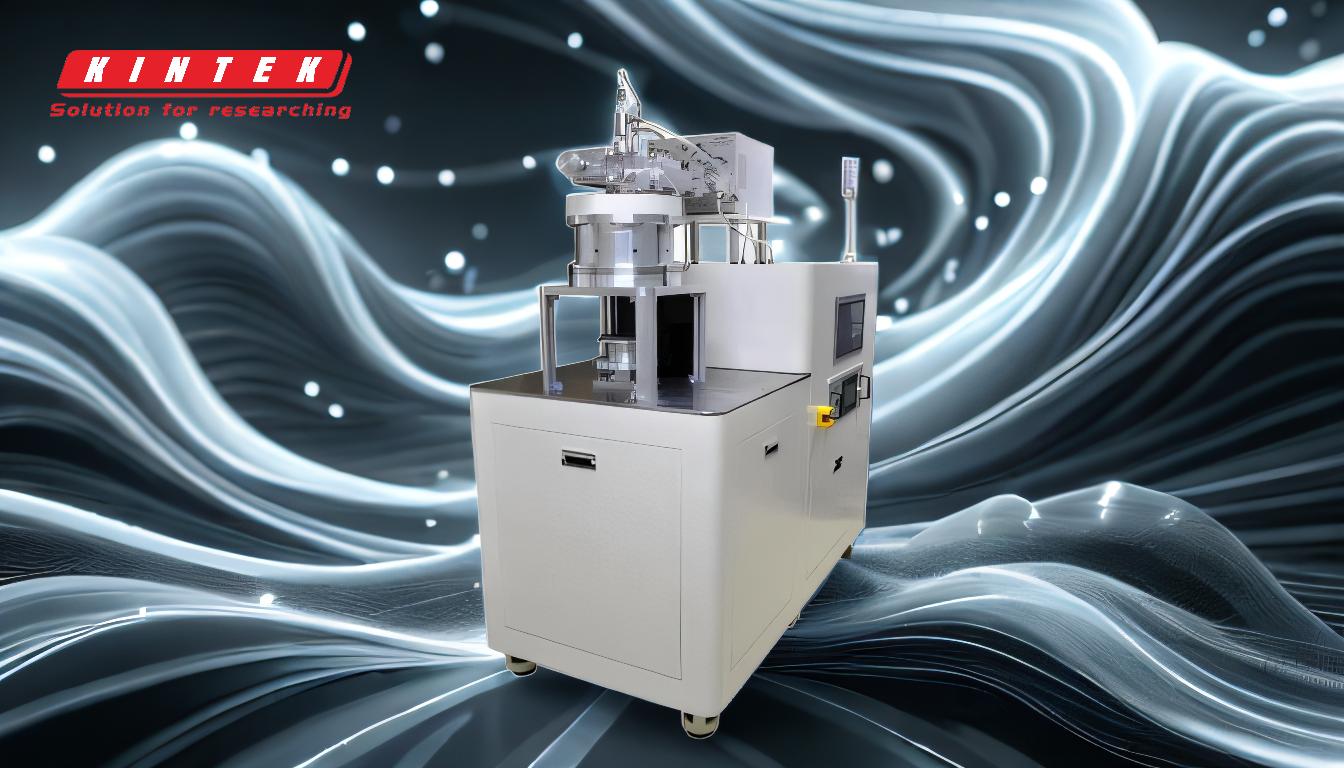
-
Adsorption of Carbon-Containing Gases:
- The process begins with the adsorption of carbon-containing gases, such as methane, ethylene, or acetylene, onto the surface of a catalyst. The catalyst is usually a transition metal nanoparticle deposited on a substrate.
- The adsorption process is influenced by the surface properties of the catalyst, including its size, shape, and crystallographic orientation.
- The carbon-containing gas molecules are adsorbed onto the catalyst surface, where they are held in place by weak van der Waals forces or stronger chemical bonds.
-
Decomposition of Carbon-Containing Gases:
- Once adsorbed, the carbon-containing gases undergo thermal decomposition, breaking down into carbon atoms and hydrogen or other by-products.
- This decomposition is facilitated by the catalyst, which lowers the activation energy required for the reaction to occur.
- The temperature of the CVD process is critical here, as it must be high enough to allow for the decomposition of the gas but not so high that it damages the catalyst or the substrate.
-
Diffusion of Carbon Atoms:
- After decomposition, the carbon atoms diffuse through or on the surface of the catalyst. The diffusion process is influenced by the size and structure of the catalyst particles.
- In some cases, carbon atoms diffuse through the bulk of the catalyst particle, while in others, they diffuse along the surface.
- The rate of diffusion is a key factor in determining the growth rate of the carbon nanotubes.
-
Nucleation and Growth of Carbon Nanotubes:
- Once the carbon atoms reach a certain concentration, they begin to nucleate, forming small clusters that eventually grow into carbon nanotubes.
- The nucleation process is influenced by the catalyst's properties, including its size and shape, as well as the temperature and pressure conditions.
- The growth of the nanotubes occurs as carbon atoms continue to be added to the growing structure, either at the base (root growth) or at the tip (tip growth) of the nanotube.
-
Role of the Catalyst:
- The catalyst is essential for the growth of carbon nanotubes. It not only facilitates the decomposition of the carbon source but also acts as a template for the formation of the nanotube structure.
- The size of the catalyst particles determines the diameter of the resulting nanotubes, while the shape and crystallographic orientation influence the type of nanotube (single-walled, double-walled, or multi-walled) that is formed.
- The catalyst can become deactivated over time due to the accumulation of carbon or other impurities, which can halt the growth process.
-
Influence of Process Parameters:
- The growth of carbon nanotubes by CVD is highly dependent on various process parameters, including temperature, pressure, gas flow rate, and the type of carbon source used.
- Higher temperatures generally favor the growth of nanotubes, but excessive temperatures can lead to the degradation of the catalyst or the substrate.
- The pressure and gas flow rate affect the availability of carbon atoms and the rate at which they are supplied to the catalyst, influencing the growth rate and quality of the nanotubes.
-
Types of Carbon Sources:
- Different carbon sources can be used in the CVD process, each with its own advantages and disadvantages. Common carbon sources include methane, ethylene, acetylene, and carbon monoxide.
- The choice of carbon source can affect the growth rate, the quality of the nanotubes, and the type of nanotubes produced.
- For example, methane tends to produce high-quality single-walled carbon nanotubes, while acetylene is often used for the growth of multi-walled nanotubes.
-
Challenges and Future Directions:
- One of the main challenges in the CVD growth of carbon nanotubes is controlling the uniformity and quality of the nanotubes produced.
- Researchers are exploring various strategies to improve the CVD process, including the use of different catalysts, the optimization of process parameters, and the development of new carbon sources.
- Future directions in this field include the large-scale production of carbon nanotubes with controlled properties for applications in electronics, energy storage, and composite materials.
In summary, the growth of carbon nanotubes by CVD is a multi-step process that involves the adsorption and decomposition of carbon-containing gases, the diffusion of carbon atoms, and the nucleation and growth of nanotubes on a catalytic surface. The catalyst plays a crucial role in this process, and the growth is influenced by various process parameters. Understanding the mechanism of CNT growth by CVD is essential for optimizing the process and producing high-quality nanotubes for various applications.
Summary Table:
Step | Description |
---|---|
1. Adsorption | Carbon-containing gases (e.g., methane, ethylene) adsorb onto the catalyst surface. |
2. Decomposition | Gases break down into carbon atoms and by-products, facilitated by the catalyst. |
3. Diffusion | Carbon atoms diffuse through or on the catalyst surface. |
4. Nucleation & Growth | Carbon atoms form clusters, leading to the growth of nanotubes (root or tip growth). |
5. Catalyst Role | Catalyst lowers activation energy, determines nanotube diameter, and influences type. |
6. Process Parameters | Temperature, pressure, and gas flow rate affect growth rate and quality. |
7. Carbon Sources | Methane, ethylene, acetylene, and carbon monoxide influence nanotube properties. |
8. Challenges & Future | Uniformity, quality control, and large-scale production are key challenges. |
Need more details on carbon nanotube growth by CVD? Contact our experts today for tailored insights!