Spark Plasma Sintering (SPS), also known as Field Assisted Sintering Technique (FAST) or Direct Current Sintering (DCS), is an advanced sintering method that combines pressure and an electric field to densify ceramic and metallic powders. The process involves applying a pulsed DC current directly to the powder particles, generating localized high temperatures (up to 10,000°C) and plasma, which activates particle surfaces and promotes rapid densification. This method allows for lower sintering temperatures, shorter processing times, and high-density materials (over 99% in some cases). The mechanism relies on Joule heating, discharge plasma, and surface diffusion, making it energy-efficient and environmentally friendly.
Key Points Explained:
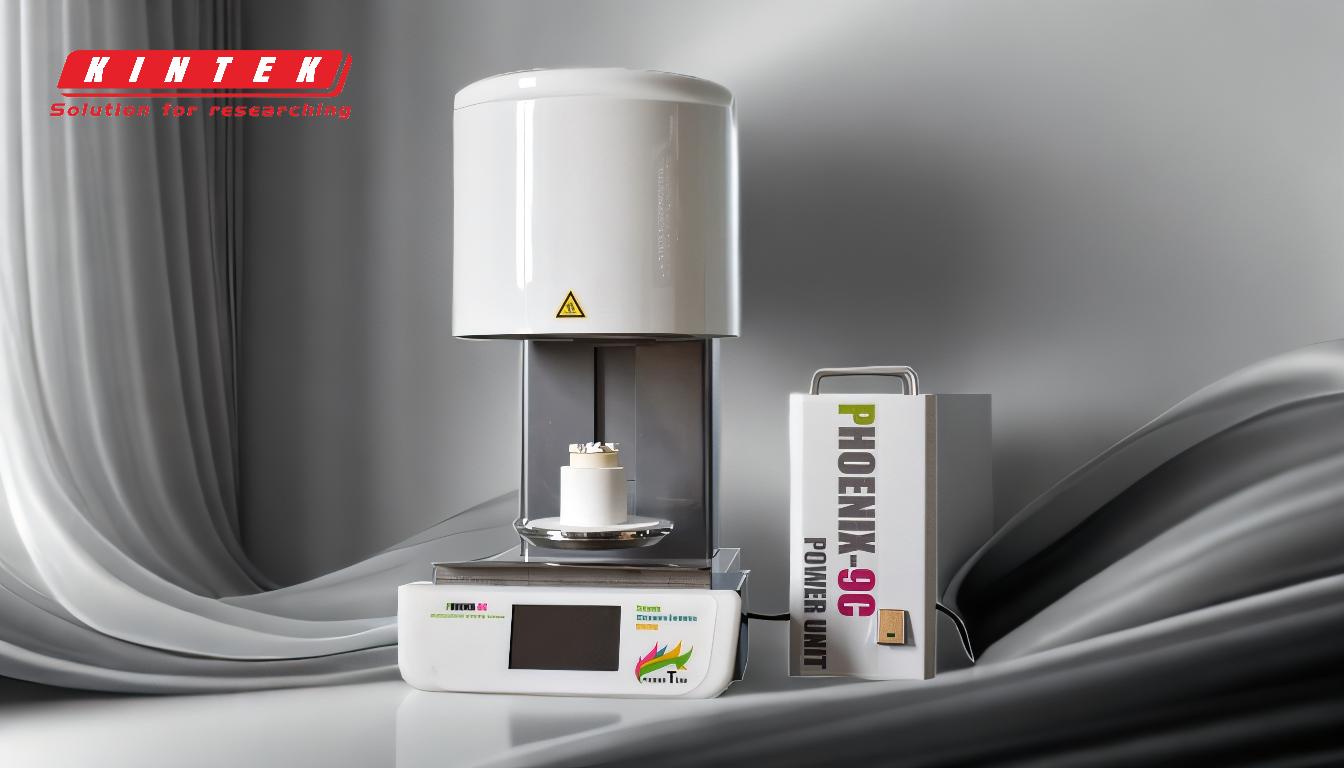
-
Application of Pulsed DC Current:
- SPS uses a pulsed DC current applied directly to the powder particles, which generates localized high temperatures and plasma.
- The pulsed current creates discharge plasma and discharge impact pressure, which activate the particle surfaces and enhance densification.
-
Generation of High Temperatures:
- The pulsed current produces instantaneous high temperatures (up to 10,000°C) between particles, causing surface melting and the formation of "necks" that bond particles together.
- This high temperature also helps in the oxidation or evaporation of surface contaminants, leading to cleaner particle interfaces.
-
Plasma Activation:
- The discharge plasma generated during the process activates the particle surfaces, reducing the energy required for sintering.
- Plasma activation facilitates surface diffusion and boundary defect diffusion, which are critical for rapid densification.
-
Joule Heating:
- Joule heating occurs as the electric current passes through the conductive die and the powder particles, generating uniform heat within the sintered body.
- This internal heating, combined with external heating from the die, allows for rapid and uniform sintering.
-
Pressure Application:
- Pressure is applied simultaneously with the electric current, which helps in reducing particle gaps and promoting densification.
- The combination of pressure and electric field results in lower sintering temperatures compared to conventional methods.
-
Rapid Densification:
- SPS enables rapid densification of materials, often achieving densities over 99% in a short time.
- The process is characterized by fast heating and cooling rates, as well as short holding times, which contribute to the efficiency of the method.
-
Energy Efficiency and Environmental Friendliness:
- SPS is an energy-efficient process due to its rapid heating and short processing times.
- The method is also environmentally friendly, as it reduces the need for high temperatures and long sintering durations, minimizing energy consumption and emissions.
-
Versatility in Material Processing:
- SPS can be used for a wide range of materials, including ceramics, metals, and composites.
- The process is particularly beneficial for materials that are difficult to sinter using conventional methods, as it allows for lower sintering temperatures and shorter times.
-
Misleading Name Clarification:
- Despite the name "Spark Plasma Sintering," research has shown that plasma generation is not the primary mechanism. The process is more accurately described by alternative names such as Field Assisted Sintering Technique (FAST) or Direct Current Sintering (DCS).
-
Integration of Multiple Effects:
- SPS integrates multiple effects, including plasma activation, hot pressing, and resistance heating, to achieve rapid and efficient sintering.
- This integration results in materials with controlled microstructures and enhanced properties.
In summary, Spark Plasma Sintering is a highly efficient and versatile sintering technique that leverages pulsed DC current, plasma activation, and pressure to achieve rapid densification of materials at lower temperatures. The process offers significant advantages in terms of energy efficiency, environmental impact, and material quality, making it a valuable tool in advanced material processing.
Summary Table:
Key Feature | Description |
---|---|
Pulsed DC Current | Generates localized high temperatures and plasma for rapid densification. |
High Temperatures (up to 10,000°C) | Melts particle surfaces, forming bonds and cleaning interfaces. |
Plasma Activation | Reduces energy requirements and enhances surface diffusion. |
Joule Heating | Ensures uniform heating within the material for efficient sintering. |
Pressure Application | Reduces particle gaps, enabling densification at lower temperatures. |
Rapid Densification | Achieves densities over 99% in shorter processing times. |
Energy Efficiency | Lowers energy consumption and emissions compared to conventional methods. |
Versatility | Suitable for ceramics, metals, and composites, even for hard-to-sinter materials. |
Misleading Name Clarification | Plasma generation is secondary; FAST or DCS are more accurate terms. |
Integration of Multiple Effects | Combines plasma activation, hot pressing, and resistance heating for efficiency. |
Ready to enhance your material processing with Spark Plasma Sintering? Contact our experts today to learn more!