The melting process in an electric furnace involves transforming solid metal into a liquid state by applying heat, which is generated through electrical energy. This process is critical in casting and metal production, as it allows for the shaping and refining of metals. Key factors influencing the melting process include temperature, pressure, impurities, and the presence of oxidants. Electric furnaces are designed to optimize energy efficiency, ensuring that electrical energy is effectively converted into heat. The selection of an electric furnace depends on technical parameters such as power rating, melting capacity, temperature range, and heating rate, which must align with the specific requirements of the metal being melted. Understanding these factors ensures efficient and cost-effective melting operations.
Key Points Explained:
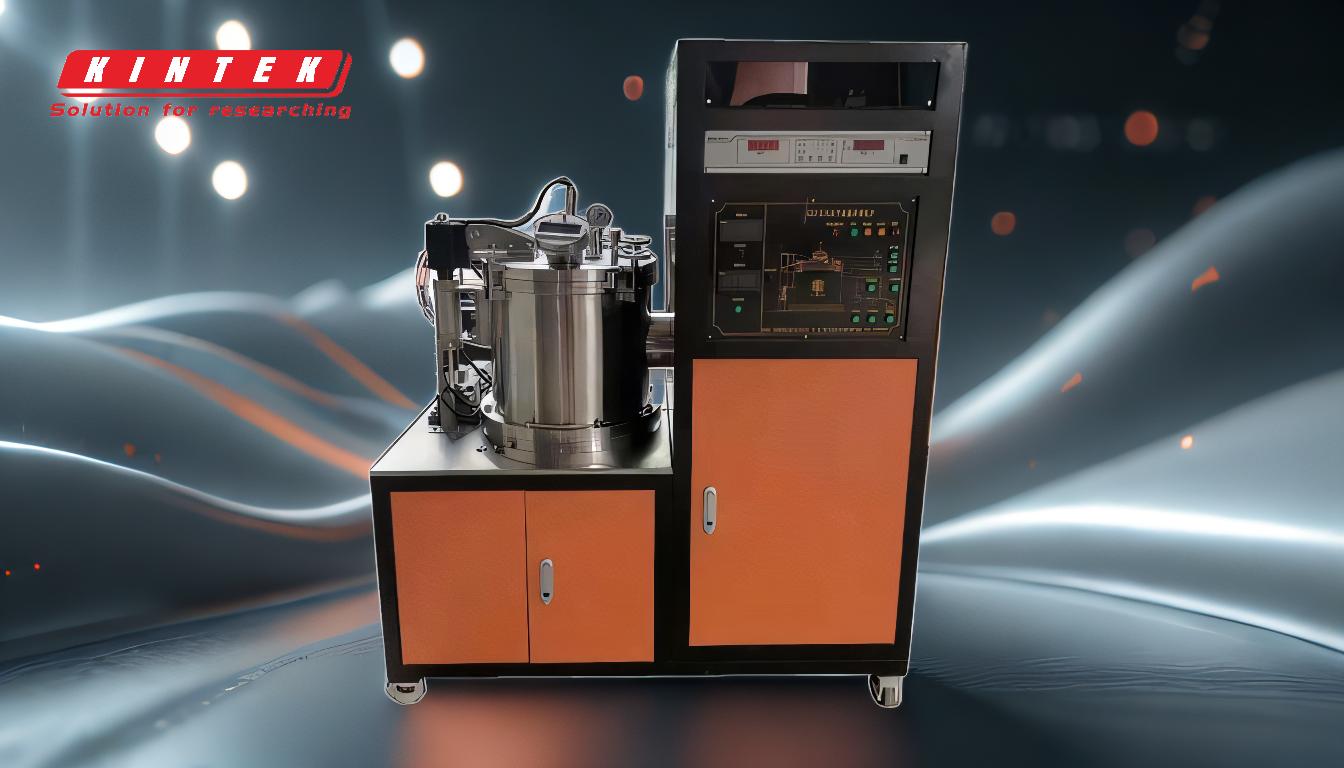
-
Definition of Smelting in an Electric Furnace:
- Smelting is the process of converting solid metal into a liquid state by applying heat, typically generated through electrical energy in an electric furnace.
- This process is essential in casting and metal production, enabling the shaping and refining of metals for various industrial applications.
-
Factors Influencing the Melting Process:
- Temperature: The furnace must generate and maintain temperatures exceeding the metal's melting point to achieve liquefaction. Each metal has a specific transition temperature from solid to liquid.
- Pressure: The phase transition of metals is also dependent on pressure, which can affect the melting point.
- Impurities and Slags: The presence of impurities and slags can influence the melting process, often requiring additional steps to refine the metal.
- Oxidants: Oxidants are sometimes used to accelerate the melting process by promoting chemical reactions that aid in liquefaction.
-
Technical Parameters for Selecting an Electric Furnace:
- Power Rating: The power rating of the furnace determines its capacity to generate heat and melt metal efficiently.
- Melting Capacity: This refers to the amount of metal the furnace can melt within a specific time frame.
- Temperature Range: The furnace must be capable of reaching and maintaining the required temperatures for the specific metal being melted.
- Heating Rate: The speed at which the furnace can heat the metal to its melting point is crucial for productivity.
- Energy Efficiency: Energy efficiency is a critical factor, as it determines how effectively the furnace converts electrical energy into heat energy. Higher energy efficiency reduces operating costs and minimizes environmental impact.
-
Energy Efficiency in Electric Furnaces:
- Energy efficiency is influenced by factors such as insulation materials, furnace design, and control systems.
- Efficient insulation materials reduce heat loss, ensuring that more energy is used for melting the metal.
- Advanced furnace designs and control systems optimize the heating process, further enhancing energy efficiency.
-
Phase Transition and Melting Point:
- The phase transition from solid to liquid in metals is dependent on both temperature and pressure.
- The furnace must be capable of generating and maintaining temperatures that exceed the metal's melting point to ensure complete liquefaction.
-
Applications and Importance of Electric Furnace Melting:
- Electric furnace melting is widely used in industries such as steel production, foundries, and metal recycling.
- The process allows for precise control over the melting conditions, ensuring high-quality metal output.
- It is also an environmentally friendly option compared to traditional fuel-based furnaces, as it reduces emissions and energy consumption.
By understanding these key points, purchasers and operators of electric furnaces can make informed decisions about selecting and optimizing equipment for their specific melting requirements. This ensures efficient, cost-effective, and environmentally sustainable metal production processes.
Summary Table:
Key Factor | Description |
---|---|
Temperature | Must exceed the metal's melting point for liquefaction. |
Pressure | Affects the melting point and phase transition of metals. |
Impurities and Slags | Influence the melting process and may require additional refining steps. |
Oxidants | Accelerate melting by promoting chemical reactions. |
Power Rating | Determines the furnace's heat generation capacity. |
Melting Capacity | Amount of metal the furnace can melt within a specific time frame. |
Temperature Range | Must align with the required temperatures for the metal being melted. |
Heating Rate | Speed at which the furnace heats metal to its melting point. |
Energy Efficiency | Ensures effective conversion of electrical energy into heat, reducing costs. |
Ready to optimize your metal melting process? Contact us today for expert advice on electric furnaces!