The strength of a brazed joint is influenced by a multitude of factors, including the materials used, the design of the joint, and the brazing process parameters. However, the most critical factor is the design of the joint itself. A well-designed joint ensures proper filler metal distribution, adequate surface contact, and optimal stress distribution, which collectively contribute to a joint strength that can exceed that of the parent metal. Additionally, process parameters such as heating rate, holding time, and cooling rate must be carefully controlled to achieve a high-quality brazed joint. These factors are interdependent and must be optimized through experimentation to achieve the desired strength.
Key Points Explained:
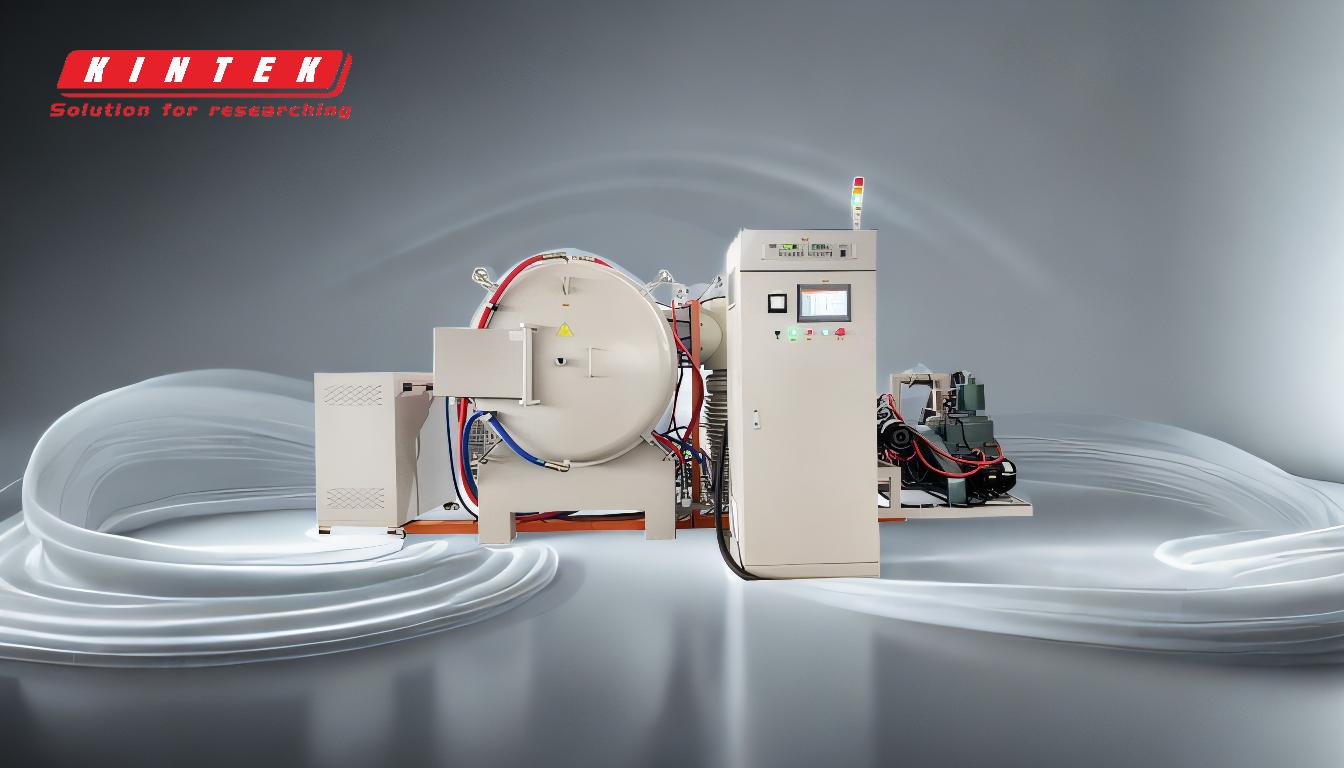
-
Joint Design:
- The design of the joint is the most critical factor influencing the strength of a brazed joint. A properly designed joint ensures:
- Uniform distribution of the filler metal.
- Maximum surface contact between the filler metal and the base materials.
- Optimal stress distribution to prevent localized weaknesses.
- Poor joint design can lead to inadequate filler metal flow, voids, and stress concentrations, which compromise the joint's strength.
- The design of the joint is the most critical factor influencing the strength of a brazed joint. A properly designed joint ensures:
-
Material Compatibility:
- The type of aluminum alloy and brazing filler metal used must be compatible to ensure strong metallurgical bonding.
- Incompatible materials can lead to poor wetting, insufficient bonding, and reduced joint strength.
-
Surface Preparation:
- Proper removal of surface oxide films is essential for achieving a strong bond. This is often done using alkali solutions, and the composition, concentration, temperature, and time of this process must be carefully controlled.
- Inadequate surface preparation can result in poor filler metal adhesion and weak joints.
-
Brazing Process Parameters:
- Heating Rate: A controlled heating rate ensures uniform temperature distribution and prevents thermal stresses.
- Holding Time: Sufficient holding time allows the filler metal to flow and wet the surfaces properly.
- Cooling Rate: Controlled cooling prevents the formation of brittle phases and reduces residual stresses.
- Vacuum Level (for vacuum brazing): Maintaining the correct vacuum level is crucial to prevent oxidation and ensure proper filler metal flow.
-
Experimental Optimization:
- The optimal combination of process parameters varies depending on the specific materials and joint design. These parameters must be determined through experimental screening to achieve the highest joint strength.
- Iterative testing and adjustment of parameters such as temperature, time, and vacuum level are necessary to fine-tune the brazing process.
-
Quality Requirements:
- The strength of the brazed joint must meet or exceed the strength of the parent metal. This requires adherence to strict quality standards and thorough inspection of the joint after brazing.
- Non-destructive testing methods, such as ultrasonic or X-ray inspection, can be used to ensure the integrity of the joint.
By focusing on these key factors, particularly joint design and process optimization, manufacturers can achieve brazed joints with exceptional strength and reliability.
Summary Table:
Key Factor | Importance |
---|---|
Joint Design | Ensures uniform filler metal distribution, surface contact, and stress control. |
Material Compatibility | Critical for strong metallurgical bonding and joint integrity. |
Surface Preparation | Removes oxide films for better filler metal adhesion. |
Brazing Process Parameters | Heating rate, holding time, cooling rate, and vacuum level must be optimized. |
Experimental Optimization | Iterative testing to fine-tune parameters for maximum joint strength. |
Quality Requirements | Ensures joint strength meets or exceeds parent metal standards. |
Achieve stronger brazed joints with expert guidance—contact us today to optimize your process!