Batch type furnaces are versatile heating systems used for various heat treatment processes, such as annealing, hardening, and stress-relieving. Their operating temperature typically ranges between 1200°F and 2500°F, depending on the specific application and the type of material being treated. These furnaces are designed to heat a batch of components at a time, allowing for flexibility in handling different weights, sizes, and grades of materials. The temperature is controlled and adjusted according to the heat treatment cycle, which includes heating, holding, and cooling phases. Batch furnaces are ideal for low-volume production, large-sized parts, or processes requiring deep case carburizing.
Key Points Explained:
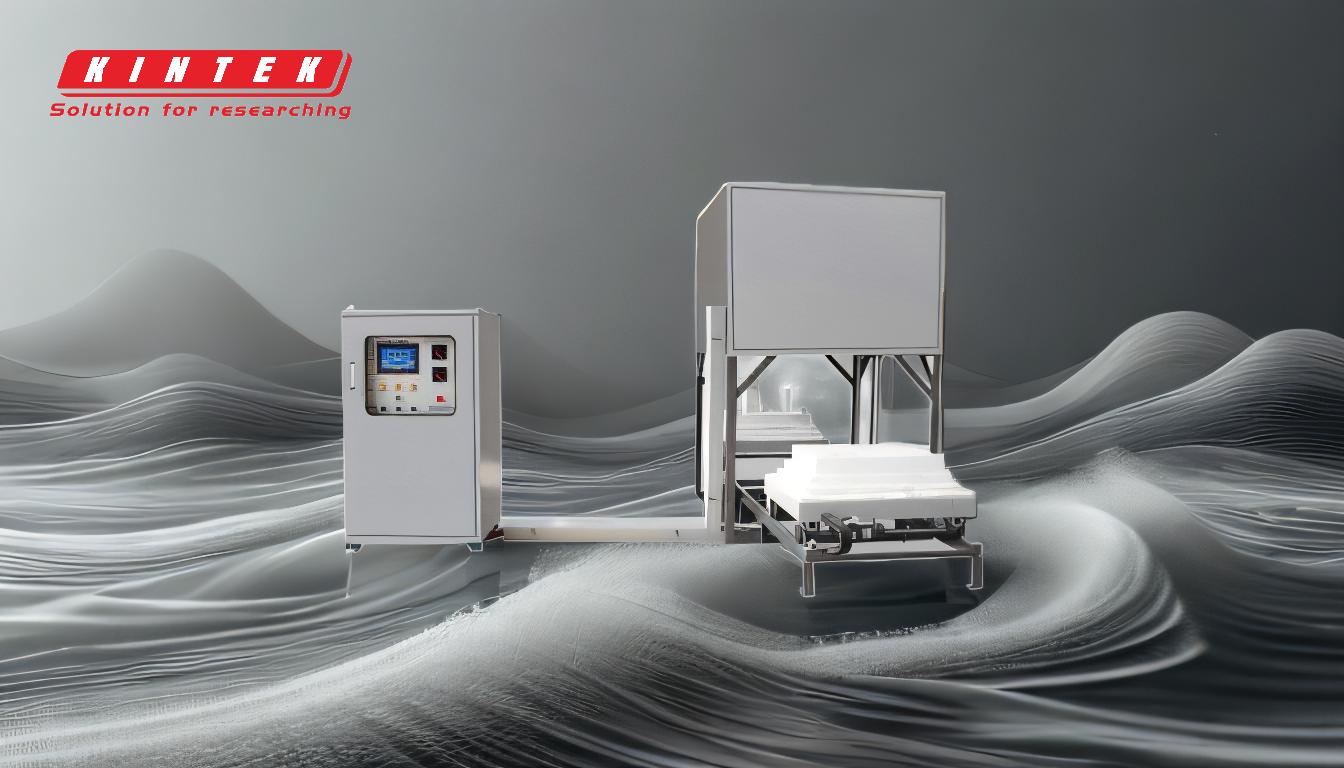
-
Operating Temperature Range
- Batch type furnaces typically operate within a temperature range of 1200°F to 2500°F.
- This range is suitable for a wide variety of heat treatment processes, including annealing, hardening, normalizing, and stress-relieving.
- The specific temperature depends on the material being treated and the desired heat treatment outcome.
-
Heating Process
- The furnace is heated from room temperature to a predetermined maximum temperature at a specified rate.
- The temperature is held at the maximum level for a specified duration to ensure proper heat treatment.
- After the holding period, the furnace is cooled at a controlled rate to complete the process.
-
Flexibility in Application
- Batch furnaces are designed to handle different batches of components, each potentially varying in weight, size, and material grade.
- This flexibility makes them ideal for low-volume production or custom heat treatment requirements.
- They are particularly useful for large-sized parts or processes like deep case carburizing, which are difficult to manage in continuous furnaces.
-
Types of Batch Furnaces
- Common types include box furnaces, car-bottom furnaces, integral-quench furnaces, pit furnaces, and vacuum furnaces.
- Each type is suited for specific applications and temperature ranges, depending on the material and heat treatment process.
-
Controlled Atmosphere Options
- Batch furnaces can be operated with or without a controlled atmosphere.
- A controlled atmosphere is often used to prevent oxidation or to introduce specific gases for processes like carburizing or nitriding.
-
Energy Efficiency and Maintenance
- The energy consumption of batch furnaces depends on factors such as furnace design, workload size, and burner settings.
- Regular maintenance, including cleaning and adjusting burners, is essential to ensure optimal performance and energy efficiency.
-
Comparison with Continuous Furnaces
- Unlike continuous furnaces, which operate at a permanent temperature for uniform heat treatment of identical components, batch furnaces offer greater flexibility for varied workloads.
- Batch furnaces are generally more cost-effective for low-volume or customized production runs.
-
Applications in Industry
- Batch furnaces are widely used in industries requiring precise heat treatment of metals, such as aerospace, automotive, and tool manufacturing.
- They are also used in dental laboratories for firing ceramics and alloys, where temperature control is critical for achieving desired material properties.
By understanding these key points, equipment and consumable purchasers can make informed decisions about selecting the right batch furnace for their specific heat treatment needs. The operating temperature range, flexibility, and adaptability of batch furnaces make them a valuable asset in various industrial applications.
Summary Table:
Feature | Details |
---|---|
Operating Temperature | 1200°F to 2500°F |
Heating Process | Heating, holding, and cooling phases for precise control |
Flexibility | Handles varying weights, sizes, and material grades |
Types | Box, car-bottom, integral-quench, pit, and vacuum furnaces |
Controlled Atmosphere | Optional for oxidation prevention or specific gas introduction |
Applications | Aerospace, automotive, tool manufacturing, and dental labs |
Energy Efficiency | Depends on design, workload, and maintenance |
Ready to find the perfect batch furnace for your heat treatment needs? Contact our experts today!