Plasma sintering, also known as Spark Plasma Sintering (SPS), is an advanced sintering technique that utilizes a combination of electric current and physical pressure to rapidly consolidate powdered materials into dense, high-performance components. This method is particularly effective for materials that are difficult to sinter using conventional methods, such as ceramics, metals, and composites. The process involves applying a pulsed direct current (DC) through the powder compact while simultaneously applying uniaxial pressure. The electric current generates plasma within the powder particles, which enhances atomic diffusion and bonding, leading to rapid densification at relatively low temperatures and short processing times. Plasma sintering is widely used in research and development for producing small quantities of new materials with high density and excellent mechanical properties.
Key Points Explained:
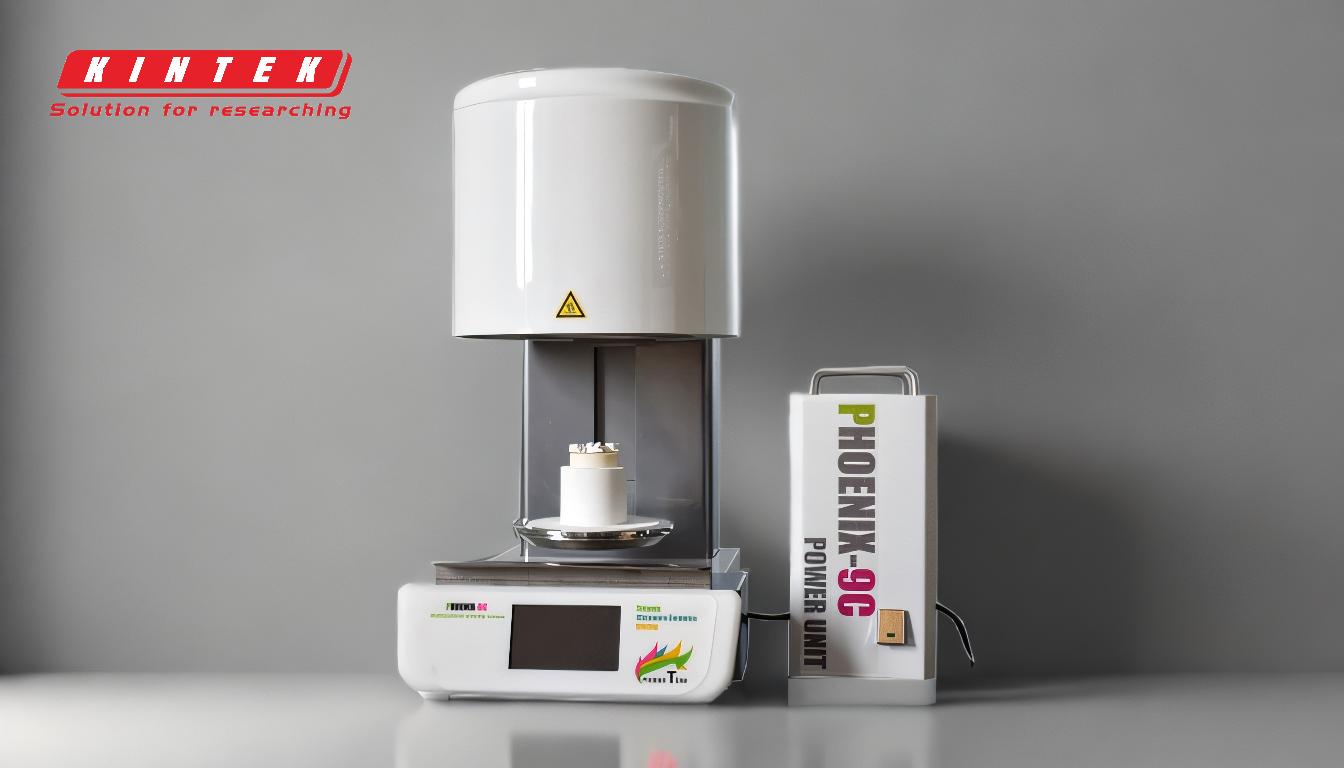
-
Definition and Overview of Plasma Sintering:
- Plasma sintering, or Spark Plasma Sintering (SPS), is a modern sintering technique that combines electric current and physical pressure to consolidate powdered materials.
- It is particularly effective for materials that are challenging to sinter using traditional methods, such as ceramics, metals, and composites.
-
Mechanism of Plasma Sintering:
- The process involves applying a pulsed direct current (DC) through the powder compact while simultaneously applying uniaxial pressure.
- The electric current generates plasma within the powder particles, which enhances atomic diffusion and bonding.
- This leads to rapid densification at relatively low temperatures and short processing times.
-
Advantages of Plasma Sintering:
- High Material Density: Plasma sintering produces materials with high density and excellent mechanical properties.
- Controllable External Pressure and Sintering Atmosphere: The process allows for precise control over external pressure and the sintering atmosphere, which is crucial for achieving desired material properties.
- Rapid Processing: The method significantly reduces sintering time compared to conventional techniques, making it ideal for research and development.
- Versatility: Plasma sintering can be used for a wide range of materials, including ceramics, metals, cemented carbide, intermetallic compounds, cermets, and diamond.
-
Applications of Plasma Sintering:
- Research and Development: Plasma sintering is particularly suitable for the preparation of small quantities and multiple varieties of new materials, making it a valuable tool in material research and development.
- Industrial Applications: The technique is used in various industries for sintering or splicing of ceramic materials, metals, and other refractory materials.
- Additive Manufacturing: Plasma sintering can be integrated with additive manufacturing techniques to produce complex three-dimensional objects with high precision.
-
Comparison with Other Sintering Methods:
- Conventional Sintering: Unlike conventional sintering, which relies solely on heat, plasma sintering uses electric current and pressure to enhance densification.
- Microwave Sintering: While microwave sintering uses microwave energy to heat materials, plasma sintering employs electric current to generate plasma, offering faster and more controlled densification.
- Hot Isostatic Pressing (HIP): Both HIP and plasma sintering apply pressure and heat, but plasma sintering uses electric current to generate plasma, resulting in faster processing times.
-
Challenges and Considerations:
- Equipment Cost: Plasma sintering equipment can be expensive, which may limit its adoption in some industries.
- Material Compatibility: Not all materials are suitable for plasma sintering, and the process may require optimization for specific materials.
- Process Control: Precise control over the electric current, pressure, and temperature is essential to achieve consistent results.
In summary, plasma sintering is a highly efficient and versatile sintering method that offers significant advantages in terms of material density, processing speed, and control over sintering conditions. Its ability to rapidly produce high-performance materials makes it an invaluable tool in both research and industrial applications. However, the high cost of equipment and the need for precise process control are important considerations for potential users.
Summary Table:
Aspect | Details |
---|---|
Definition | Combines electric current and pressure to consolidate powdered materials. |
Key Mechanism | Pulsed DC generates plasma, enhancing atomic diffusion and bonding. |
Advantages | High density, rapid processing, controllable pressure, and versatility. |
Applications | R&D, industrial sintering, additive manufacturing. |
Challenges | High equipment cost, material compatibility, and precise process control. |
Ready to explore plasma sintering for your projects? Contact our experts today to learn more!