Spark plasma sintering (SPS) is an advanced sintering technique known for its rapid heating rates, high sintering temperatures, and uniform heating, which enable the production of dense sintered bodies in a short time. The pressure applied during SPS is a critical parameter that influences the densification and mechanical properties of the final product. Typically, the pressure ranges from 20 MPa to 100 MPa, depending on the material being sintered and the desired properties. Higher pressures are often used for materials that are harder to densify, while lower pressures may suffice for more easily sintered materials. The combination of pressure and pulsed electric current in SPS facilitates particle rearrangement, plastic deformation, and diffusion, leading to enhanced densification and improved material properties.
Key Points Explained:
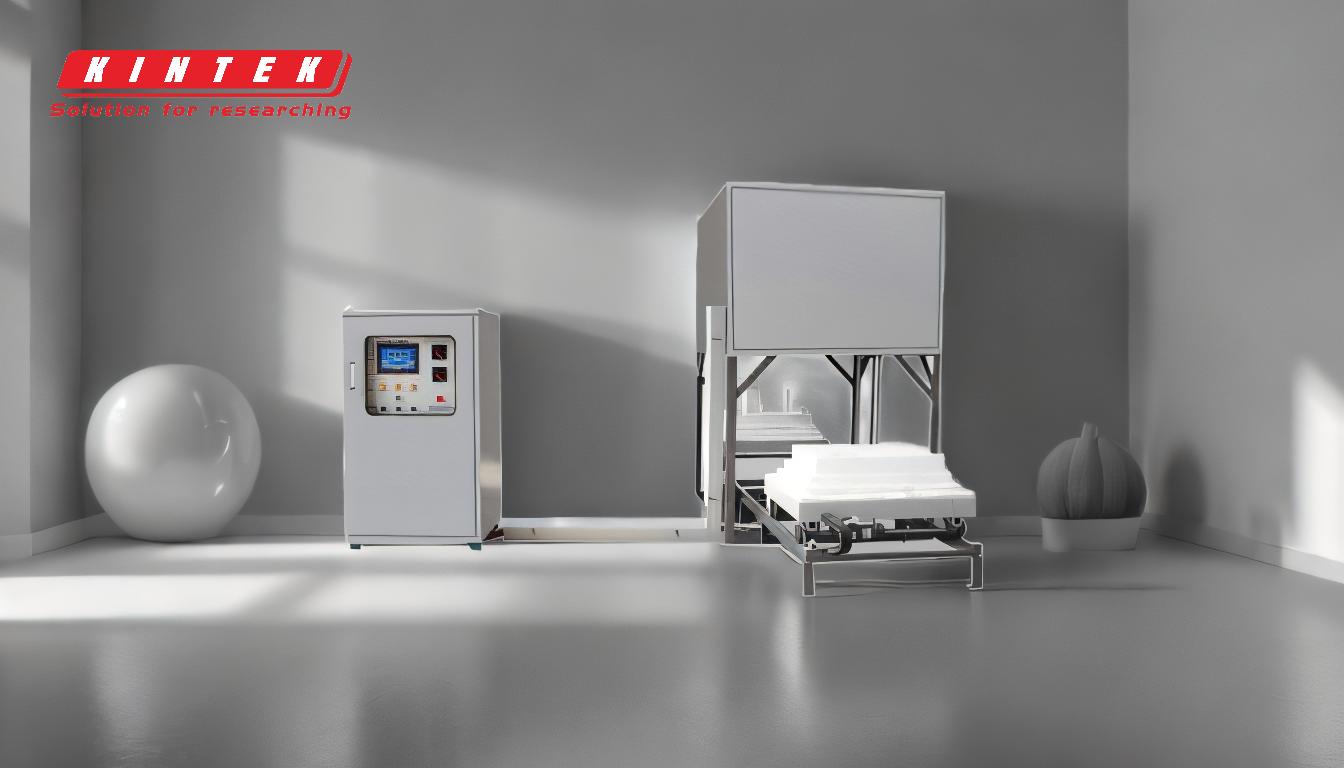
-
Pressure Range in SPS:
- The pressure applied during spark plasma sintering typically ranges from 20 MPa to 100 MPa.
- This range is chosen based on the material's properties, such as hardness and melting point, as well as the desired density and mechanical characteristics of the final product.
- Lower pressures (20-50 MPa) are often sufficient for materials that densify easily, while higher pressures (50-100 MPa) are required for harder or more refractory materials.
-
Role of Pressure in SPS:
- Particle Rearrangement: Pressure helps in the initial stage of sintering by promoting particle rearrangement, which is crucial for achieving a uniform and dense microstructure.
- Plastic Deformation: Higher pressures induce plastic deformation of particles, especially at elevated temperatures, which aids in closing pores and enhancing densification.
- Diffusion Enhancement: Pressure, combined with the pulsed electric current, accelerates diffusion processes, leading to faster grain boundary migration and improved sintering kinetics.
-
Factors Influencing Pressure Selection:
- Material Type: Different materials require different pressures based on their hardness, melting point, and sintering behavior. For example, ceramics may require higher pressures compared to metals.
- Desired Density: The target density of the sintered body influences the pressure choice. Higher densities often necessitate higher pressures.
- Temperature: The sintering temperature and the applied pressure are interrelated. Higher temperatures can sometimes compensate for lower pressures, but the optimal combination must be determined experimentally.
-
Impact of Pressure on Final Properties:
- Mechanical Properties: The pressure applied during SPS significantly affects the mechanical properties of the sintered material, such as hardness, strength, and toughness.
- Microstructure: Pressure influences the grain size and porosity of the sintered body, which in turn affects its mechanical and thermal properties.
- Density: Higher pressures generally lead to higher densities, which are crucial for applications requiring high strength and durability.
-
Practical Considerations:
- Equipment Capability: The maximum pressure that can be applied is limited by the capabilities of the SPS equipment. Users must ensure that their equipment can handle the required pressures.
- Safety: High pressures and temperatures require careful handling to ensure safety during the sintering process.
- Cost: Higher pressures may increase the cost of the sintering process due to the need for more robust equipment and longer processing times.
In summary, the pressure applied during spark plasma sintering is a critical parameter that must be carefully selected based on the material properties, desired final characteristics, and practical considerations. The typical pressure range of 20-100 MPa allows for the production of dense, high-quality sintered bodies with enhanced mechanical properties.
Summary Table:
Aspect | Details |
---|---|
Pressure Range | 20 MPa to 100 MPa, depending on material and desired properties. |
Role of Pressure | Facilitates particle rearrangement, plastic deformation, and diffusion. |
Factors Influencing | Material type, desired density, and sintering temperature. |
Impact on Properties | Affects mechanical properties, microstructure, and density. |
Practical Considerations | Equipment capability, safety, and cost. |
Ready to optimize your spark plasma sintering process? Contact our experts today for tailored solutions!