Vacuum carburizing, also known as low-pressure carburizing (LPC), is a process used to harden metals like iron, steel, or alloy steel by infusing them with carbon. The process involves placing the metal in a vacuum furnace, heating it to the appropriate temperature, and introducing hydrocarbon gases such as propane, acetylene, or cyclohexane. These gases break down under heat, releasing carbon that diffuses into the metal to increase its hardness. The pressure during vacuum carburizing is typically maintained at low levels, often in the range of 10 to 500 mbar (millibar), depending on the specific process and materials used. This low-pressure environment ensures precise control over the carburizing atmosphere, leading to consistent and repeatable results.
Key Points Explained:
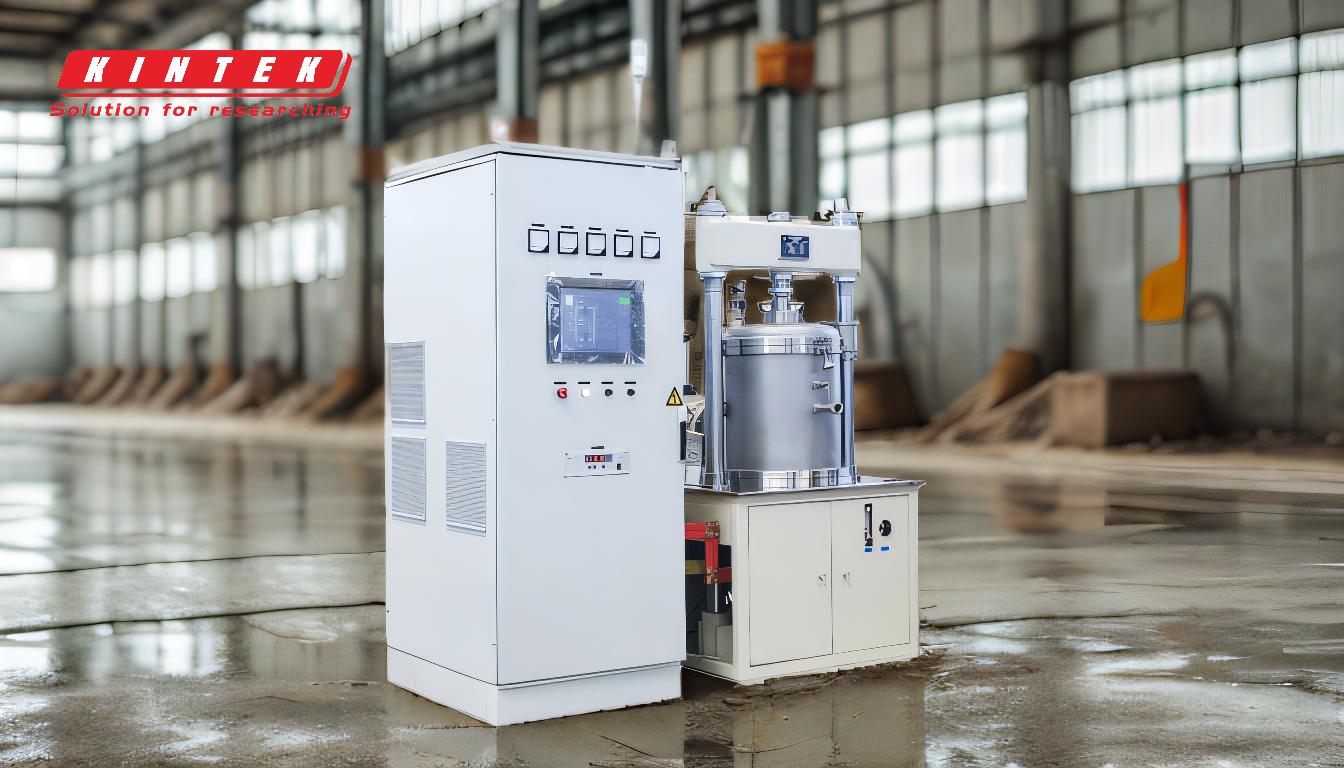
-
Definition of Vacuum Carburizing:
- Vacuum carburizing is a heat treatment process that hardens metals by infusing them with carbon in a low-pressure environment.
- The process is also referred to as low-pressure carburizing (LPC), emphasizing the controlled, low-pressure atmosphere used.
-
Pressure Range in Vacuum Carburizing:
- The pressure during vacuum carburizing is typically maintained between 10 to 500 mbar.
- This low-pressure range is critical for ensuring a controlled and reproducible atmosphere, which is essential for consistent results.
-
Role of Hydrocarbon Gases:
- Hydrocarbon gases such as propane, acetylene, and cyclohexane are commonly used in vacuum carburizing.
- These gases decompose under heat, releasing carbon that diffuses into the metal surface.
- Acetylene and its mixtures (e.g., acetylene + hydrogen or acetylene + ethylene + hydrogen) are particularly popular due to their efficiency.
-
Process Control and Simulation:
- Advanced simulation programs are used to control the vacuum carburizing process.
- These programs apply kinetic and diffusion models to determine boost (carbon infusion) and diffuse (carbon distribution) times based on material chemistry, surface area, and desired case depth.
- The simulations predict outcomes such as case depth, hardness profiles, and microstructural results (e.g., carbide size and retained-austenite levels).
-
Advantages of Low-Pressure Carburizing:
- Precision: The low-pressure environment allows for highly controlled carbon infusion, leading to consistent and repeatable results.
- Efficiency: The use of hydrocarbon gases like acetylene ensures rapid carbon diffusion, reducing processing time.
- Environmental Benefits: Vacuum carburizing produces fewer emissions compared to traditional carburizing methods, making it more environmentally friendly.
-
Steps in the Vacuum Carburizing Process:
- Step 1: Place the metal in a vacuum furnace.
- Step 2: Heat the metal to the required temperature (typically between 850°C to 1050°C).
- Step 3: Introduce hydrocarbon gas (e.g., propane or acetylene) into the furnace.
- Step 4: Allow the gas to decompose under heat, releasing carbon.
- Step 5: Enable the carbon to diffuse into the metal, hardening its surface.
-
Applications of Vacuum Carburizing:
- This process is widely used in industries requiring high-precision components, such as automotive, aerospace, and tool manufacturing.
- It is particularly beneficial for parts that require deep case depths and uniform hardness profiles.
By maintaining a low-pressure environment and using precise control systems, vacuum carburizing ensures high-quality, repeatable results, making it a preferred method for hardening metals in various industrial applications.
Summary Table:
Key Aspect | Details |
---|---|
Process Name | Vacuum Carburizing (Low-Pressure Carburizing) |
Pressure Range | 10 to 500 mbar |
Hydrocarbon Gases Used | Propane, Acetylene, Cyclohexane |
Temperature Range | 850°C to 1050°C |
Key Advantages | Precision, Efficiency, Environmental Benefits |
Applications | Automotive, Aerospace, Tool Manufacturing |
Discover how vacuum carburizing can enhance your metal hardening process—contact our experts today!