Pressureless sintering is a method of sintering that relies solely on temperature to fuse powdered materials without the application of external pressure. This technique is commonly used in the production of ceramics and metal-ceramic composites, where the goal is to achieve a dense and uniform final product. The process involves creating ceramic or metal powder compacts through methods like cold isostatic pressing, injection molding, or slip casting. These compacts are then pre-sintered and machined to their final shape before being heated. Pressureless sintering is advantageous because it avoids density variations and allows for the production of complex shapes. The heating techniques used include constant-rate heating (CRH), rate-controlled sintering (RCS), and two-step sintering (TSS), each influencing the microstructure and grain size of the final product.
Key Points Explained:
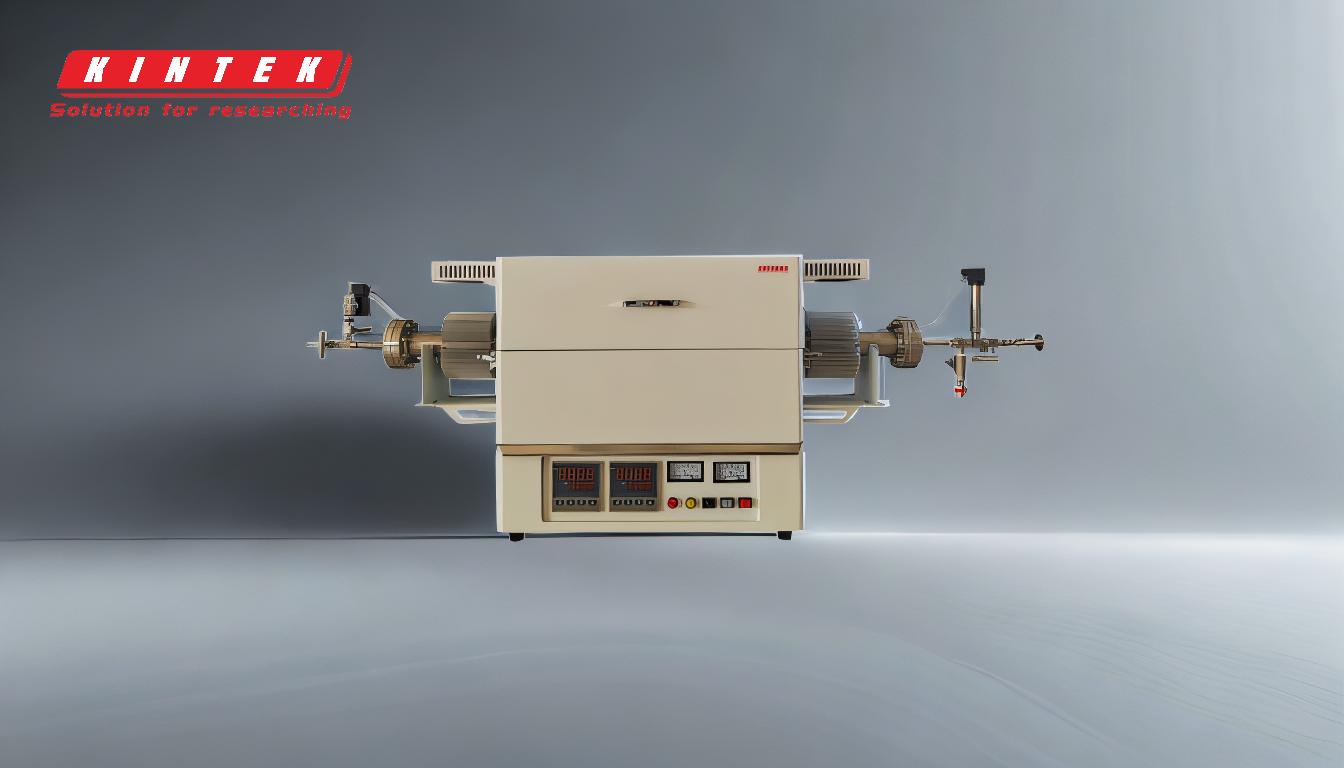
-
Definition of Pressureless Sintering:
- Pressureless sintering is a sintering process that uses only heat, without applying external pressure, to fuse powdered materials into a dense and cohesive structure.
- This method is particularly useful for ceramics and metal-ceramic composites, where external pressure could cause density variations or damage delicate structures.
-
Materials Suitable for Pressureless Sintering:
- Graded Metal-Ceramic Composites: These materials combine the properties of metals and ceramics, making them ideal for applications requiring both strength and thermal resistance.
- Nanoparticle Sintering Aids: Nanoparticles can be added to the powder mixture to enhance sintering by reducing the temperature required for densification and improving the final product's properties.
- Monolithic Molding Techniques: These techniques allow for the creation of complex shapes that can be sintered without the need for external pressure.
-
Steps in the Pressureless Sintering Process:
- Powder Compaction: The first step involves compacting the ceramic or metal powder into a desired shape using methods like cold isostatic pressing, injection molding, or slip casting.
- Pre-Sintering: The compacted powder is then pre-sintered at a lower temperature to remove binders and other organic materials, as well as to strengthen the structure before final sintering.
- Machining: After pre-sintering, the material is machined to its final shape, ensuring precision and accuracy.
- Final Sintering: The machined part is then heated to a high temperature, where the particles fuse together without the need for external pressure.
-
Heating Techniques in Pressureless Sintering:
- Constant-Rate Heating (CRH): The temperature is increased at a constant rate throughout the sintering process. This method is simple but may lead to uneven grain growth.
- Rate-Controlled Sintering (RCS): The heating rate is adjusted during the process to control the densification and grain growth, resulting in a more uniform microstructure.
- Two-Step Sintering (TSS): This technique involves heating the material to a high temperature initially, followed by a lower temperature hold. It helps in achieving fine grain sizes and high density.
-
Advantages of Pressureless Sintering:
- Avoids Density Variations: Since no external pressure is applied, the risk of density variations in the final product is minimized.
- Complex Shapes: Pressureless sintering allows for the production of complex shapes that would be difficult to achieve with pressure-assisted methods.
- Cost-Effective: The absence of external pressure equipment reduces the overall cost of the sintering process.
-
Applications of Pressureless Sintering:
- Ceramics: Used in the production of advanced ceramics for applications in electronics, aerospace, and biomedical fields.
- Metal-Ceramic Composites: Ideal for components that require a combination of metal and ceramic properties, such as cutting tools and wear-resistant parts.
- Nanomaterials: Pressureless sintering is also used in the production of nanomaterials, where precise control over grain size and density is crucial.
-
Comparison with Other Sintering Methods:
- Solid-State Sintering: Involves heating powdered material just below its melting point, relying on atomic diffusion for bonding. Pressureless sintering is a subset of this method.
- Liquid Phase Sintering: Uses a liquid phase to aid in bonding, which is then driven off by heating. Pressureless sintering does not involve a liquid phase.
- Spark Plasma Sintering (SPS): Uses electric current and physical compression to achieve rapid sintering. Pressureless sintering, in contrast, does not use external pressure or electric current.
- Hot Isostatic Pressing (HIP): Applies high pressure and temperature to fuse powder particles, which is different from the pressureless approach.
In summary, pressureless sintering is a versatile and cost-effective method for producing dense and complex ceramic and metal-ceramic components. By relying solely on heat and avoiding external pressure, this technique ensures uniform density and allows for the creation of intricate shapes, making it suitable for a wide range of advanced applications.
Summary Table:
Aspect | Details |
---|---|
Definition | Sintering using heat only, no external pressure. |
Materials | Graded metal-ceramic composites, nanoparticle aids, monolithic molding. |
Process Steps | Powder compaction, pre-sintering, machining, final sintering. |
Heating Techniques | CRH, RCS, TSS for controlled microstructure and grain size. |
Advantages | Avoids density variations, produces complex shapes, cost-effective. |
Applications | Advanced ceramics, metal-ceramic composites, nanomaterials. |
Comparison | Differs from SPS, HIP, and liquid-phase sintering by avoiding pressure. |
Discover how pressureless sintering can enhance your material production—contact us today!