PVD (Physical Vapor Deposition) operates under vacuum conditions to ensure high-quality thin film deposition. The vacuum pressure in PVD systems typically ranges below 10^-5 torr, which is essential for minimizing contamination and optimizing the deposition process. This low-pressure environment increases the mean free path of atoms and ions, reduces gaseous contamination, and influences the plasma's energy distribution. The vacuum pressure is critical for controlling the vaporization, transport, and condensation of the target material, ensuring efficient and defect-free thin film formation. Factors such as system cleanliness, outgassing, and leakage rates also play a significant role in maintaining the required vacuum levels.
Key Points Explained:
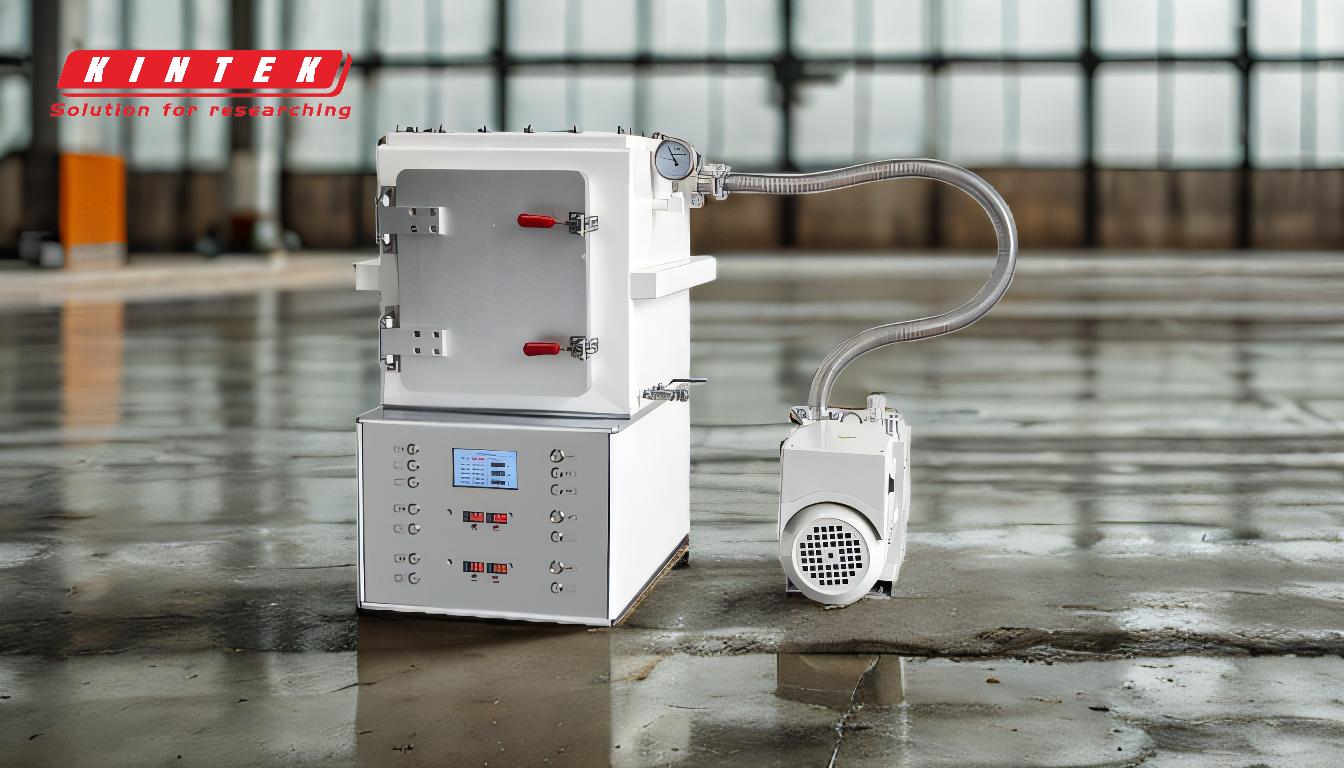
-
Vacuum Pressure Range in PVD:
- PVD processes require a vacuum environment with a pressure typically less than 10^-5 torr.
- This low pressure is necessary to minimize contamination and ensure high-quality thin film deposition.
- The vacuum environment increases the mean free path of atoms and ions, reducing collisions and gaseous contamination.
-
Role of Vacuum in PVD Processes:
- The vacuum environment is crucial for the proper vaporization, transport, and condensation of the target material.
- It influences the enthalpy, density of charged and uncharged particles, and energy distribution in the plasma.
- A well-maintained vacuum ensures efficient and defect-free thin film formation.
-
Factors Affecting Vacuum Levels:
- Outgassing: Materials introduced into the vacuum chamber can release gases, affecting the vacuum level.
- Leakage Rate: The integrity of the vacuum system's seals impacts the ability to maintain low pressure.
- Cleanliness: Contaminants in the chamber can degrade the vacuum quality.
- Ambient Conditions: Humidity and temperature can influence the vacuum system's performance.
-
Impact of Pressure on Deposition:
- High Pressure: Increases the reaction rate but reduces the mean free path, hindering film coverage on steps.
- Low Pressure: Decreases film denseness and can lead to defects such as needle-like structures.
- Optimal Pressure: Balances deposition rate and film quality, ensuring uniform and dense thin films.
-
Plasma and Pressure Interaction:
- Higher gas pressure increases the concentration of reaction gases, enhancing the deposition rate.
- However, excessive pressure can enhance plasma polymerization, reducing the regularity of the growth network and increasing defects.
- Maintaining the correct pressure is essential for controlling the plasma's behavior and ensuring high-quality film growth.
-
Modern Vacuum System Regulation:
- Modern PVD systems regulate vacuum depth as a key variable to achieve desired outcomes.
- The required pressure can vary significantly depending on the specific application and materials being used.
- Advanced systems are designed to maintain precise vacuum levels, ensuring consistent and high-quality deposition processes.
-
Advantages of PVD Vacuum Coating:
- PVD vacuum coating machines are known for their fast deposition speed and low deposition temperature.
- They use environmentally friendly physical means, making them suitable for coating precision and complex tools.
- The vacuum environment ensures minimal contamination and high-quality thin film deposition.
By understanding and controlling the vacuum pressure in PVD systems, manufacturers can optimize the deposition process, ensuring high-quality, defect-free thin films for various applications.
Summary Table:
Key Aspect | Details |
---|---|
Vacuum Pressure Range | Below 10^-5 torr for minimal contamination and optimal deposition. |
Role of Vacuum | Controls vaporization, transport, and condensation of target material. |
Factors Affecting Vacuum | Outgassing, leakage rate, cleanliness, and ambient conditions. |
Pressure Impact | High pressure reduces mean free path; low pressure causes defects. |
Plasma Interaction | Higher pressure enhances deposition rate but may increase defects. |
Modern Regulation | Advanced systems maintain precise vacuum levels for consistent outcomes. |
Advantages of PVD Coating | Fast deposition, low temperature, and environmentally friendly processes. |
Ready to optimize your PVD process? Contact us today for expert guidance!