The principle of the quenching effect involves rapidly cooling a material, typically a metal, from a high temperature to a lower temperature to alter its physical properties, such as hardness and strength. This process is often used in metallurgy to achieve desired material characteristics. While the references provided do not directly address quenching, they offer insights into related principles like electromagnetic induction, ultrasonic cavitation, and vibration, which can be analogously applied to understand the quenching effect. For instance, the rapid cooling in quenching can be compared to the rapid heat generation in induction heating or the disruptive forces in ultrasonic homogenization.
Key Points Explained:
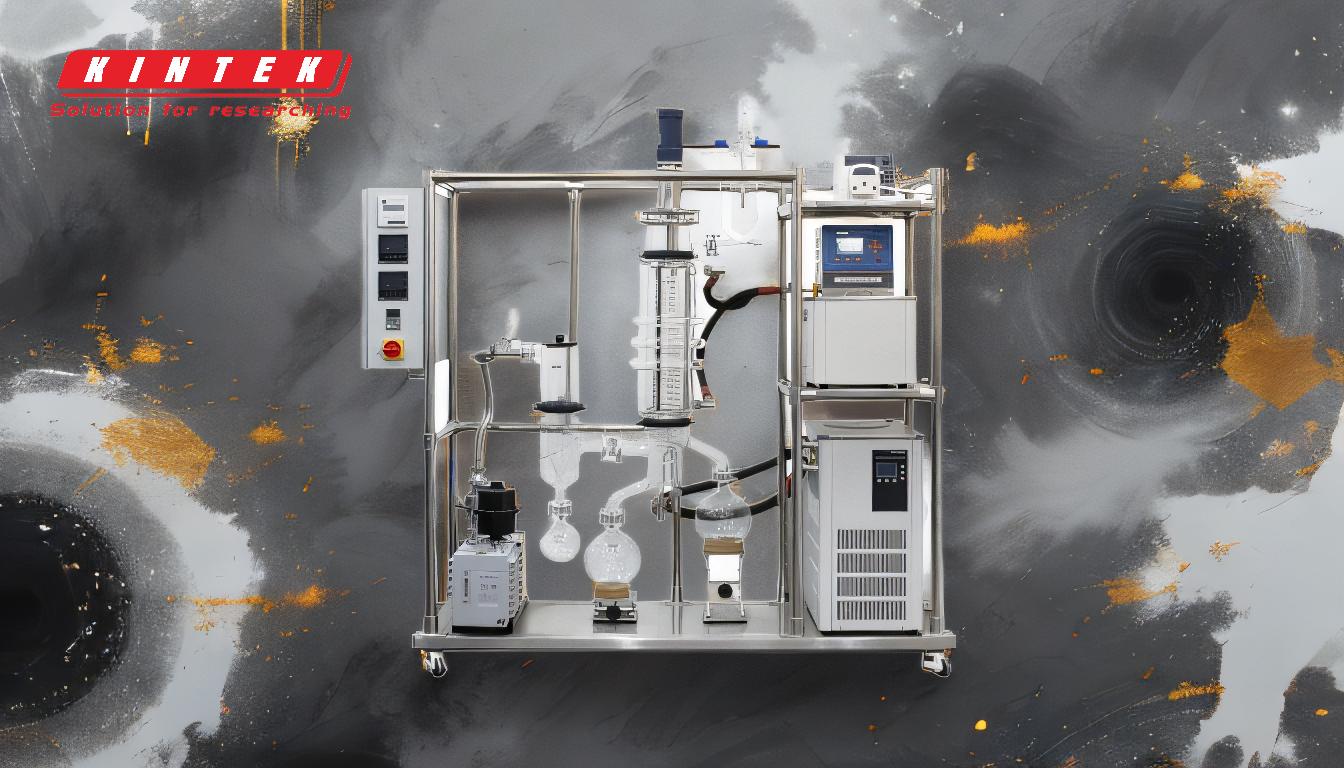
-
Rapid Cooling Mechanism:
- Quenching involves rapidly cooling a material to alter its microstructure and properties. This is analogous to how sieve shakers use vibration to separate materials based on particle size, where rapid movement causes separation. Similarly, in quenching, rapid cooling causes the material to transition from a high-energy state to a low-energy state, resulting in a hardened structure.
-
Heat Transfer Principles:
- The quenching process relies on efficient heat transfer, similar to how induction heating uses electromagnetic fields to generate heat in conductive materials. In quenching, the heat is rapidly transferred from the material to the cooling medium (e.g., water, oil, or air), causing the material to cool quickly and solidify in a desired state.
-
Material Transformation:
- Quenching transforms the material's microstructure, often leading to increased hardness and strength. This transformation can be compared to the disruption caused by ultrasonic homogenizers, where ultrasonic cavitation disrupts components at a microscopic level. In quenching, the rapid cooling disrupts the material's atomic arrangement, leading to a more rigid structure.
-
Applications in Metallurgy:
- Quenching is widely used in metallurgy to enhance the mechanical properties of metals, such as steel. This is similar to how autoclaves use high pressure and moist heat to sterilize equipment by altering the microbial structure. In quenching, the altered microstructure of the metal results in improved durability and resistance to wear.
-
Comparison with Other Processes:
- The principles of quenching can be compared to other processes like the operation of a two-component evaporation boat, where material composition affects performance. In quenching, the choice of cooling medium and rate of cooling significantly impact the final properties of the material, just as the composition of the evaporation boat affects its lifespan and efficiency.
By understanding these key points, one can appreciate the quenching effect as a critical process in material science, driven by principles of rapid cooling, heat transfer, and material transformation.
Summary Table:
Key Aspect | Description |
---|---|
Rapid Cooling Mechanism | Rapidly cools materials to alter microstructure, similar to vibration in sieve shakers. |
Heat Transfer Principles | Efficient heat transfer, akin to induction heating, ensures quick solidification. |
Material Transformation | Transforms microstructure, increasing hardness and strength via atomic disruption. |
Applications in Metallurgy | Enhances metal properties like durability and wear resistance through altered microstructure. |
Comparison with Other Processes | Similar to how material composition affects evaporation boats, cooling medium impacts final properties. |
Want to learn more about how quenching can optimize your material properties? Contact our experts today!