Cold Isostatic Pressing (CIP) is a manufacturing process that uses hydraulic pressure to compact powdered materials into a desired shape. This process involves placing the powder into a flexible mold, sealing it, and then subjecting it to uniform pressure from all directions using a liquid medium. The key advantage of CIP is its ability to produce complex shapes with high green density and uniform properties. The process is based on Pascal’s law, ensuring that the pressure is evenly distributed throughout the material. CIP can be performed using either the wet-bag or dry-bag technique, depending on the specific requirements of the application. The resulting compacted powder body, or green body, is then sintered at high temperatures to achieve the final product.
Key Points Explained:
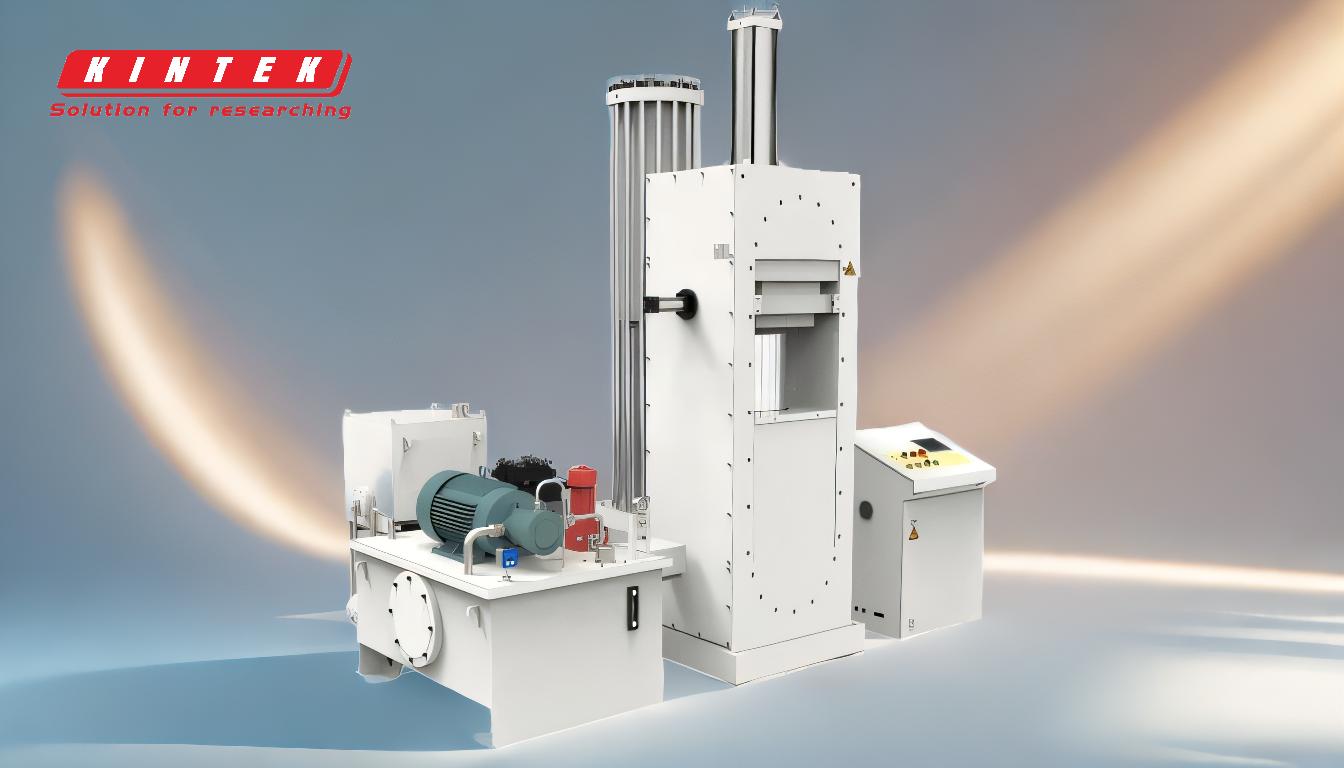
-
Basic Principle of Cold Isostatic Pressing:
- CIP operates on Pascal’s law, which states that pressure applied to an enclosed fluid is transmitted uniformly in all directions. This ensures that the powder within the mold experiences equal pressure from all sides, leading to uniform compaction and density.
- The process is particularly effective for shaping and consolidating powdered materials, especially when intricate shapes or high green density is required.
-
Steps Involved in the CIP Process:
- Loading the Powder: The powdered material is loaded into a flexible mold, typically made of elastomers like polyurethane. This mold can be designed to create complex shapes.
- Sealing the Mold: The mold is sealed to prevent any leakage of the powder or the pressurizing fluid during the process.
- Applying Pressure: The sealed mold is placed in a pressure vessel filled with a liquid, usually water with a corrosion inhibitor. Hydraulic pressure is applied uniformly from all directions, compacting the powder into a solid green body.
- Releasing Pressure and Removing the Green Body: After the desired pressure is maintained for a specific duration, the pressure is released, and the compacted powder body is removed from the mold.
-
Wet-Bag vs. Dry-Bag Techniques:
- Wet-Bag Technique: In this method, the flexible mold containing the powder is submerged in a pressure vessel filled with a pressurizing fluid. The mold is removed and replaced after each pressing cycle.
- Dry-Bag Technique: Here, the flexible mold is fixed within the pressure vessel, and the powder is loaded without removing the mold. This technique is more suitable for high-volume production and automated processes.
-
Applications and Advantages:
- CIP is widely used in industries such as ceramics, metallurgy, and advanced materials. It is particularly useful for producing components with complex geometries, uniform density, and high strength.
- The process allows for the compaction of materials that are difficult to press using conventional methods, such as hard metals, ceramics, and composites.
-
Integration with High-Temperature Processing:
- In some applications, such as the preparation of solid electrolytes, CIP is combined with high-temperature sintering. The green body obtained from CIP is sintered at high temperatures to achieve the final product with the desired properties.
- For example, in the preparation of solid electrolytes, the process involves steps like calcining, mixing, ball milling, drying, and sintering, with CIP being a critical step in forming the green body before final sintering.
-
Equipment and Safety Considerations:
- The pressure chamber used in CIP must be designed to withstand severe cyclic loading, as the process involves repeated application of high pressures.
- Safety measures are crucial, especially when dealing with high-pressure fluids. The use of corrosion inhibitors in the pressurizing fluid helps protect the equipment and ensures consistent performance.
By understanding these key points, one can appreciate the versatility and effectiveness of Cold Isostatic Pressing in various industrial applications. The process's ability to produce uniform and complex shapes makes it an invaluable technique in modern manufacturing.
Summary Table:
Aspect | Details |
---|---|
Basic Principle | Based on Pascal’s law, ensuring uniform pressure distribution. |
Steps in CIP Process | Loading powder, sealing mold, applying pressure, and removing green body. |
Techniques | Wet-bag (mold submerged) or dry-bag (mold fixed). |
Applications | Ceramics, metallurgy, advanced materials, and complex geometries. |
Advantages | High green density, uniform properties, and ability to compact hard materials. |
Safety Considerations | Pressure chamber must withstand cyclic loading; corrosion inhibitors used. |
Discover how Cold Isostatic Pressing can enhance your manufacturing process—contact our experts today!