Graphene transfer is a critical process in the fabrication of graphene-based devices, where graphene is moved from its growth substrate (often copper or nickel) to a target substrate (such as SiO2/Si or flexible polymers). The process involves several steps, including coating the graphene with a supporting polymer, etching away the metal substrate, and transferring the graphene to the desired surface. The goal is to achieve a clean, defect-free transfer with minimal contamination and damage to the graphene lattice. The process requires precision and careful handling to ensure the integrity and functionality of the graphene for applications in electronics, sensors, and other advanced technologies.
Key Points Explained:
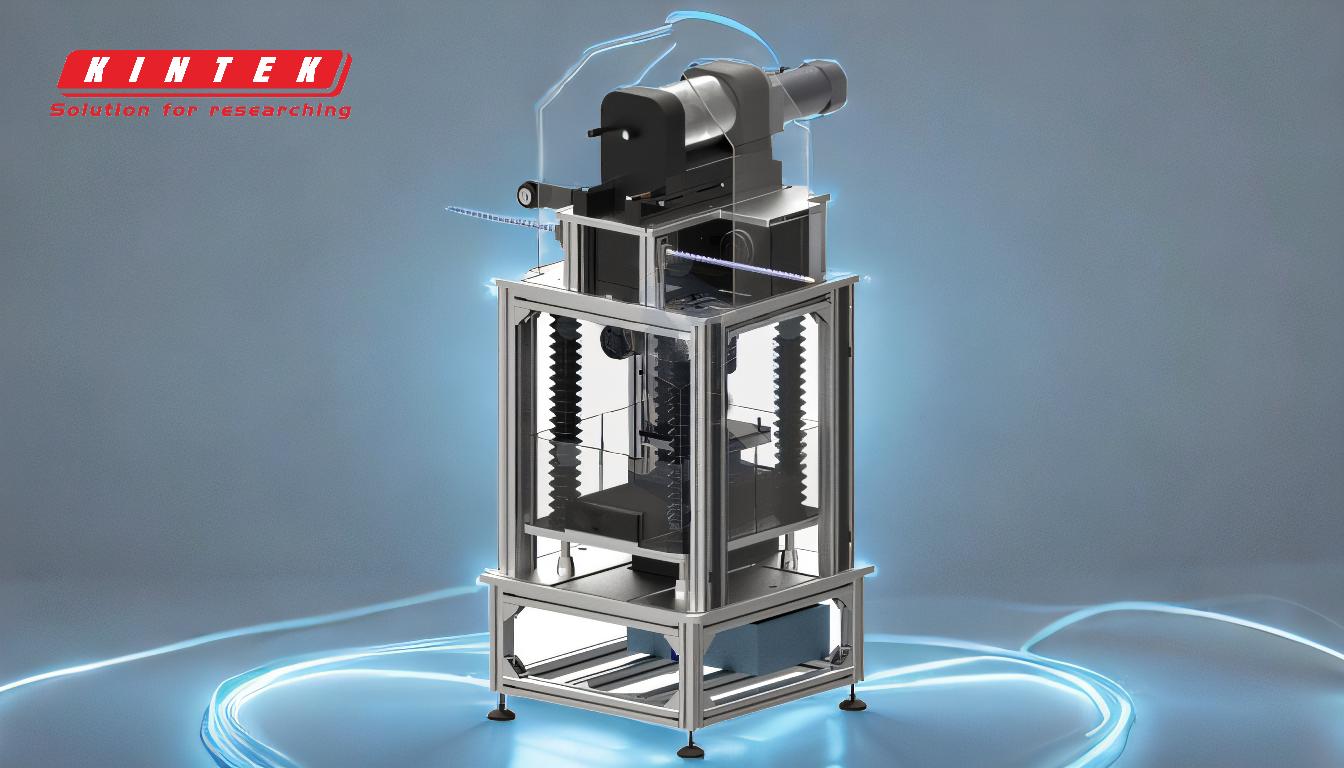
-
Preparation of Graphene on Growth Substrate:
- Graphene is typically grown on a metal substrate, such as copper or nickel, using chemical vapor deposition (CVD). This substrate provides a surface for the graphene to form a uniform layer.
- The quality of the graphene, including its thickness and defect density, depends on the growth conditions, such as temperature, gas flow rates, and pressure.
-
Application of a Polymer Support Layer:
- To facilitate the transfer, a polymer layer (commonly polymethyl methacrylate, PMMA) is spin-coated onto the graphene surface. This layer acts as a support to hold the graphene together during the subsequent steps.
- The polymer must be uniformly applied to ensure that the graphene remains intact and does not tear or fold during transfer.
-
Etching of the Metal Substrate:
- The metal substrate is etched away using a chemical etchant, such as ferric chloride (FeCl3) for copper or ammonium persulfate ((NH4)2S2O8) for nickel. This step dissolves the metal, leaving the graphene-polymer bilayer floating on the surface of the etchant solution.
- Care must be taken to avoid over-etching, which can damage the graphene or leave residual metal particles.
-
Transfer to the Target Substrate:
- The graphene-polymer bilayer is carefully lifted from the etchant solution and placed onto the target substrate (e.g., SiO2/Si wafer or flexible polymer). This step requires precision to align the graphene and avoid introducing wrinkles or bubbles.
- The target substrate is often pre-treated to enhance adhesion, such as by cleaning with solvents or applying a thin adhesive layer.
-
Removal of the Polymer Support Layer:
- After transfer, the polymer support layer is removed using solvents like acetone or isopropyl alcohol. This step must be done gently to avoid damaging the graphene.
- Residual polymer can affect the electrical and mechanical properties of the graphene, so thorough cleaning is essential.
-
Post-Transfer Cleaning and Characterization:
- The transferred graphene is cleaned to remove any remaining contaminants or residues. Techniques such as annealing in a controlled atmosphere or rinsing with deionized water may be used.
- Characterization techniques, such as Raman spectroscopy, atomic force microscopy (AFM), and electrical measurements, are employed to assess the quality of the transferred graphene, including its defect density, thickness, and electrical conductivity.
-
Challenges and Considerations:
- The transfer process can introduce defects, such as cracks, folds, or contamination, which can degrade the performance of graphene-based devices.
- Factors like the choice of polymer, etchant, and target substrate, as well as environmental conditions (e.g., humidity, temperature), play a significant role in the success of the transfer.
- Advanced techniques, such as roll-to-roll transfer or electrochemical delamination, are being developed to improve the scalability and quality of graphene transfer.
By following these steps meticulously, researchers and engineers can achieve high-quality graphene transfer, enabling the development of next-generation electronic and optoelectronic devices.
Summary Table:
Step | Description |
---|---|
1. Preparation of Graphene | Grow graphene on a metal substrate (e.g., copper or nickel) using CVD. |
2. Polymer Support Layer | Apply a polymer (e.g., PMMA) to support graphene during transfer. |
3. Etching of Metal Substrate | Etch away the metal substrate using chemical etchants (e.g., FeCl3 for copper). |
4. Transfer to Target Substrate | Place graphene-polymer bilayer onto the target substrate (e.g., SiO2/Si). |
5. Remove Polymer Layer | Gently dissolve the polymer layer using solvents (e.g., acetone). |
6. Post-Transfer Cleaning | Clean graphene to remove contaminants and residues. |
7. Characterization | Use techniques like Raman spectroscopy and AFM to assess graphene quality. |
Need expert guidance on graphene transfer? Contact us today to optimize your process!