Heat treatment furnaces are essential in industrial processes for altering the physical and sometimes chemical properties of materials, primarily metals, through controlled heating and cooling. The process involves three fundamental steps: heating the material to a specific temperature, holding it at that temperature for a predetermined duration, and then cooling it according to specified methods. The type of furnace and the specific heat treatment process can vary significantly depending on the material and the desired outcome. Continuous furnaces, for instance, are designed for high-volume production, utilizing conveyor belts or other automated systems to move parts through the furnace efficiently. In contrast, vacuum furnaces create a low-pressure environment to prevent oxidation and ensure uniform heat distribution. Regardless of the furnace type, precise temperature control and uniform heat distribution are critical to achieving the desired material properties.
Key Points Explained:
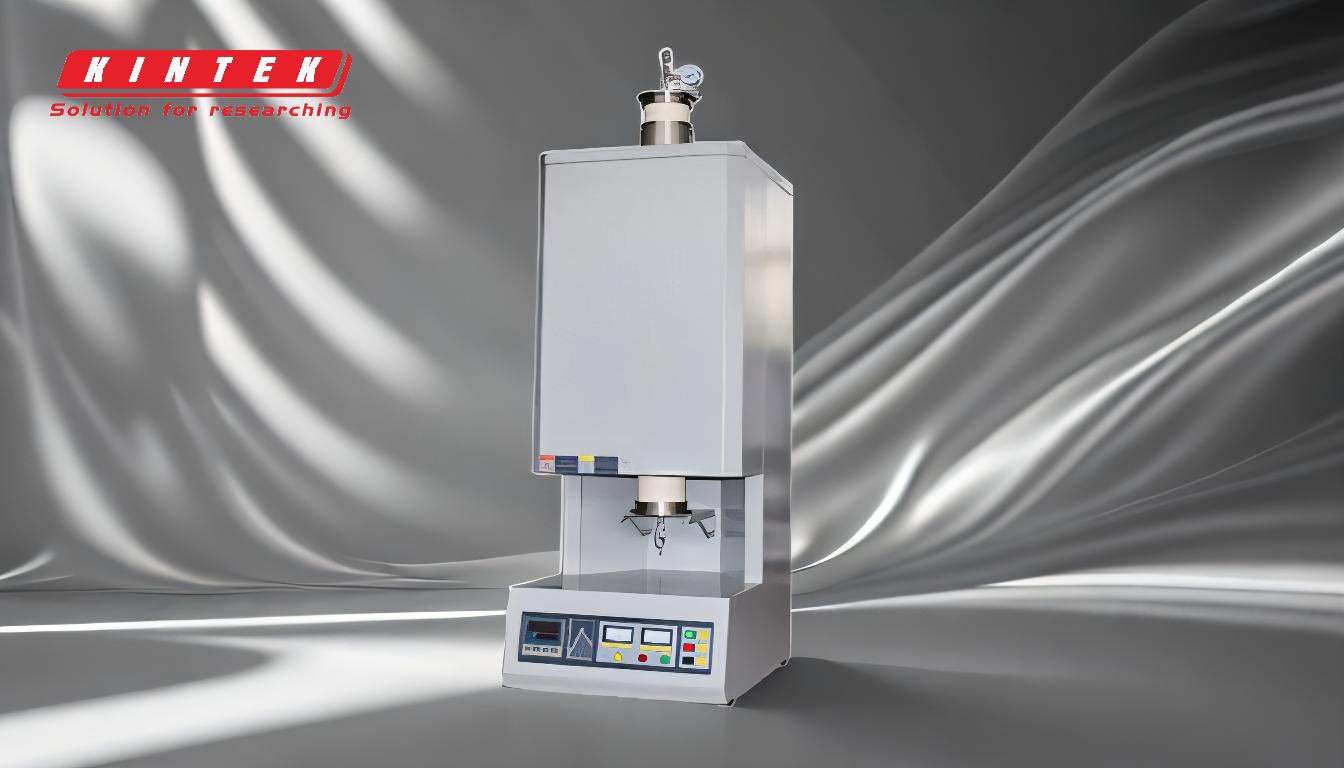
-
Preparation:
- Cleaning and Inspection: Before starting the heat treatment process, the furnace must be cleaned, and all components should be checked to ensure they are functioning correctly. Any debris or contaminants inside the furnace could affect the quality of the heat treatment.
- Material Preparation: The items to be heated must also be prepared. This may involve cleaning the parts, ensuring they are free of oils or other contaminants, and arranging them in the furnace in a way that allows for even heat distribution.
-
Heating:
- Temperature Control: The furnace is powered on, and the temperature controller is adjusted to the desired temperature. The heating process begins, and the furnace gradually reaches the set temperature. During this phase, more heat is required to raise the temperature to the desired level.
- Uniform Heat Distribution: It is crucial that the heat is distributed evenly throughout the furnace to ensure that all parts are heated uniformly. This is especially important in large furnaces or when treating multiple parts simultaneously.
-
Holding:
- Maintaining Temperature: Once the furnace reaches the desired temperature, the temperature controller is adjusted to a holding state. This maintains the temperature at a constant level for a specified period, known as the "soak time." The duration of this phase depends on the material being treated and the desired properties.
- Soak Time: The soak time can vary significantly, from a few seconds to several hours, depending on the material and the specific heat treatment process. During this time, the material undergoes the necessary metallurgical changes.
-
Cooling:
- Controlled Cooling: After the holding period, the material must be cooled according to prescribed methods. The cooling rate is critical and can significantly affect the final properties of the material. Cooling can be done in air, oil, water, or a controlled atmosphere, depending on the requirements.
- Post-Treatment Inspection: Once the material has cooled, it may undergo inspection to ensure that the desired properties have been achieved. This could involve checking for hardness, strength, or other material characteristics.
-
Special Considerations for Different Furnace Types:
- Continuous Furnaces: These are designed for high-volume production and often use conveyor belts or other automated systems to move parts through the furnace. The process time is usually shorter, measured in minutes rather than hours, making them ideal for environments where thousands of identical parts are processed.
- Vacuum Furnaces: These furnaces create a low-pressure environment, often replacing oxygen with inert gases like argon to prevent oxidation. The heating and cooling processes are tightly controlled, often through computer systems, to ensure uniformity and repeatability. Vacuum furnaces are particularly useful for treating materials that are sensitive to oxidation or require very precise temperature control.
-
Heat Source and Atmosphere:
- Heat Source: The heat source in a heat treatment furnace can be gas-fueled or electrically energized. The choice of heat source can affect the efficiency and uniformity of the heating process.
- Atmosphere Control: The atmosphere inside the furnace can also be controlled to achieve specific results. For example, a reducing atmosphere might be used to prevent oxidation, while a carburizing atmosphere could be used to increase the carbon content of the material's surface.
-
Safety and Maintenance:
- Safety Precautions: Operating a heat treatment furnace involves high temperatures and potentially hazardous materials, so safety precautions are essential. This includes proper ventilation, protective gear, and regular maintenance to ensure the furnace operates safely and efficiently.
- Regular Maintenance: Regular maintenance of the furnace is crucial to ensure its longevity and consistent performance. This includes checking and replacing heating elements, inspecting seals and gaskets, and ensuring that all control systems are functioning correctly.
By following these steps and considerations, the heat treatment process can be effectively managed to achieve the desired material properties, whether for industrial applications, manufacturing, or other specialized uses.
Summary Table:
Step | Key Details |
---|---|
Preparation | Clean furnace, inspect components, and prepare materials for even heat exposure. |
Heating | Adjust temperature controller for uniform heat distribution. |
Holding | Maintain temperature during soak time for metallurgical changes. |
Cooling | Cool material at controlled rates using air, oil, water, or controlled atmospheres. |
Furnace Types | Continuous furnaces for high-volume production; vacuum furnaces for precision. |
Heat Source | Gas-fueled or electrically energized heat sources for efficiency. |
Safety & Maintenance | Regular maintenance and safety precautions ensure optimal performance. |
Discover how heat treatment furnaces can enhance your industrial processes—contact us today for expert guidance!