Hot isostatic pressing (HIP) is a manufacturing process that combines high temperature and isostatic pressure to densify materials, improve mechanical properties, and bond or clad materials. It is widely used in industries such as aerospace, automotive, and medical devices. The process involves several key steps, including powder preparation, mold design, powder filling, degassing, sealing, pressing, and post-processing. HIP can be performed using wet-bag or dry-bag techniques, depending on the application. It is particularly effective when combined with advanced techniques like 3D printing, as it reduces production time and costs while enhancing material properties.
Key Points Explained:
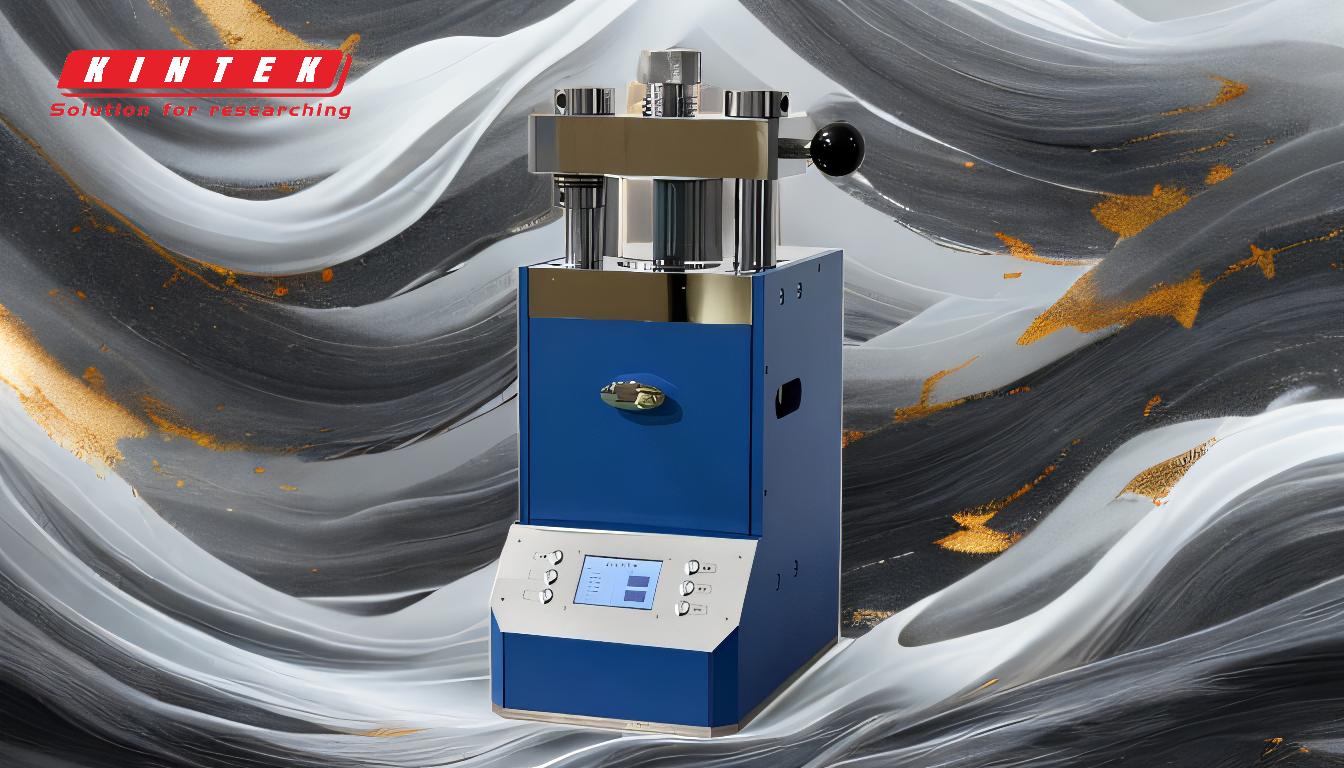
-
Definition and Purpose of Hot Isostatic Pressing (HIP):
- HIP is a process that uses high temperature and uniform hydrostatic pressure to densify materials, improve their mechanical properties, and bond or clad multiple materials together. It is particularly useful for materials in powder or solid form, ensuring uniformity and eliminating porosity.
-
Key Steps in the HIP Process:
- Powder Preparation: The raw material is prepared in powder form, ensuring it meets the required specifications for particle size and distribution.
- Cladding Design and Manufacturing: A flexible mold (often made of polyurethane) is designed to hold the powder. The mold must withstand high pressures and temperatures.
- Powder Filling and Degassing Sealing: The powder is loaded into the mold, and the mold is sealed after degassing to remove any trapped air or gases.
- Hot Isostatic Pressing: The sealed mold is placed in a pressure vessel, where it is subjected to high temperature and uniform pressure using a liquid medium (e.g., gas or oil). This step compacts the powder into a solid mass.
- Removal of Cladding and Post-Processing: After pressing, the mold is removed, and the compacted material undergoes additional processing, such as machining or heat treatment, to achieve the final product.
-
Wet-Bag vs. Dry-Bag Techniques:
- Wet-Bag Technique: The flexible mold containing the powder is submerged in a pressure vessel filled with a pressurizing fluid. Pressure is applied uniformly to the external surface of the mold, compressing the powder. This method is suitable for small to medium-sized parts and takes 5 to 30 minutes.
- Dry-Bag Technique: The flexible mold is fixed inside the pressure vessel, and powder is loaded without removing the mold. This method is more efficient for large-scale production and reduces the time required for mold handling.
-
Applications and Advantages of HIP:
- HIP is used in industries requiring high-performance materials, such as aerospace (for turbine blades), automotive (for engine components), and medical devices (for implants). It improves material density, strength, and fatigue resistance.
- When combined with 3D printing, HIP reduces manufacturing time and costs while enhancing the mechanical properties of the final product.
-
Capacities and Equipment:
- HIP equipment is categorized into small-sized, medium-sized, and large-sized presses, depending on the volume and size of the parts being processed. The choice of equipment depends on the specific application and production requirements.
By following these steps and techniques, hot isostatic pressing ensures the production of high-quality, defect-free materials with superior mechanical properties.
Summary Table:
Key Steps in HIP Process | Details |
---|---|
Powder Preparation | Raw material is prepared in powder form with specific particle size and distribution. |
Cladding Design | Flexible molds (e.g., polyurethane) are designed to withstand high pressures and temperatures. |
Powder Filling & Degassing | Powder is loaded into the mold, degassed, and sealed to remove air or gases. |
Hot Isostatic Pressing | The sealed mold is subjected to high temperature and uniform pressure in a pressure vessel. |
Post-Processing | Mold is removed, and the material undergoes machining or heat treatment for final use. |
Wet-Bag vs. Dry-Bag | Wet-bag: Submerged in pressurizing fluid; Dry-bag: Fixed mold for large-scale production. |
Applications | Aerospace, automotive, and medical devices for improved density, strength, and fatigue resistance. |
Discover how hot isostatic pressing can enhance your manufacturing process—contact us today to learn more!