Isostatic pressing is a manufacturing process that uses uniform hydrostatic pressure to compact powdered materials into dense, uniform shapes. The process involves placing powder in a flexible mold, sealing it, and applying equal pressure from all directions using a liquid medium. This can be achieved through either the wet-bag or dry-bag technique, depending on the application. The compacted powder is then removed from the mold after pressure release. This method is widely used in industries requiring high-density, complex-shaped components, such as ceramics, metals, and composites.
Key Points Explained:
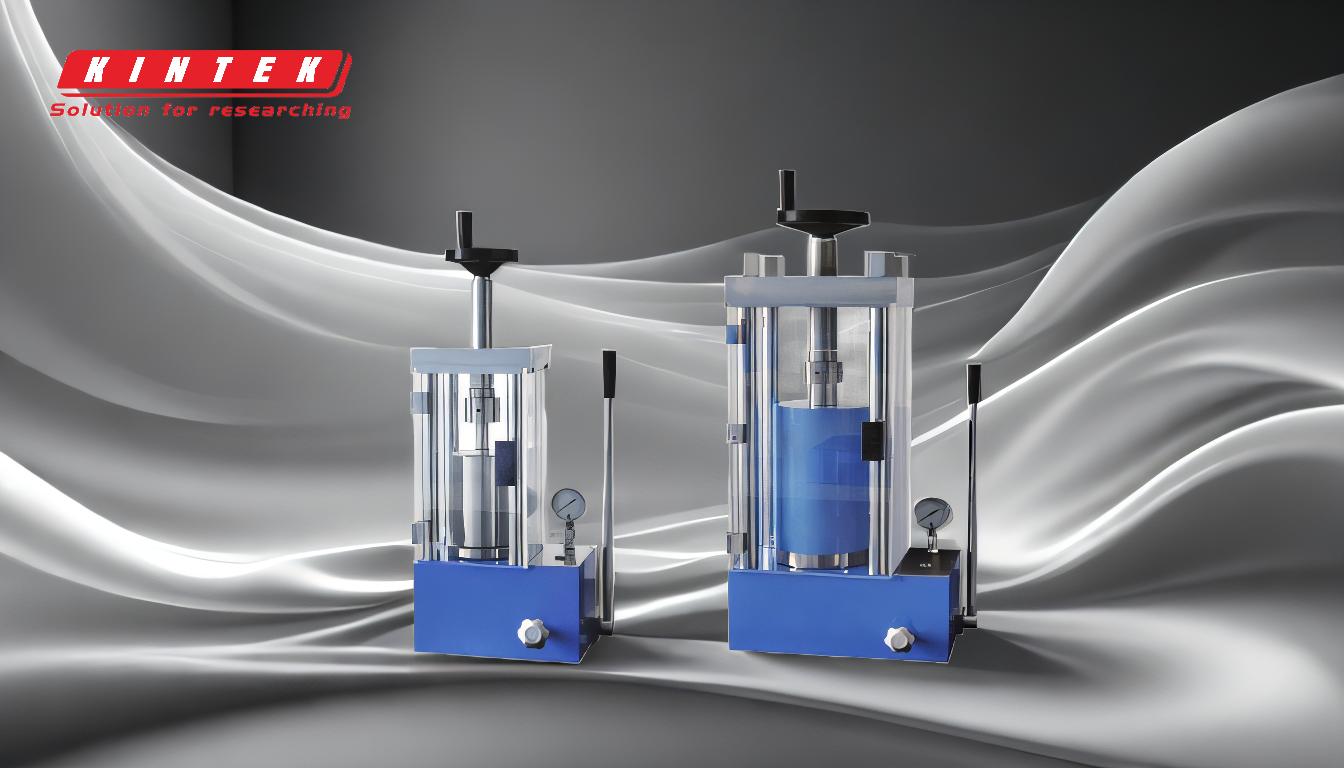
-
Flexible Mold and Powder Loading:
- The process begins by loading the powder into a flexible mold, typically made of materials like polyurethane. This mold can conform to the shape of the powder, ensuring uniform compaction.
- The mold is then sealed to prevent any leakage of the powder or the pressurizing medium during the process.
-
Application of Hydrostatic Pressure:
- The sealed mold is placed inside a pressure vessel, which is then filled with a liquid medium (often water or an oil-water mixture).
- Pressure is applied uniformly from all directions, ensuring that the powder is compressed evenly, regardless of the shape or size of the mold.
- This uniform pressure is the defining characteristic of isostatic pressing, distinguishing it from other compaction methods.
-
Wet-Bag vs. Dry-Bag Techniques:
- Wet-Bag Technique: In this method, the flexible mold containing the powder is submerged in the pressure vessel. After pressing, the mold is removed from the vessel.
- Dry-Bag Technique: Here, the flexible mold is fixed within the pressure vessel, and powder is loaded and unloaded without removing the mold. This technique is more suitable for high-volume production.
-
Pressure and Temperature Control:
- The pressure in the vessel can reach extremely high levels, up to 100,000 psi, depending on the material and desired density.
- In some cases, the process may involve elevating the temperature to enhance compaction, especially in hot isostatic pressing (HIP).
-
Release of Pressure and Removal of Compacted Powder:
- After the desired pressure and, if applicable, temperature are maintained for a specific duration, the pressure is gradually released.
- The compacted powder body, now in the desired shape, is removed from the mold. This product typically has high density and uniform properties.
-
Applications and Capacities:
- Isostatic pressing is used in various industries, including aerospace, automotive, and medical, for producing components with complex shapes and high density.
- The process can be scaled to different capacities, from small-sized HIP for laboratory use to large-sized HIP for industrial production.
-
Advantages of Isostatic Pressing:
- Uniform density and microstructure of the final product.
- Ability to produce complex shapes with minimal machining required.
- Suitable for a wide range of materials, including ceramics, metals, and composites.
By understanding these key points, a purchaser of a cold isostatic pressing machine can better appreciate the capabilities and applications of this technology, ensuring they select the right equipment for their specific needs.
Summary Table:
Step | Description |
---|---|
Flexible Mold & Powder Loading | Powder is loaded into a flexible mold, which is sealed to prevent leakage. |
Hydrostatic Pressure Application | Uniform pressure is applied from all directions using a liquid medium. |
Wet-Bag vs. Dry-Bag Techniques | Wet-bag: Mold is submerged; Dry-bag: Mold remains fixed for high-volume production. |
Pressure & Temperature Control | Pressure up to 100,000 psi; temperature may be elevated for enhanced compaction. |
Pressure Release & Removal | Compacted powder is removed after pressure release, resulting in a dense product. |
Applications | Used in aerospace, automotive, and medical industries for high-density components. |
Advantages | Uniform density, complex shapes, and suitability for ceramics, metals, and composites. |
Discover how isostatic pressing can transform your manufacturing process—contact our experts today for tailored solutions!