The sintering process is a critical method in materials science and manufacturing, used to create solid, low-porosity structures from powdered materials without melting them completely. It involves several key steps: composition (mixing primary materials and coupling agents), compression (pressing the powder into the desired shape), and heating (to remove the coupling agent and fuse the primary material). The process leverages heat and pressure to diffuse atoms across particle boundaries, bonding them into a cohesive structure. This method is particularly useful for materials with high melting points, such as tungsten and molybdenum, and is widely applied in industries like ceramics, metallurgy, and powder metallurgy.
Key Points Explained:
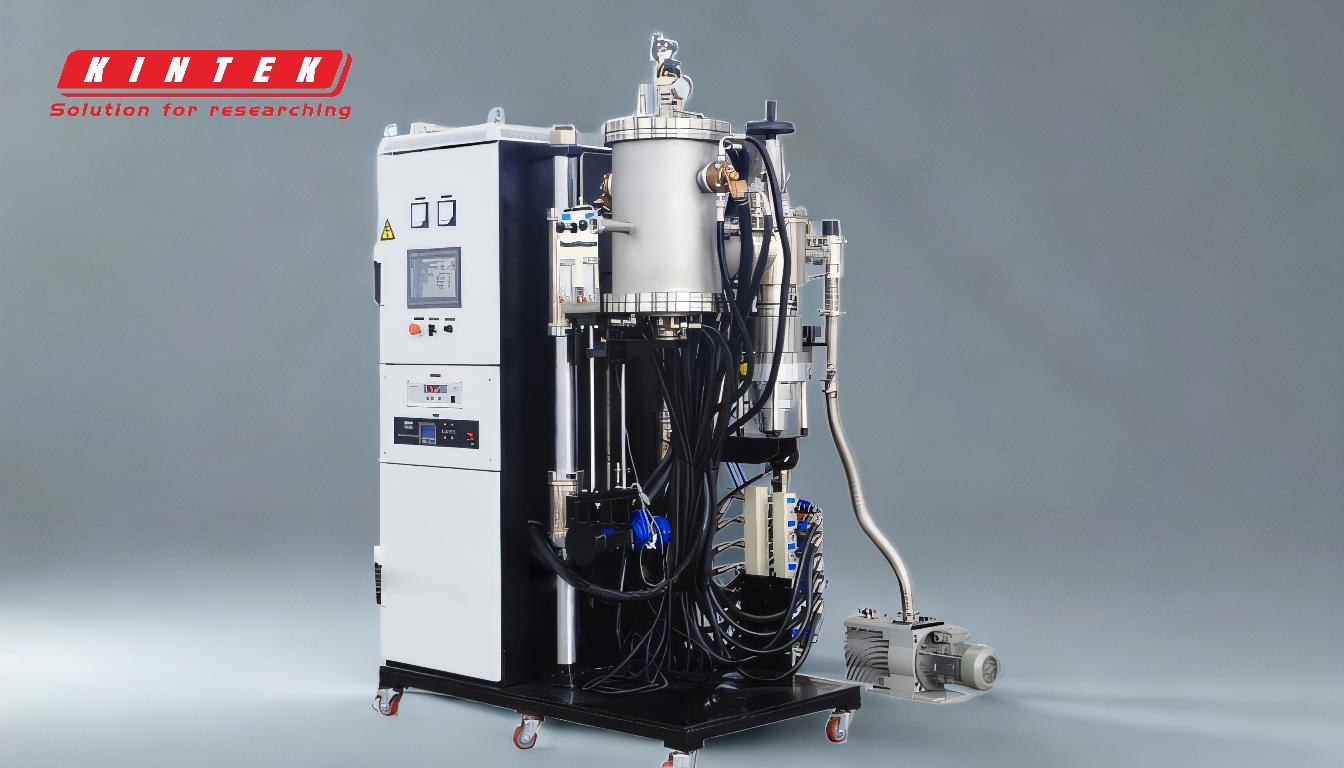
-
Composition and Powder Preparation:
- The process begins with selecting the appropriate powder composition, which may include metals like iron, nickel, molybdenum, or copper, along with lubricants or coupling agents.
- The powder is carefully mixed to ensure uniformity, which is critical for achieving consistent material properties in the final product.
- For ceramic sintering, the powder is often loaded into a furnace, and the environment is controlled (e.g., vacuum) to remove impurities and gases.
-
Compaction (Pressing):
- The mixed powder is then compacted using high pressure to form a "green" part, which has an initial shape but lacks structural integrity.
- Compaction is typically done using a die press, which applies force to shape the powder into the desired geometry.
- This step is crucial for achieving the correct density and shape before sintering.
-
Heating and Sintering:
- The compacted powder is heated in a furnace to a temperature just below its melting point. This allows the particles to bond without liquefying.
- During heating, atoms diffuse across particle boundaries, fusing them together and reducing porosity.
- In some cases, liquid phase sintering (LPS) is used to accelerate particle merging by introducing a liquid phase that aids in densification.
-
Pressurization (Hot Press Sintering):
- In hot press sintering, pressure is applied simultaneously with heating to enhance densification and reduce porosity.
- This method is particularly effective for ceramics and other materials requiring high structural integrity.
-
Cooling and Solidification:
- After sintering, the material is gradually cooled to room temperature to solidify into a unified mass.
- Controlled cooling prevents cracking or warping, ensuring the final product maintains its shape and structural properties.
-
Applications and Materials:
- Sintering is widely used for materials with high melting points, such as tungsten, molybdenum, and ceramics.
- It is a key process in powder metallurgy for creating components like gears, bearings, and filters, as well as in advanced manufacturing techniques like 3D printing.
By following these steps, the sintering process transforms powdered materials into durable, high-performance components with minimal porosity and optimal mechanical properties. This makes it an indispensable technique in modern manufacturing and materials engineering.
Summary Table:
Step | Description |
---|---|
1. Composition | Mix primary materials and coupling agents for uniformity. |
2. Compaction | Press powder into the desired shape using high pressure. |
3. Heating | Heat below melting point to bond particles and reduce porosity. |
4. Pressurization | Apply pressure during heating for enhanced densification (hot press sintering). |
5. Cooling | Gradually cool to solidify into a unified mass, preventing cracks or warping. |
6. Applications | Used for high-melting-point materials like tungsten, ceramics, and 3D printing. |
Discover how sintering can revolutionize your manufacturing process—contact us today to learn more!