Physical Vapor Deposition (PVD) is a widely used technique in semiconductor manufacturing to deposit thin films of material onto a substrate. The process involves converting a solid material into a vapor phase in a vacuum environment and then condensing it onto a substrate to form a thin, durable, and high-quality film. PVD is particularly valued for its ability to produce coatings that are highly resistant to wear, corrosion, and scratching, making it ideal for semiconductor applications. The process typically involves several key steps, including vaporization of the target material, transportation of the vaporized material to the substrate, and condensation of the material onto the substrate to form a thin film. Advanced monitoring and control mechanisms, such as quartz crystal rate monitors, ensure precise control over film thickness and deposition rates.
Key Points Explained:
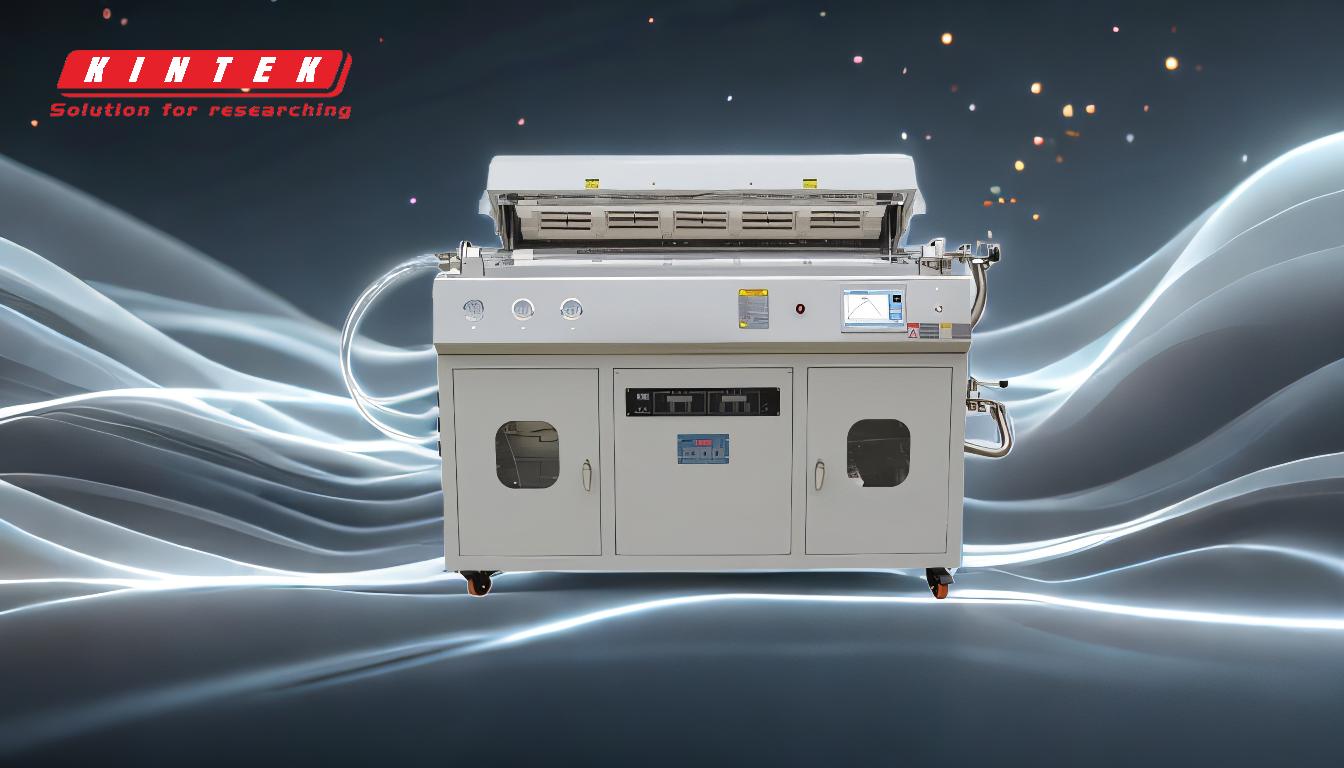
-
Vaporization of the Target Material:
- The PVD process begins with the vaporization of a solid precursor material. This is achieved through physical means such as:
- Sputtering: Bombarding the target material with high-energy ions to dislodge atoms from the surface.
- Evaporation: Heating the material until it vaporizes.
- Laser Pulses or Arc Discharge: Using focused energy sources to vaporize the material.
- The vaporization occurs in a vacuum chamber to minimize contamination from background gases and ensure a clean deposition environment.
- The PVD process begins with the vaporization of a solid precursor material. This is achieved through physical means such as:
-
Transportation of Vaporized Material:
- Once the material is vaporized, the atoms or molecules are transported across a low-pressure region to the substrate. This is typically done in a vacuum environment to prevent unwanted chemical reactions and ensure the purity of the deposited film.
- The transportation process is influenced by the vacuum level, the distance between the target and the substrate, and the energy of the vaporized particles.
-
Condensation on the Substrate:
- The vaporized material condenses onto the substrate to form a thin film. This step involves:
- Nucleation: The initial formation of tiny islands of the deposited material on the substrate.
- Growth: These islands grow and coalesce to form a continuous film.
- The quality of the film depends on factors such as substrate temperature, deposition rate, and the energy of the condensing particles.
- The vaporized material condenses onto the substrate to form a thin film. This step involves:
-
Control and Monitoring:
- Quartz Crystal Rate Monitor: This device is used to measure and control the deposition rate and thickness of the film. It works by measuring the change in frequency of a quartz crystal as the film deposits on it, providing real-time feedback for precise control.
- Vacuum Levels: Maintaining a high vacuum is crucial to minimize contamination and ensure the desired film properties. The chamber is pumped down to very low pressures to reduce the presence of background gases.
-
Applications in Semiconductors:
- PVD is used in semiconductor manufacturing to deposit thin films of metals, metal alloys, and ceramics onto silicon wafers or other substrates. These films are essential for creating:
- Interconnects: Thin metal layers that connect different components of a semiconductor device.
- Barrier Layers: Layers that prevent diffusion between different materials.
- Protective Coatings: Layers that enhance the durability and performance of semiconductor devices.
- PVD is used in semiconductor manufacturing to deposit thin films of metals, metal alloys, and ceramics onto silicon wafers or other substrates. These films are essential for creating:
-
Advantages of PVD in Semiconductors:
- High Purity: The vacuum environment ensures minimal contamination, resulting in high-purity films.
- Precision: Advanced monitoring and control mechanisms allow for precise control over film thickness and composition.
- Durability: PVD coatings are highly resistant to wear, corrosion, and scratching, making them ideal for demanding semiconductor applications.
- Versatility: PVD can be used to deposit a wide range of materials, including metals, alloys, and ceramics.
-
Common PVD Techniques:
- Sputtering: The most widely used PVD technique in semiconductor manufacturing. It involves bombarding a target material with high-energy ions to dislodge atoms, which then deposit onto the substrate.
- Evaporation: Involves heating the target material until it vaporizes, with the vapor then condensing onto the substrate. This technique is often used for materials with lower melting points.
- Arc Deposition: Uses an electric arc to vaporize the target material, which is then deposited onto the substrate. This technique is known for producing dense, high-quality films.
By following these steps and utilizing advanced control mechanisms, the PVD process enables the production of high-quality thin films that are essential for the performance and reliability of semiconductor devices.
Summary Table:
Key Aspect | Details |
---|---|
Process Steps | Vaporization, Transportation, Condensation, Control & Monitoring |
Common Techniques | Sputtering, Evaporation, Arc Deposition |
Applications | Interconnects, Barrier Layers, Protective Coatings |
Advantages | High Purity, Precision, Durability, Versatility |
Monitoring Tools | Quartz Crystal Rate Monitor, High Vacuum Levels |
Discover how PVD can enhance your semiconductor manufacturing process—contact our experts today!