Vacuum deposition is a sophisticated process used to deposit thin films of material onto a substrate in a controlled, vacuum environment. This technique is widely used in industries such as semiconductors, optics, and aerospace for creating precise, high-quality coatings. The process involves creating a vacuum to eliminate interfering gases, preparing the substrate, evaporating or sputtering the coating material, depositing it onto the substrate, and finally cooling and venting the chamber. The result is a uniform, high-purity coating that can range from atomic thickness to several millimeters, depending on the application.
Key Points Explained:
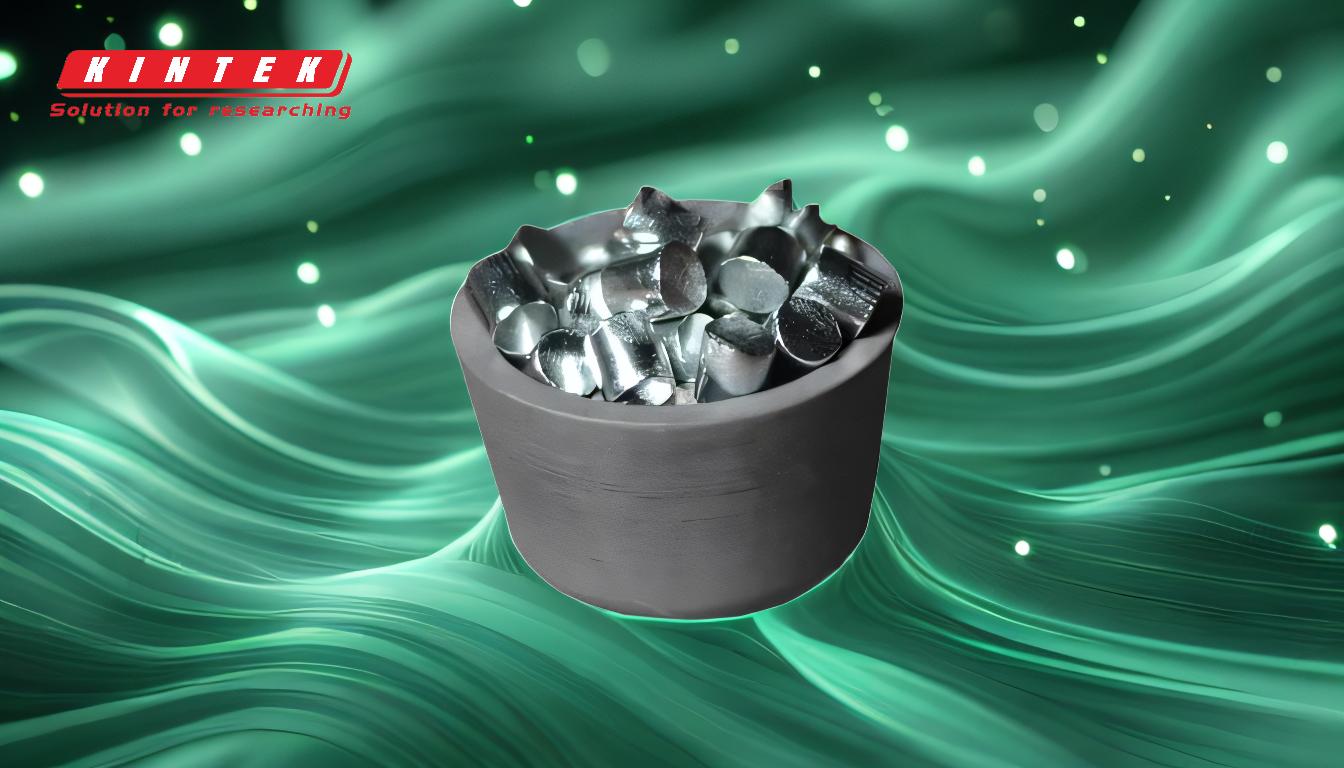
-
Creating a Vacuum Environment:
- The first step in vacuum deposition is creating a vacuum within the deposition chamber. This involves removing air and other gases to minimize contamination and interference during the deposition process. A vacuum environment ensures that the coating material can travel unimpeded to the substrate, resulting in a cleaner and more uniform deposition.
- The vacuum level required depends on the specific process and materials used. High vacuum levels (10^-6 to 10^-9 Torr) are typical for processes like physical vapor deposition (PVD) to ensure minimal gas molecule interference.
-
Substrate Preparation:
- Before deposition, the substrate (the surface to be coated) must be thoroughly cleaned and prepared. This often involves cleaning with solvents, plasma etching, or other surface treatments to remove contaminants and improve adhesion.
- Proper substrate preparation is critical for ensuring the coating adheres well and achieves the desired properties, such as uniformity and durability.
-
Evaporation or Sputtering of Coating Material:
- The coating material is introduced into the vacuum chamber and transformed into a vapor or plasma state. This can be achieved through:
- Evaporation: The material is heated until it vaporizes, typically using resistive heating, electron beams, or lasers.
- Sputtering: High-energy ions bombard a target material, knocking atoms off the target, which then deposit onto the substrate.
- These methods allow for precise control over the deposition rate and thickness of the coating.
- The coating material is introduced into the vacuum chamber and transformed into a vapor or plasma state. This can be achieved through:
-
Deposition of Material onto the Substrate:
- The vaporized or sputtered material travels through the vacuum and deposits onto the substrate. The lack of gas molecules in the vacuum ensures that the material forms a uniform, high-purity film.
- The deposition process can be controlled to achieve specific film properties, such as thickness, composition, and microstructure. This is particularly important for applications requiring nanometer-scale precision.
-
Cooling and Venting the Chamber:
- After the deposition is complete, the chamber is gradually cooled to room temperature to prevent thermal stress on the coated substrate. The chamber is then vented to atmospheric pressure, allowing the coated substrate to be removed.
- Proper cooling and venting are essential to maintain the integrity of the coating and ensure the substrate is not damaged.
-
Types of Vacuum Deposition Processes:
- Physical Vapor Deposition (PVD): Involves physical methods like evaporation or sputtering to deposit thin films. PVD is widely used for creating hard, wear-resistant coatings.
- Low-Pressure Chemical Vapor Deposition (LPCVD): Uses chemical reactions at low pressures to deposit thin films. This method is common in semiconductor manufacturing.
- Low-Pressure Plasma Spraying (LPPS): Combines plasma spraying with a vacuum environment to deposit high-quality coatings, often used in aerospace applications.
-
Applications of Vacuum Deposition:
- Vacuum deposition is used in a wide range of industries, including:
- Semiconductors: For creating thin films in integrated circuits and microelectronics.
- Optics: For producing anti-reflective, reflective, or protective coatings on lenses and mirrors.
- Aerospace: For applying thermal barrier coatings and corrosion-resistant layers on components.
- Decorative Coatings: For creating durable, aesthetically pleasing finishes on consumer products.
- Vacuum deposition is used in a wide range of industries, including:
-
Advantages of Vacuum Deposition:
- High Precision: Allows for the deposition of ultra-thin films with nanometer-scale accuracy.
- Clean Environment: The vacuum minimizes contamination, resulting in high-purity coatings.
- Versatility: Can deposit a wide range of materials, including metals, ceramics, and polymers.
- Enhanced Properties: Coatings can improve hardness, wear resistance, corrosion resistance, and other material properties.
By following these steps and understanding the key processes involved, vacuum deposition enables the creation of advanced materials and coatings with exceptional precision and performance.
Summary Table:
Key Step | Description |
---|---|
Creating a Vacuum Environment | Remove air and gases to minimize contamination and ensure uniform deposition. |
Substrate Preparation | Clean and treat the substrate for optimal adhesion and coating quality. |
Evaporation or Sputtering | Transform coating material into vapor or plasma using heat (evaporation) or ion bombardment (sputtering). |
Deposition onto Substrate | Deposit material uniformly onto the substrate in a vacuum environment. |
Cooling and Venting | Gradually cool and vent the chamber to prevent coating damage. |
Types of Processes | Includes PVD, LPCVD, and LPPS, each suited for specific applications. |
Applications | Used in semiconductors, optics, aerospace, and decorative coatings. |
Advantages | High precision, clean environment, versatility, and enhanced material properties. |
Discover how vacuum deposition can elevate your projects—contact our experts today!