The process temperature for PVD (Physical Vapor Deposition) coating typically ranges between 200°C to 450°C (approximately 392°F to 842°F), depending on the substrate material and specific application requirements. This lower temperature range is a key advantage of PVD over other coating methods like CVD (Chemical Vapor Deposition), which operates at much higher temperatures (600°C to 1100°C). The relatively low temperature of PVD makes it suitable for heat-sensitive materials, such as certain plastics and aluminum, which might otherwise deform or degrade at higher temperatures. Additionally, pre-treating heat-sensitive parts at 900°F to 950°F before coating can help minimize distortion or hardness alterations during the PVD process.
Key Points Explained:
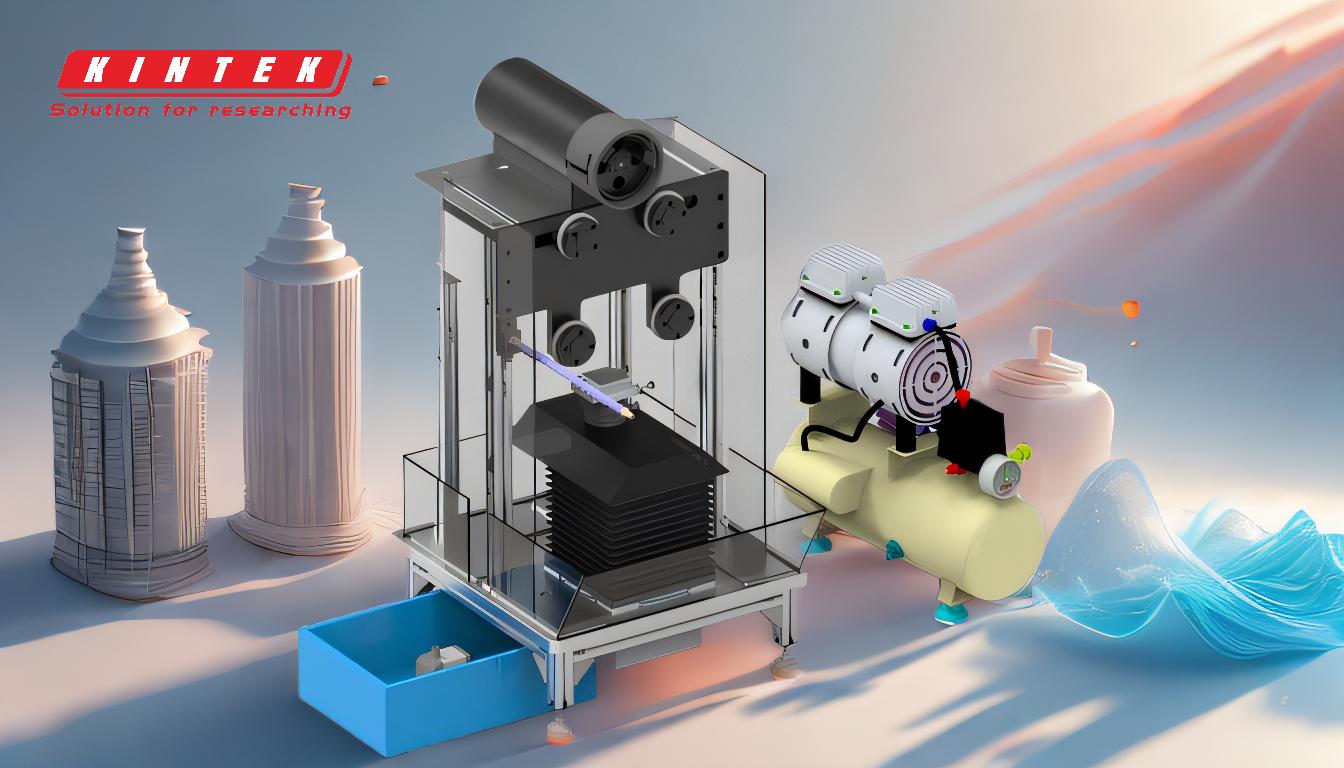
-
Typical PVD Coating Temperature Range:
- PVD coating is generally performed at temperatures between 200°C to 450°C (392°F to 842°F). This range is significantly lower than that of CVD, which operates at 600°C to 1100°C.
- The lower temperature is a result of the plasma-based process, which does not require high heat to vaporize the solid material.
-
Substrate-Specific Temperature Control:
- The exact temperature can vary depending on the substrate material. For example:
- Zinc, Brass, Steel: Can be coated at temperatures up to 400°F.
- Plastics: Require even lower temperatures, typically starting at 50°F, to prevent melting or deformation.
- Aluminum is generally unsuitable for PVD coating due to its low melting point, which is close to the upper limit of PVD temperatures.
- The exact temperature can vary depending on the substrate material. For example:
-
Pre-Treatment for Heat-Sensitive Parts:
- Heat-sensitive materials may undergo a pre-treatment process, such as tempering at 900°F to 950°F, to minimize distortions or changes in hardness during the coating process.
-
Advantages of Low-Temperature PVD:
- The lower temperatures make PVD suitable for a wide range of materials, including heat-sensitive substrates.
- It reduces the risk of thermal distortion, making it ideal for precision components and delicate materials.
-
Process Steps and Temperature Considerations:
- The PVD process involves several steps, including cleaning, pretreatment, vaporization, reaction, and deposition. Temperature control is critical during the vaporization and deposition phases to ensure proper adhesion and coating quality.
-
Comparison with CVD:
- PVD is preferred over CVD for applications requiring lower temperatures, as CVD’s high-temperature requirements can damage or alter the properties of certain substrates.
By maintaining precise temperature control and tailoring the process to the substrate material, PVD coating achieves high-quality, durable finishes without compromising the integrity of the underlying material.
Summary Table:
Aspect | Details |
---|---|
Typical Temperature Range | 200°C to 450°C (392°F to 842°F) |
Substrate-Specific Control | - Zinc, Brass, Steel: Up to 400°F - Plastics: Starting at 50°F |
Pre-Treatment | Heat-sensitive parts tempered at 900°F to 950°F to minimize distortion |
Advantages | Suitable for heat-sensitive materials, reduces thermal distortion |
Comparison with CVD | PVD operates at lower temperatures, making it ideal for delicate materials |
Discover how PVD coating can enhance your material performance—contact our experts today!