An induction furnace is a highly efficient and environmentally friendly melting device used primarily in foundries and industrial settings. Its primary purpose is to melt metals such as iron, steel, copper, aluminum, and precious metals with minimal contamination, precise temperature control, and energy efficiency. Unlike traditional furnaces, induction furnaces generate heat directly within the metal charge using electromagnetic induction, eliminating the need for combustion or an arc. This results in a cleaner melting process, reduced oxidation, and the preservation of alloying elements. Induction furnaces are also praised for their fast heating speed, low energy consumption, and ability to create a homogeneous mixture of molten metals, making them ideal for applications like alloy manufacturing, investment casting, and other metalworking processes.
Key Points Explained:
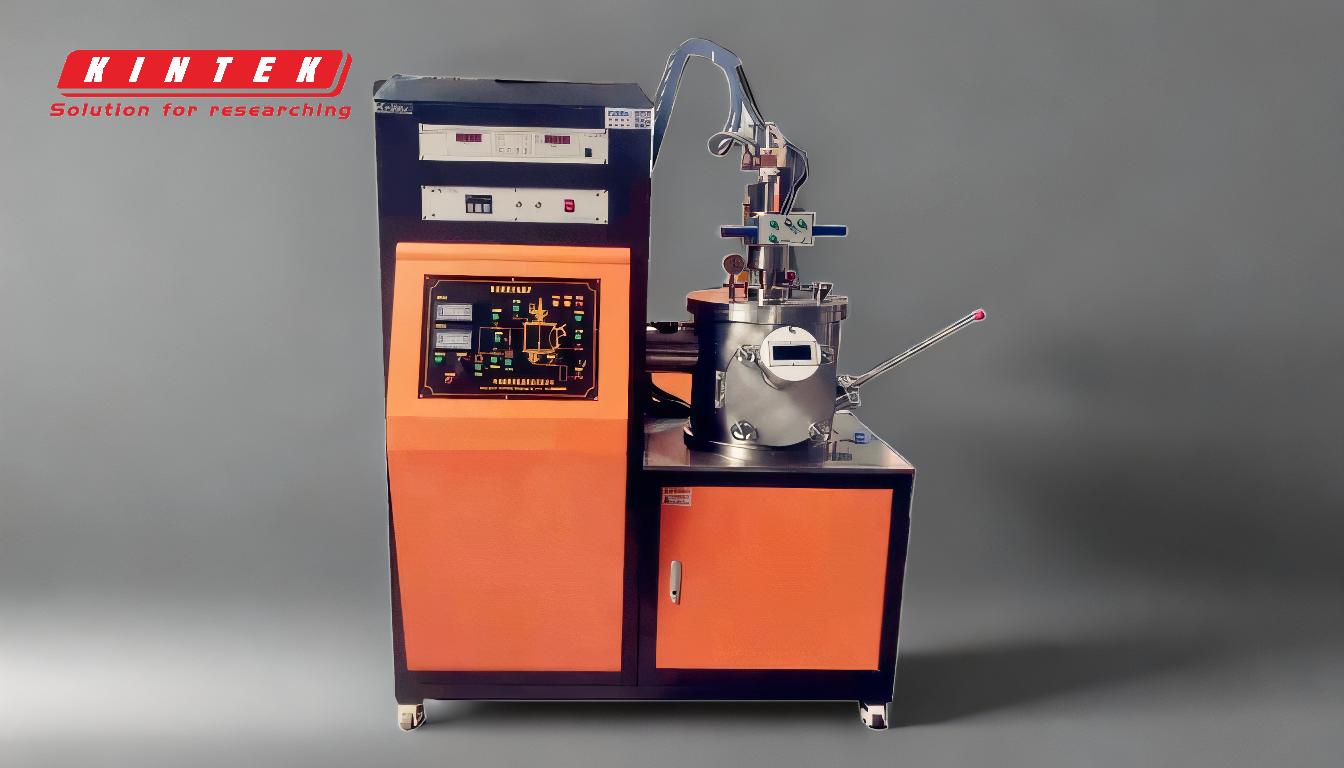
-
Purpose of Melting Metals:
- Induction furnaces are primarily used to melt metals, including iron, steel, copper, aluminum, and precious metals.
- The melted metal is poured into molds to produce castings, which are used in various industrial applications.
-
Clean and Contamination-Free Melting:
- Induction furnaces do not rely on combustion or an arc, which prevents contamination from external heat sources.
- The heat is generated directly within the metal charge through electromagnetic induction, ensuring a cleaner melting process.
-
Preservation of Alloying Elements:
- The regulated temperature control in induction furnaces allows metals to retain their alloying elements, which is crucial for maintaining the desired properties of the final product.
- This makes induction furnaces ideal for melting valuable alloys without compromising their composition.
-
Energy Efficiency and Low Pollution:
- Induction furnaces are highly energy-efficient, consuming less power compared to traditional furnaces.
- They produce minimal waste and pollutants, such as dust, making them environmentally friendly and reducing the carbon footprint of industrial operations.
-
Fast Heating and High Production Efficiency:
- Induction furnaces heat metals rapidly, leading to shorter melting cycles and higher production efficiency.
- This speed is beneficial for industries requiring high throughput and quick turnaround times.
-
Superior Temperature Control:
- The precise temperature control in induction furnaces ensures consistent melting conditions, reducing the risk of overheating or underheating.
- This accuracy is particularly important for processes like investment casting, annealing, and brazing.
-
Homogeneous Mixing of Molten Metals:
- The electromagnetic stirring action in induction furnaces creates a uniform mixture of molten metals, eliminating the need for manual sampling or stirring.
- This homogeneity ensures the quality and consistency of the final product.
-
Versatility in Applications:
- Induction furnaces are used in various industrial processes, including alloy manufacturing, aluminum melting, investment casting, shrink-fitting, annealing, and brazing.
- Their flexibility and efficiency make them suitable for a wide range of metalworking applications.
-
Improved Working Conditions:
- Induction furnaces operate in a contained and clean environment, reducing exposure to pollutants and improving safety for workers.
- The absence of combustion or open flames makes the process safer and more controlled.
-
Replacement of Older Furnaces:
- Many older foundries are replacing traditional cupolas with induction furnaces due to their superior efficiency, cleanliness, and environmental benefits.
- This transition reflects the growing preference for modern, sustainable melting technologies.
In summary, the induction furnace serves as a critical tool in modern metalworking and foundry operations. Its ability to melt metals cleanly, efficiently, and precisely makes it indispensable for producing high-quality castings and alloys while minimizing environmental impact and operational costs.
Summary Table:
Feature | Description |
---|---|
Purpose | Melts metals (iron, steel, copper, aluminum, precious metals) for industrial use. |
Clean Melting | No combustion or arc; heat generated via electromagnetic induction. |
Energy Efficiency | Low power consumption and minimal waste production. |
Temperature Control | Precise regulation for consistent melting conditions. |
Fast Heating | Rapid melting cycles for high production efficiency. |
Homogeneous Mixing | Electromagnetic stirring ensures uniform molten metal quality. |
Applications | Alloy manufacturing, investment casting, annealing, brazing, and more. |
Environmental Benefits | Reduces pollution and carbon footprint compared to traditional furnaces. |
Upgrade your metal melting process with an induction furnace—contact us today to learn more!