A vulcanizing machine, also known as a vulcanizer, is primarily used to vulcanize rubber and plastic products. Vulcanization is a chemical process that improves the elasticity, strength, and durability of rubber by cross-linking polymer chains. The machine achieves this by providing precise control over pressure, temperature, and timing, ensuring consistent and high-quality results. Key functions include automatic mold clamping, pressure supplementation, temperature control, and timing, with alarms to notify operators when the process is complete. This makes the vulcanizing machine essential in industries like automotive, manufacturing, and construction, where durable rubber components are required.
Key Points Explained:
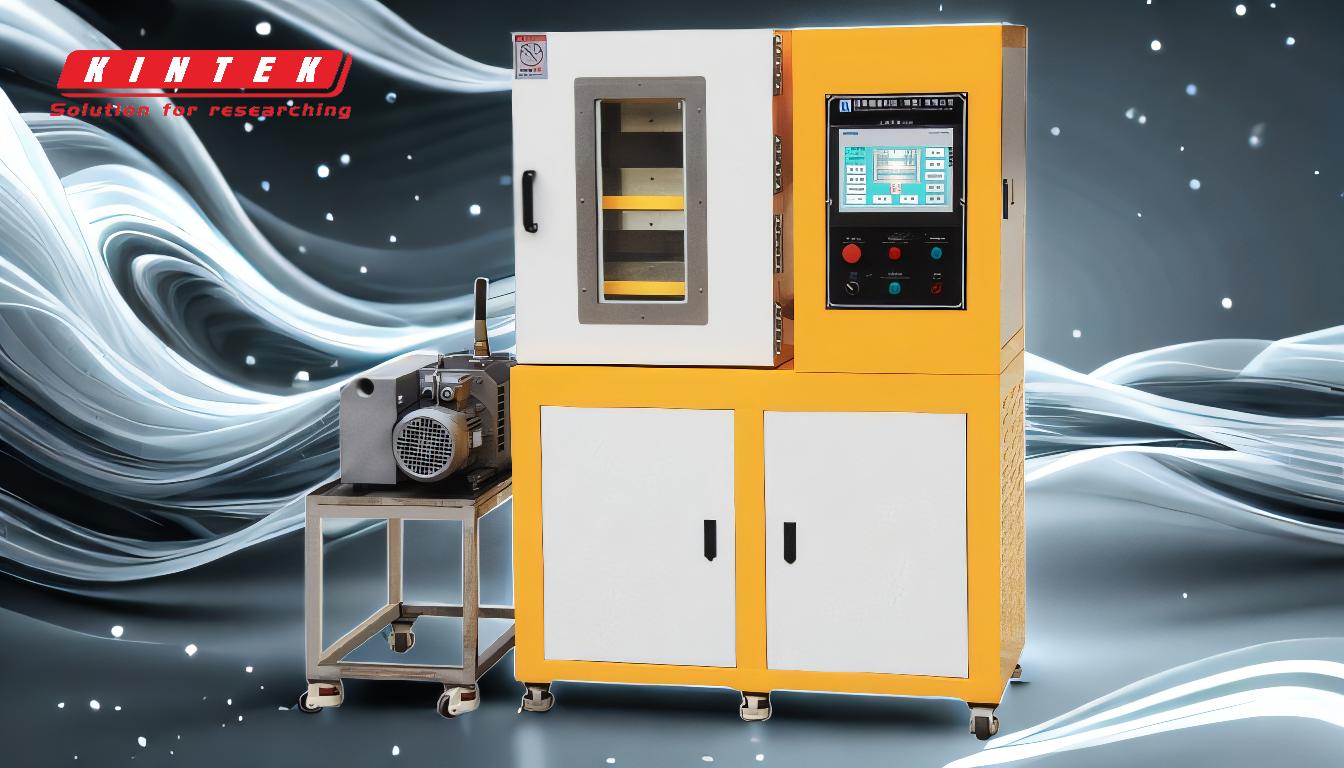
-
Purpose of Vulcanization:
- Vulcanization is a chemical process that enhances the properties of rubber, making it more elastic, durable, and resistant to wear, heat, and chemicals.
- The vulcanizing machine facilitates this process by creating the ideal conditions for the reaction to occur.
-
Core Functions of a Vulcanizing Machine:
-
Pressure Application:
- The machine uses a hydraulic system to generate and maintain the necessary pressure for vulcanization. This ensures that the rubber or plastic material is evenly compressed, which is critical for achieving uniform properties.
-
Temperature Control:
- A heating medium, such as steam or electric heaters, provides the required temperature for the vulcanization process. Precise temperature control ensures the chemical reaction occurs efficiently without damaging the material.
-
Timing and Automation:
- The machine includes automatic timing features to control the duration of the vulcanization process. This ensures consistency across batches and reduces the risk of human error.
- Alarms notify operators when the process is complete, improving workflow efficiency.
-
Pressure Application:
-
Applications in Industry:
- Vulcanizing machines are widely used in industries that rely on rubber components, such as:
- Automotive: For manufacturing tires, seals, and gaskets.
- Construction: For producing rubber mats, hoses, and insulation materials.
- Consumer Goods: For creating items like footwear, gloves, and sports equipment.
- Vulcanizing machines are widely used in industries that rely on rubber components, such as:
-
Advantages of Using a Vulcanizing Machine:
- Consistency: Automated pressure and temperature control ensure uniform quality across products.
- Efficiency: Timers and alarms streamline the production process, reducing downtime.
- Versatility: The machine can handle a wide range of rubber and plastic products, making it a valuable tool in various industries.
-
Key Components of a Vulcanizing Machine:
- Hydraulic System: Generates the pressure needed for mold clamping and vulcanization.
- Heating System: Provides the heat required for the chemical reaction.
- Control Panel: Allows operators to set and monitor pressure, temperature, and timing.
- Mold Clamping Mechanism: Ensures the material is securely held in place during the process.
By combining these functions, a vulcanizing machine ensures the production of high-quality rubber products that meet industry standards and customer requirements.
Summary Table:
Key Feature | Description |
---|---|
Pressure Application | Hydraulic system ensures even compression for uniform vulcanization. |
Temperature Control | Steam or electric heaters provide precise heat for efficient chemical reactions. |
Timing & Automation | Automatic timers and alarms ensure consistency and reduce human error. |
Applications | Automotive, construction, and consumer goods industries. |
Advantages | Consistent quality, improved efficiency, and versatile use. |
Key Components | Hydraulic system, heating system, control panel, and mold clamping mechanism. |
Upgrade your production process with a vulcanizing machine—contact us today for expert advice!