The PVD (Physical Vapor Deposition) sputtering process is a widely used technique for depositing thin films of material onto a substrate. It involves bombarding a target material with high-energy ions, typically argon gas ions, to eject atoms or molecules from the target. These ejected particles then travel through a vacuum chamber and condense onto a substrate, forming a thin film. The process is highly controllable and versatile, making it suitable for applications in semiconductors, optics, and coatings. Below, the key aspects of the PVD sputtering process are explained in detail.
Key Points Explained:
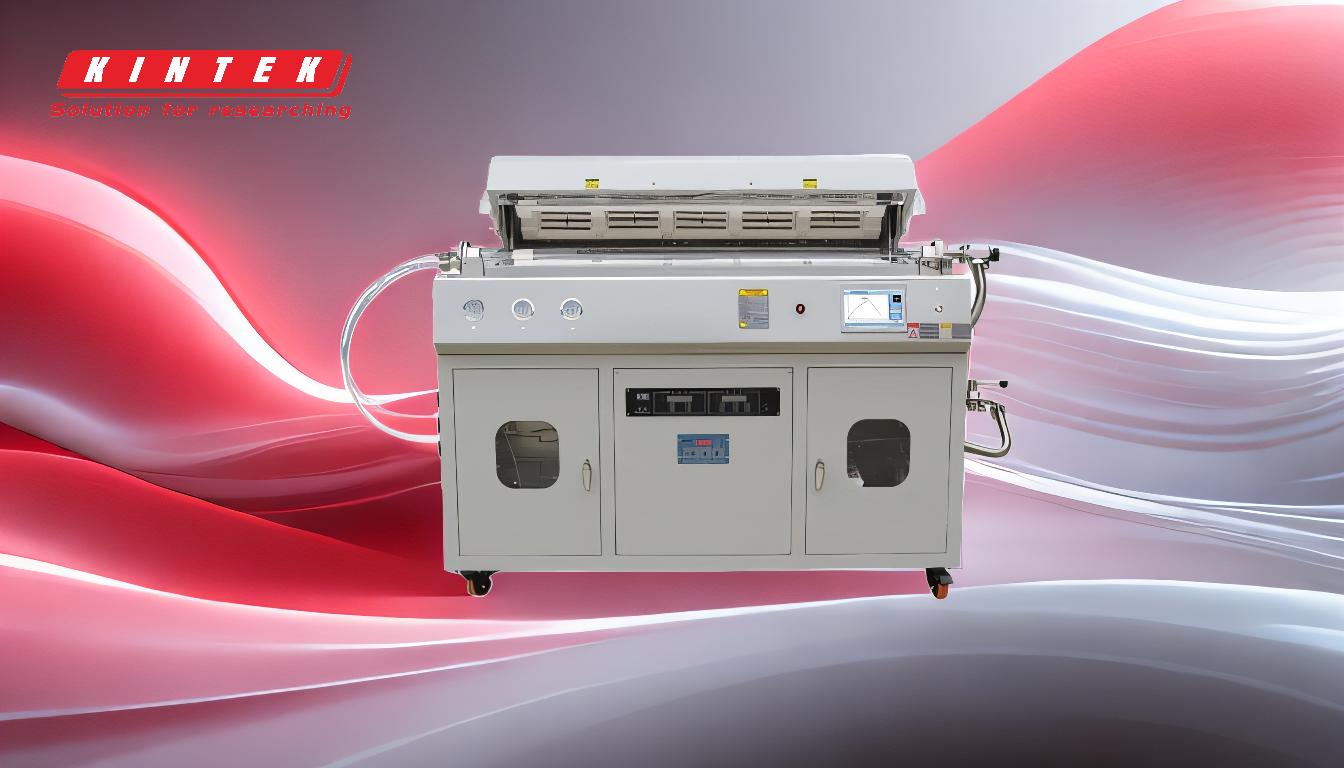
-
Definition and Overview of PVD Sputtering:
- PVD sputtering is a physical vapor deposition technique where atoms or molecules are ejected from a target material by high-energy particle bombardment.
- The ejected particles condense on a substrate to form a thin film.
- This process is widely used in industries requiring precise thin-film deposition, such as electronics, optics, and wear-resistant coatings.
-
Key Components of the Sputtering Process:
- Target Material: The material to be deposited as a thin film. It serves as the cathode in the sputtering system.
- Substrate: The surface onto which the thin film is deposited. It acts as the anode.
- Inert Gas (Argon): Typically used to generate ions for bombarding the target.
- Vacuum Chamber: Provides a controlled environment to minimize contamination and ensure efficient deposition.
-
Mechanism of Sputtering:
- Ion Generation: Inert gas atoms (e.g., argon) are ionized to form a plasma.
- Bombardment: High-energy ions from the plasma are accelerated toward the target material.
- Ejection of Target Atoms: The impact of ions transfers energy to the target, causing atoms or molecules to be ejected (sputtered) from the surface.
- Transport and Deposition: The ejected neutral particles travel through the vacuum chamber and condense on the substrate, forming a thin film.
-
Types of Sputtering Techniques:
- DC Sputtering: Uses a direct current (DC) power supply to generate ions. Suitable for conductive target materials.
- RF Sputtering: Uses radio frequency (RF) power to generate ions. Suitable for insulating target materials.
- Magnetron Sputtering: Employs magnetic fields to enhance ionization efficiency and deposition rates.
- Reactive Sputtering: Introduces reactive gases (e.g., oxygen or nitrogen) to form compound films (e.g., oxides or nitrides).
-
Advantages of PVD Sputtering:
- High-Quality Films: Produces dense, uniform, and well-adhered thin films.
- Versatility: Can deposit a wide range of materials, including metals, alloys, and ceramics.
- Controllability: Precise control over film thickness, composition, and properties.
- Scalability: Suitable for both small-scale research and large-scale industrial applications.
-
Applications of PVD Sputtering:
- Semiconductors: Deposition of conductive and insulating layers in microelectronics.
- Optics: Coating of lenses, mirrors, and displays for enhanced optical properties.
- Wear-Resistant Coatings: Application of hard coatings (e.g., titanium nitride) on tools and components.
- Decorative Coatings: Deposition of aesthetically pleasing and durable coatings on consumer products.
-
Challenges and Considerations:
- Target Erosion: Continuous bombardment can lead to target wear, requiring periodic replacement.
- Contamination: Impurities in the vacuum chamber or target material can affect film quality.
- Cost: High initial investment in equipment and maintenance.
- Process Optimization: Requires careful tuning of parameters (e.g., pressure, power, and gas flow) for optimal results.
By understanding these key aspects, one can appreciate the complexity and versatility of the PVD sputtering process, making it a cornerstone of modern thin-film technology.
Summary Table:
Aspect | Details |
---|---|
Definition | A technique to deposit thin films by ejecting atoms from a target material. |
Key Components | Target material, substrate, inert gas (argon), and vacuum chamber. |
Mechanism | Ion generation, bombardment, ejection, and deposition of target atoms. |
Techniques | DC, RF, magnetron, and reactive sputtering. |
Advantages | High-quality films, versatility, controllability, and scalability. |
Applications | Semiconductors, optics, wear-resistant coatings, and decorative coatings. |
Challenges | Target erosion, contamination, cost, and process optimization. |
Discover how the PVD sputtering process can enhance your projects—contact our experts today!