The pyrolysis process for scrap tires involves heating the tires in an oxygen-free environment to break them down into smaller molecules, which are then converted into useful products such as pyrolysis oil, syngas, and carbon black. This thermochemical process begins with the preparation of tires, which are shredded or halved before being fed into a reactor. Inside the reactor, the rubber softens and disintegrates due to high temperatures, producing vapors that can be condensed into oil or used as fuel. Solid residues, such as steel wires and carbon black, are also recovered. The process is energy-intensive but offers a sustainable way to recycle tires and reduce waste.
Key Points Explained:
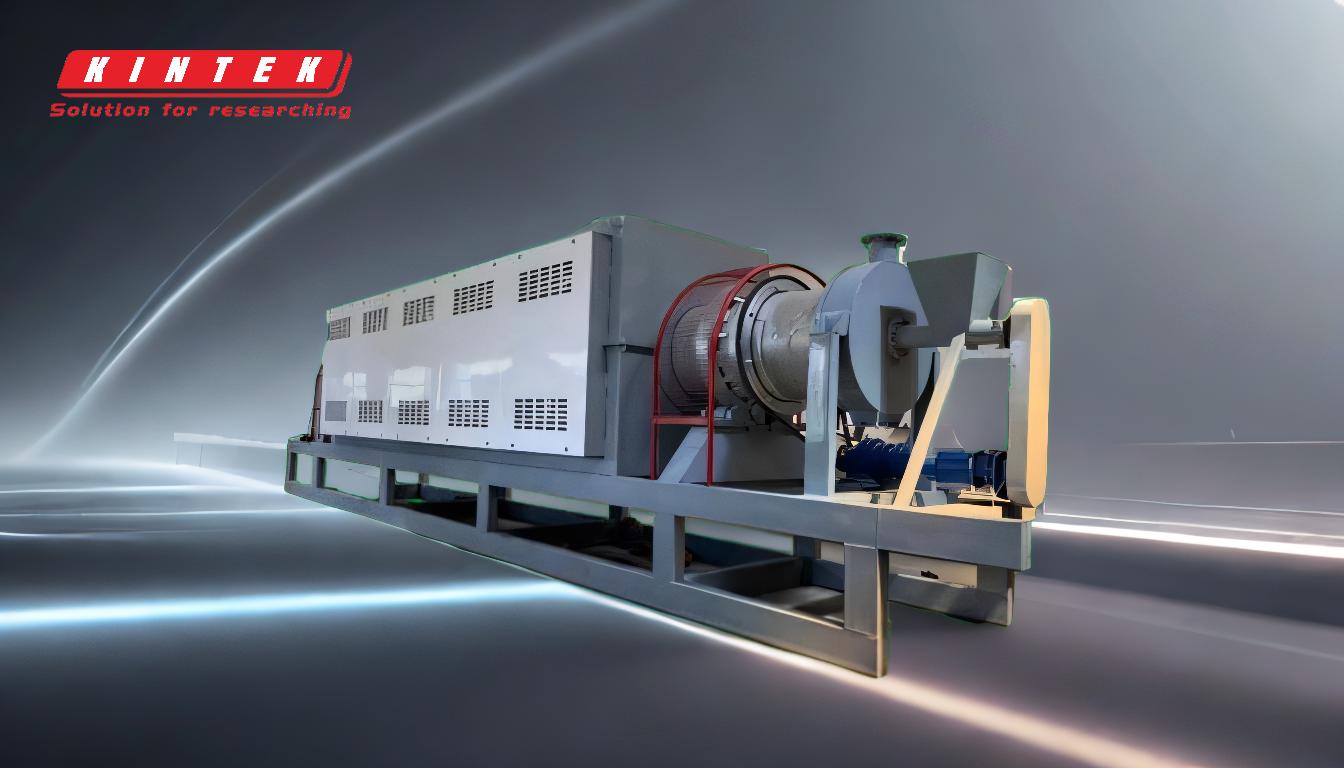
-
Definition of Pyrolysis:
- Pyrolysis is a thermochemical decomposition process that occurs in the absence of oxygen. Derived from the Greek words "pyro" (fire) and "lysis" (separation), it involves breaking down materials like tires, plastics, or biomass into smaller molecules through heat. This process is particularly effective for recycling scrap tires, as it converts them into valuable byproducts.
-
Preparation of Scrap Tires:
- Before pyrolysis, scrap tires undergo preparation steps:
- Shredding or Halving: Tires are cut into smaller pieces to facilitate uniform heating and efficient decomposition.
- Magnetic Separation: Steel wires and other metallic components are removed using magnets, as they do not decompose during pyrolysis and can be recycled separately.
- Before pyrolysis, scrap tires undergo preparation steps:
-
Pyrolysis Reactor Operation:
- The prepared tire pieces are fed into a pyrolysis reactor, which operates in an oxygen-free environment to prevent combustion. Key steps include:
- Heating: The reactor is heated to temperatures typically ranging from 400°C to 700°C, causing the rubber to soften and disintegrate.
- Vaporization: The rubber breaks down into smaller hydrocarbon molecules, which vaporize and exit the reactor as gases.
- Cracking: The vaporized gases undergo further thermal cracking, breaking down into lighter hydrocarbons.
- The prepared tire pieces are fed into a pyrolysis reactor, which operates in an oxygen-free environment to prevent combustion. Key steps include:
-
Product Recovery:
- The vapors produced during pyrolysis are processed to recover valuable products:
- Pyrolysis Oil: The vapors are condensed into a liquid known as pyrolysis oil, which can be used as fuel or further refined.
- Syngas: Non-condensable gases, such as methane and hydrogen, are collected and used as fuel to power the pyrolysis process or for other energy needs.
- Carbon Black: The solid residue left in the reactor is carbon black, a valuable material used in manufacturing tires, inks, and coatings.
- Steel Wires: Recovered during the preparation stage, steel wires are recycled for use in construction or other industries.
- The vapors produced during pyrolysis are processed to recover valuable products:
-
Energy Requirements and Sustainability:
- Pyrolysis is an energy-intensive process, requiring significant heat input to achieve the necessary temperatures. However, the syngas produced during pyrolysis can be used to offset energy costs, making the process more sustainable. Additionally, pyrolysis reduces landfill waste and provides a circular economy solution for scrap tires.
-
Applications of Pyrolysis Products:
- The products derived from tire pyrolysis have diverse applications:
- Pyrolysis Oil: Used as a substitute for industrial fuel oil or as a feedstock for refining into diesel or gasoline.
- Syngas: Used for heating, electricity generation, or as a chemical feedstock.
- Carbon Black: Used in rubber products, plastics, and as a pigment in inks and paints.
- Steel Wires: Recycled for use in construction, automotive, and manufacturing industries.
- The products derived from tire pyrolysis have diverse applications:
-
Advantages of Tire Pyrolysis:
- Waste Reduction: Converts non-biodegradable tires into useful products, reducing landfill waste.
- Resource Recovery: Recovers valuable materials like oil, gas, and carbon black, contributing to a circular economy.
- Environmental Benefits: Reduces the environmental impact of tire disposal and provides an alternative to fossil fuels.
-
Challenges and Considerations:
- Energy Consumption: The process requires significant energy input, though this can be partially offset by using the syngas produced.
- Emission Control: Proper management of emissions and byproducts is essential to minimize environmental impact.
- Economic Viability: The profitability of tire pyrolysis depends on the market value of the recovered products and the scale of operation.
By understanding the pyrolysis process for scrap tires, purchasers and stakeholders can evaluate its feasibility, sustainability, and economic benefits for waste management and resource recovery.
Summary Table:
Aspect | Details |
---|---|
Process | Heating tires in an oxygen-free environment to break them into smaller molecules. |
Key Products | Pyrolysis oil, syngas, carbon black, and steel wires. |
Temperature Range | 400°C to 700°C. |
Applications | Fuel production, energy generation, rubber manufacturing, and construction. |
Advantages | Waste reduction, resource recovery, and environmental benefits. |
Challenges | High energy consumption, emission control, and economic viability. |
Discover how pyrolysis can transform your waste management strategy—contact us today for expert guidance!