The substrate plays a critical role in Chemical Vapor Deposition (CVD) by influencing the quality, uniformity, and adhesion of the deposited film. Its material, surface preparation, and temperature during deposition directly impact the sticking coefficient, which determines how effectively the precursor molecules adhere to the surface. Proper substrate selection and preparation ensure compatibility with the precursor and optimal deposition conditions, leading to efficient and uniform film growth. Additionally, the substrate holder and manipulator system are essential for maintaining consistent deposition conditions, such as distance and rotation, to achieve a high-quality film.
Key Points Explained:
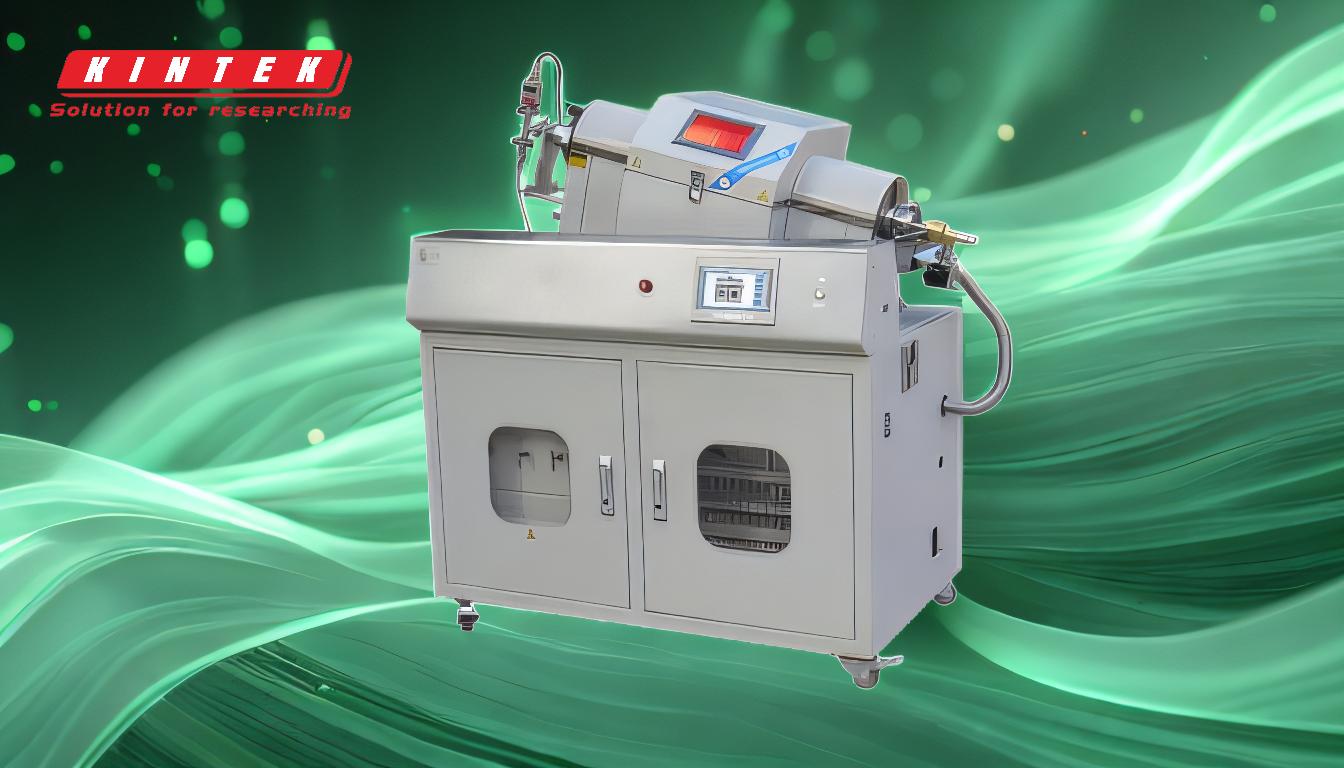
-
Role of Substrate in CVD:
- The substrate acts as the foundation for film deposition in CVD. Its material properties, such as thermal conductivity, surface energy, and chemical compatibility, influence the nucleation and growth of the deposited film.
- The substrate's surface preparation, including cleaning and treatment, ensures a defect-free and uniform surface, which is critical for high-quality film deposition.
-
Impact of Substrate Temperature:
- The temperature of the substrate during deposition affects the sticking coefficient, which is the probability of precursor molecules adhering to the surface. Higher temperatures can enhance surface mobility, leading to better film quality and uniformity.
- Optimal substrate temperature is determined by the precursor's decomposition kinetics and the desired film properties, such as crystallinity and adhesion.
-
Substrate Compatibility with Precursors:
- The substrate must be chemically compatible with the precursor gases to avoid unwanted reactions or contamination. For example, certain substrates may react with specific precursors, leading to poor film quality or delamination.
- Knowledge of substrate-precursor interactions is essential for selecting the right materials and achieving efficient deposition.
-
Substrate Holder and Manipulator System:
- The substrate holder securely fastens the substrate and ensures it remains stable during deposition. It is often attached to a manipulator shaft, which allows precise control over the substrate's position and rotation.
- Rotating the substrate during deposition ensures uniform exposure to the precursor gases, leading to consistent film thickness and quality across the entire surface.
-
Surface Preparation and Cleaning:
- Before deposition, the substrate undergoes ultrasonic cleaning to remove contaminants and ensure a pristine surface. This step is crucial for achieving strong adhesion and minimizing defects in the deposited film.
- Proper surface preparation also includes treatments such as etching or coating to enhance nucleation sites and improve film growth.
-
Influence on Process Selection (PVD vs. CVD):
- The substrate's properties and requirements can influence the choice between Physical Vapor Deposition (PVD) and CVD. For example, CVD is often preferred for substrates that require conformal coatings or complex geometries, while PVD may be better suited for temperature-sensitive materials.
- Understanding the substrate's role helps in selecting the most suitable deposition technique for specific applications.
By carefully considering the substrate's material, temperature, and preparation, along with the use of appropriate equipment like substrate holders and manipulators, CVD processes can achieve high-quality, uniform, and adherent films tailored to specific applications.
Summary Table:
Key Aspect | Role in CVD |
---|---|
Substrate Material | Influences nucleation, growth, and adhesion of the deposited film. |
Substrate Temperature | Affects sticking coefficient and surface mobility for better film quality. |
Substrate Compatibility | Ensures chemical compatibility with precursor gases to avoid contamination. |
Substrate Holder System | Maintains stability and rotation for uniform film thickness and quality. |
Surface Preparation | Ensures defect-free surfaces through cleaning and treatment for strong adhesion. |
Optimize your CVD process with the right substrate—contact our experts today for tailored solutions!