The furnace atmosphere plays a crucial role in material processing by either protecting the material from unwanted surface reactions or enabling specific surface modifications. It can be chemically inert to prevent oxidation or other undesirable reactions, or chemically reactive to facilitate processes like carburizing. The choice of atmosphere depends on the material being processed and the desired outcome. For instance, in a muffle furnace, the atmosphere ensures that the sample is heated without direct contact with flames, allowing for precise control over the material's properties.
Key Points Explained:
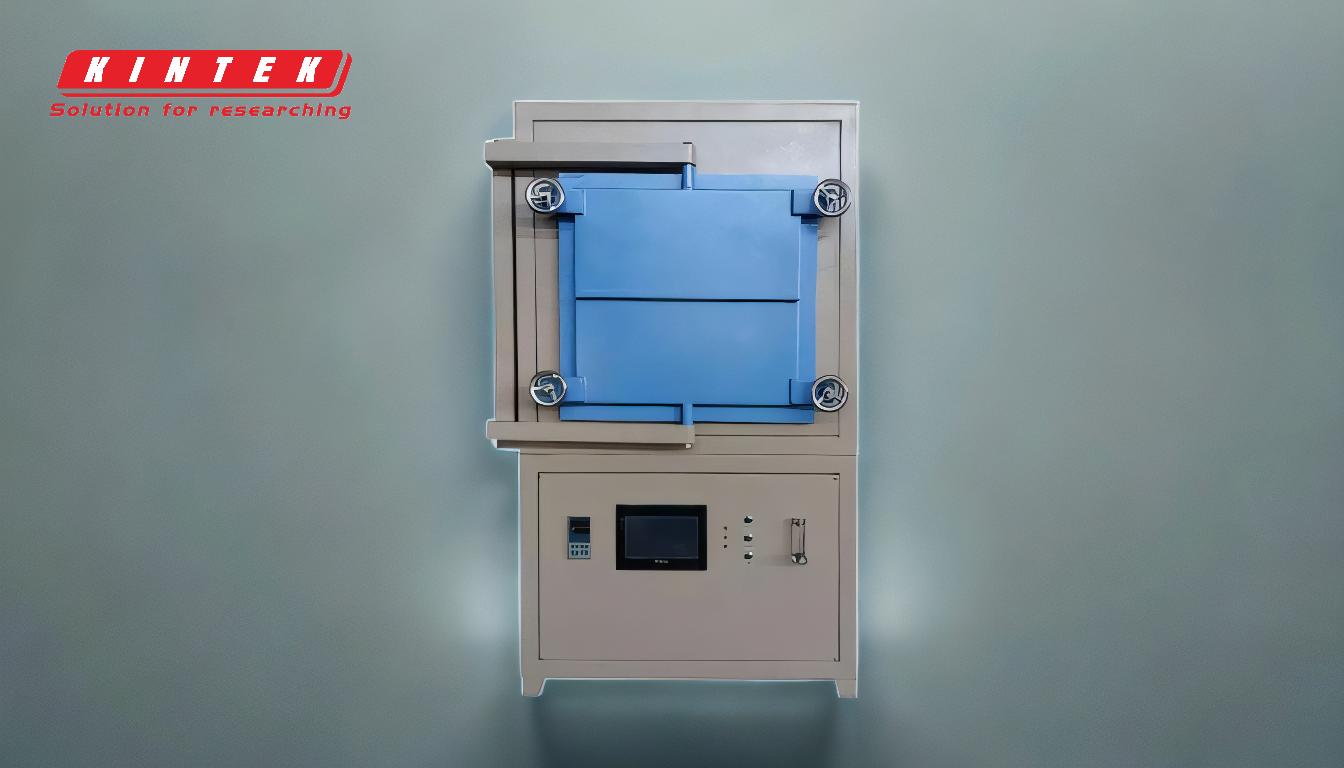
-
Protection from Surface Reactions:
- The furnace atmosphere acts as a protective barrier, preventing materials from undergoing unwanted chemical reactions such as oxidation or contamination. This is particularly important in processes where the material's surface integrity is critical, such as in metal heat treatment or ceramic sintering.
-
Chemically Inert Atmosphere:
- An inert atmosphere, typically composed of gases like nitrogen or argon, is used when the goal is to shield the material from reactive elements in the environment. This is common in processes like annealing, where maintaining the material's purity and preventing oxidation are essential.
-
Chemically Reactive Atmosphere:
- In some cases, a reactive atmosphere is intentionally introduced to facilitate specific surface reactions. For example, carburizing involves introducing a carbon-rich atmosphere to increase the surface hardness of steel. This controlled reactivity is vital for achieving desired material properties.
-
Role in a Muffle Furnace:
- In a muffle furnace, the atmosphere ensures that the sample is heated uniformly and without direct exposure to flames. This allows for precise control over the heating process, making it ideal for applications like ash content determination or material property evaluation.
-
Process-Specific Atmospheres:
- The choice of furnace atmosphere is highly dependent on the specific process and material being treated. For instance, in sintering processes, reducing atmospheres are often used to prevent oxidation of metal powders, while in brazing, a vacuum or inert gas atmosphere may be employed to ensure strong, clean joints.
-
Impact on Material Properties:
- The furnace atmosphere directly influences the final properties of the material, such as hardness, strength, and surface finish. By carefully selecting the appropriate atmosphere, manufacturers can tailor the material's characteristics to meet specific application requirements.
-
Temperature and Atmosphere Interaction:
- The effectiveness of the furnace atmosphere is closely tied to the temperature at which the material is processed. Higher temperatures can accelerate both desirable and undesirable reactions, making the choice of atmosphere even more critical in high-temperature applications.
By understanding and controlling the furnace atmosphere, manufacturers can achieve precise and consistent results in material processing, ensuring that the final product meets the required specifications.
Summary Table:
Aspect | Role of Furnace Atmosphere |
---|---|
Protection | Prevents oxidation and contamination, ensuring surface integrity. |
Inert Atmosphere | Uses gases like nitrogen or argon to shield materials from reactive elements. |
Reactive Atmosphere | Facilitates processes like carburizing to enhance material properties. |
Muffle Furnace Role | Ensures uniform heating without direct flame contact for precise control. |
Process-Specific Atmospheres | Tailored to processes like sintering or brazing for optimal results. |
Material Properties | Influences hardness, strength, and surface finish based on atmosphere choice. |
Temperature Interaction | Higher temperatures require careful atmosphere selection to control reactions. |
Discover how the right furnace atmosphere can transform your material processing—contact our experts today!