Sintering pressing force refers to the external pressure applied during the sintering process to enhance the densification and mechanical properties of the material. This force, combined with the intrinsic sintering stress driven by curvature, accelerates particle rearrangement, reduces porosity, and improves the overall density and strength of the final product. The magnitude of the pressing force, along with factors like temperature, particle size, and composition, plays a critical role in determining the efficiency and quality of the sintering process. High-pressure pressing brings powder particles into closer contact, allowing them to deform and sinter more effectively, resulting in a denser and stronger material.
Key Points Explained:
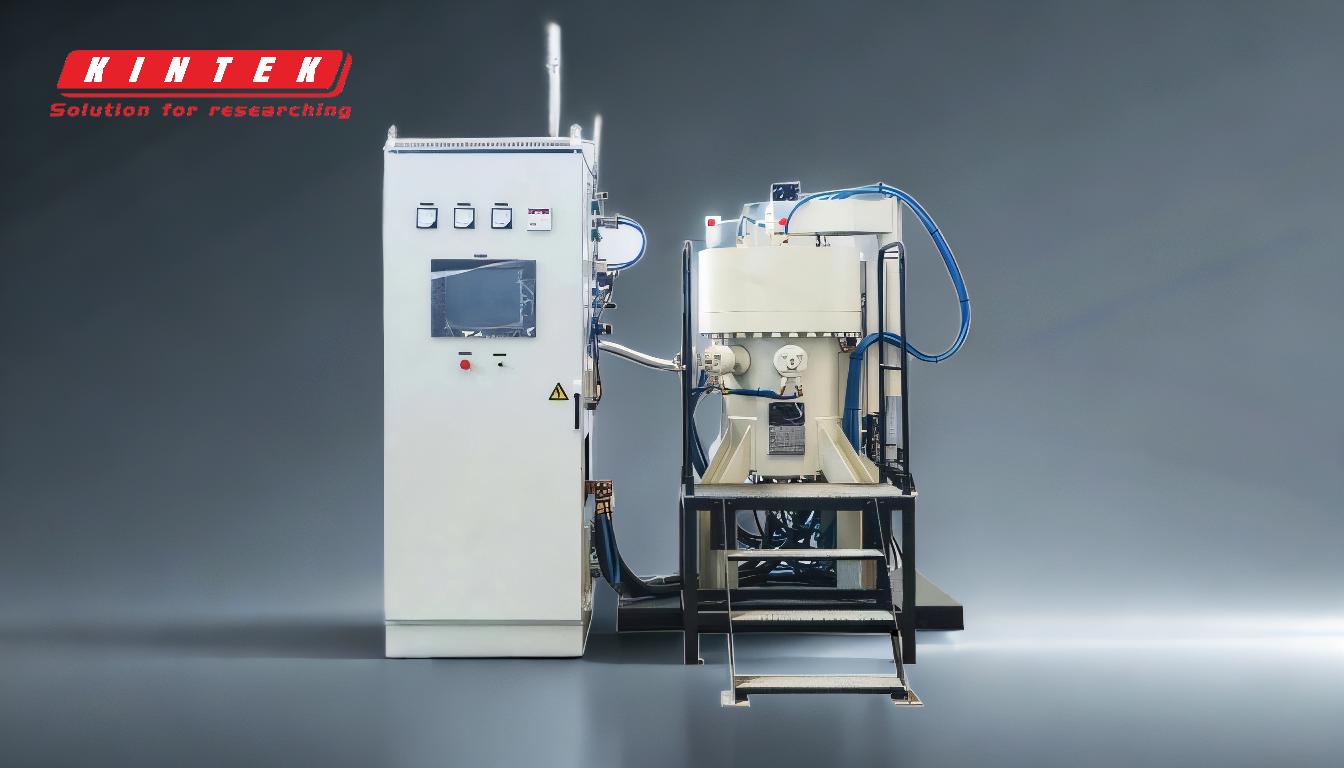
-
Definition of Sintering Pressing Force:
- Sintering pressing force is the external pressure applied during the sintering process to aid in the densification of powder particles. This force works in conjunction with the intrinsic sintering stress, which is driven by the curvature of the particles, to enhance the overall sintering driving force.
-
Role of Pressing Force in Sintering:
- Particle Rearrangement: Applying pressure helps rearrange particles into a more compact structure, reducing voids and porosity.
- Enhanced Densification: High-pressure pressing brings particles into closer contact, allowing them to deform and merge more effectively during heating, leading to a denser final product.
- Reduced Sintering Time: The application of pressure can significantly decrease the time required for sintering by accelerating particle bonding and densification.
-
Factors Influencing Sintering Pressing Force:
- Temperature: Higher temperatures increase the mobility of atoms, making it easier for particles to deform and merge under pressure.
- Particle Size: Smaller particles have a higher surface area-to-volume ratio, which enhances their ability to sinter under pressure.
- Composition: Homogeneous compositions and the presence of coupling agents can improve the effectiveness of the pressing force by promoting better particle bonding.
-
Impact on Material Properties:
- Mechanical Strength: High-pressure sintering results in materials with higher tensile strength, bending fatigue strength, and impact energy due to reduced porosity and improved particle bonding.
- Density: The application of pressure during sintering leads to a denser material with fewer voids, enhancing its overall structural integrity.
-
Process Variables and Control:
- Atmosphere: The sintering atmosphere (air, vacuum, or inert gases like argon/nitrogen) can influence the effectiveness of the pressing force by affecting oxidation and particle interactions.
- Heating Rate: A controlled heating rate ensures uniform densification and prevents defects that could arise from rapid temperature changes.
- Layer Thickness and Speed: In industrial sintering, layer thickness and machine speed are controlled to ensure that the material is sintered uniformly and reaches the desired endpoint.
-
Applications and Benefits:
- Industrial Manufacturing: Sintering pressing force is widely used in the production of metal components, ceramics, and composites, where high density and mechanical strength are required.
- Material Optimization: By controlling the pressing force and other sintering parameters, manufacturers can tailor the properties of the final product to meet specific application requirements.
In summary, sintering pressing force is a critical parameter in the sintering process that enhances densification, reduces porosity, and improves the mechanical properties of the final material. By understanding and optimizing the factors that influence this force, manufacturers can produce high-quality sintered products with superior performance characteristics.
Summary Table:
Key Aspect | Description |
---|---|
Definition | External pressure applied during sintering to enhance densification and strength. |
Role in Sintering | Accelerates particle rearrangement, reduces porosity, and improves density. |
Influencing Factors | Temperature, particle size, and material composition. |
Impact on Properties | Higher mechanical strength, improved density, and structural integrity. |
Applications | Used in metal, ceramic, and composite manufacturing for superior performance. |
Optimize your sintering process for superior results—contact our experts today!