Hot isostatic pressing (HIP) is a manufacturing process that uses high temperature and pressure to improve the properties of materials. The size of particles used in HIP can vary depending on the application, but typically ranges from a few micrometers to several hundred micrometers. The process involves loading parts into a heating chamber, where inert argon gas is applied, and the temperature, pressure, and process time are closely controlled. HIP is used for processing high-performance ceramics, ferrites, and cemented carbides, as well as for net-shape forming of superalloys and titanium powders. The development of equilibrium and isostatic hot pressing has addressed some of the limitations of traditional hot pressing.
Key Points Explained:
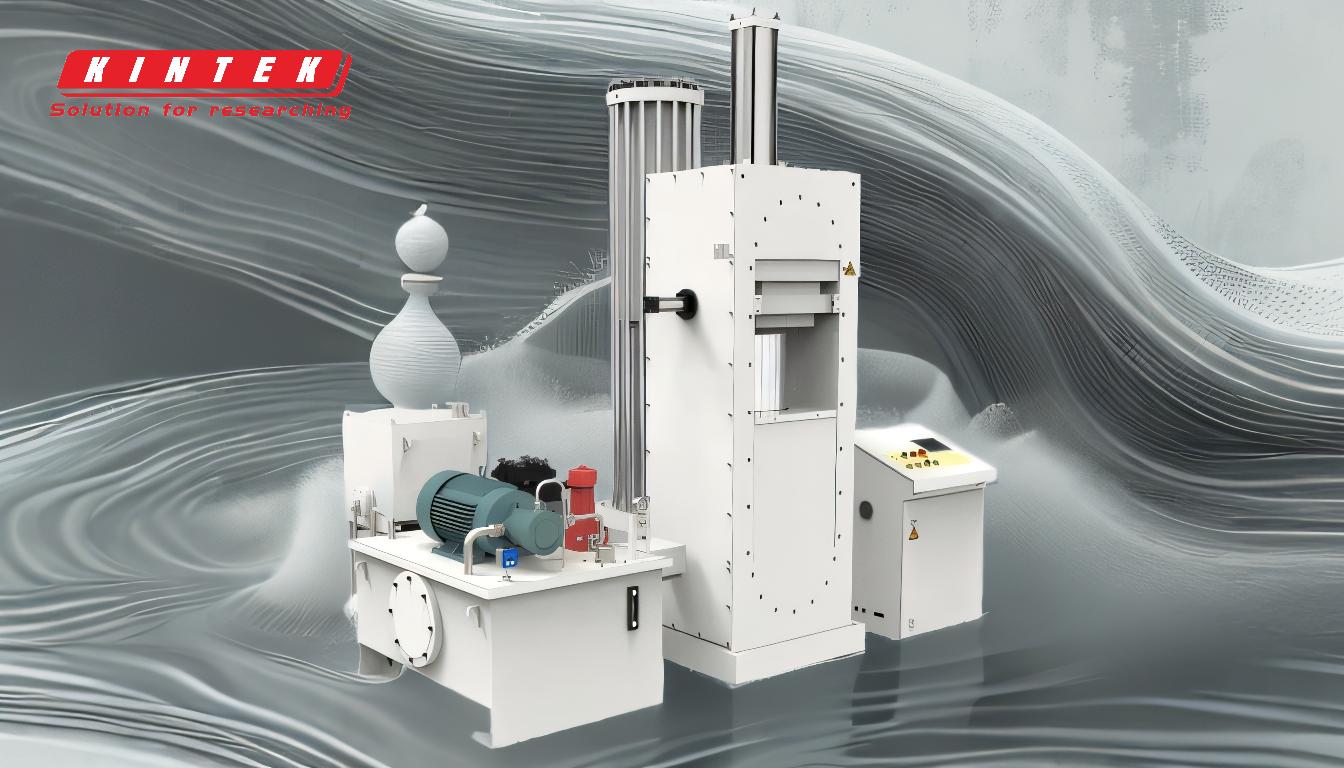
-
Particle Size in Hot Isostatic Pressing (HIP):
- The size of particles used in HIP can vary significantly depending on the material and application.
- Typically, particle sizes range from a few micrometers to several hundred micrometers.
- Smaller particles are often used for high-performance ceramics and ferrites, while larger particles may be used for cemented carbides and superalloys.
-
Applications of HIP:
- HIP is used for processing high-performance ceramics, ferrites, and cemented carbides.
- It is also used for net-shape forming of nickel-base superalloys and titanium powders.
- Other applications include compacting high-speed tool steel, diffusion bonding of materials, and eliminating voids in aerospace castings.
-
Process Details:
- The HIP process involves loading parts into a heating chamber where inert argon gas is applied.
- The chamber heats up, and the temperature, pressure, and total process time are closely monitored and controlled.
- The process ends with a depressurization phase and a cool-down period to ensure the parts are safe to remove.
-
Warm Isostatic Press:
- A warm isostatic press is usually heated to the temperature of the liquid medium first.
- The heated liquid medium is continuously injected into the sealed pressing cylinder through a booster source.
- The pressing cylinder is equipped with a heat generator to ensure accurate temperature control.
-
Advantages of HIP:
- HIP can remove defects from castings and heat-treat creep-damaged products.
- The development of equilibrium and isostatic hot pressing has overcome some of the drawbacks of the traditional hot pressing process.
-
Industry Expertise:
- HIP operations are managed by experienced engineers and technicians who provide vital support and understand customer requirements.
- This expertise ensures that the HIP process is optimized for each specific application.
In summary, the size of particles in hot isostatic pressing varies depending on the material and application, typically ranging from a few micrometers to several hundred micrometers. The process is widely used in various industries for improving material properties and is supported by experienced professionals to ensure optimal results.
Summary Table:
Aspect | Details |
---|---|
Particle Size Range | Few micrometers to several hundred micrometers |
Applications | High-performance ceramics, ferrites, cemented carbides, superalloys, titanium powders |
Process Details | Inert argon gas, controlled temperature/pressure, monitored process time |
Advantages | Defect removal, improved material properties, optimized for specific needs |
Industry Expertise | Managed by experienced engineers for tailored solutions |
Optimize your materials with HIP—contact our experts today for tailored solutions!