The Special Protection System (SPS) is a sophisticated equipment setup primarily used in material science and engineering for fabricating advanced materials with unique properties. It integrates multiple subsystems, including pressure, vacuum, water cooling, temperature measurement, power supply, and control systems, to achieve precise control over the sintering process. The SPS process leverages pulsed electric currents and the "spark plasma effect" to enable rapid heating, short processing times, and low sintering temperatures, making it ideal for creating materials with tailored microstructures and enhanced properties. This system operates in a vacuum or controlled atmosphere to ensure material purity and prevent oxidation.
Key Points Explained:
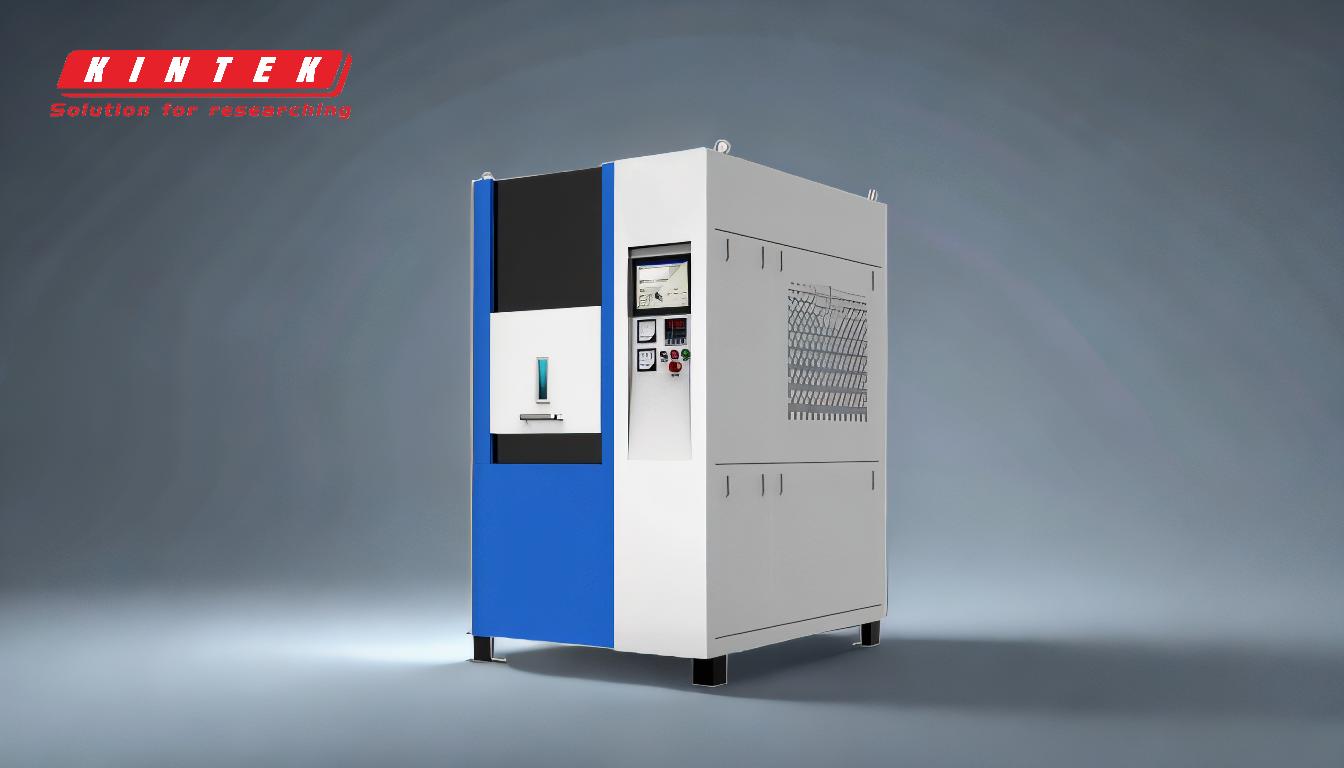
-
Definition and Purpose of SPS:
- The SPS system, also known as the Remedial Action Scheme (RAS), is designed to detect abnormal system conditions and take corrective actions to preserve system integrity and performance.
- In material science, SPS refers to a specialized sintering process that uses pulsed electric currents to achieve rapid heating and precise control over material properties.
-
Components of the SPS System:
- Pressure System: Ensures controlled application of pressure during the sintering process.
- Vacuum System: Maintains a vacuum or controlled atmosphere to prevent oxidation and contamination.
- Water Cooling System: Regulates temperature to prevent overheating of components.
- Temperature Measurement System: Monitors and controls the temperature during the process.
- Power Supply and Control System: Provides pulsed electric currents and manages the overall operation of the system.
-
Key Features of the SPS Process:
- Pulsed Electric Currents: Directly flows through the pressing die and the material, enabling rapid heating and short processing times.
- Spark Plasma Effect: Inhibits particle growth, allowing the creation of materials with unique compositions and properties.
- Precise Control: Offers accurate control over temperature, pressure, and heating rate, enabling the fabrication of materials with tailored microstructures.
-
Advantages of SPS:
- High Heating Rates: Achieves very fast heating times, reducing overall processing time.
- Low Sintering Temperatures: Operates at lower temperatures compared to conventional methods, preserving material properties.
- Material Purity: Operates in a vacuum or controlled atmosphere, preventing oxidation and ensuring high material purity.
-
Applications of SPS:
- Advanced Materials: Used to fabricate ceramics, composites, and alloys with enhanced properties.
- Research and Development: Ideal for creating materials with unique microstructures and compositions for experimental purposes.
- Industrial Manufacturing: Applied in industries requiring high-performance materials with precise control over properties.
-
Comparison with Traditional Methods:
- Conventional Hot Pressing: Typically involves slower heating rates and longer processing times, which can lead to particle growth and less control over material properties.
- SPS Advantages: Offers faster processing, lower temperatures, and better control, resulting in materials with superior properties.
By integrating advanced technologies and precise control mechanisms, the SPS system stands out as a powerful tool in material science, enabling the creation of innovative materials with exceptional properties.
Summary Table:
Aspect | Details |
---|---|
Definition | A sophisticated system for material fabrication using pulsed electric currents. |
Key Components | Pressure, vacuum, water cooling, temperature measurement, power supply, and control systems. |
Key Features | Rapid heating, spark plasma effect, precise control over temperature and pressure. |
Advantages | High heating rates, low sintering temperatures, and high material purity. |
Applications | Advanced ceramics, composites, alloys, R&D, and industrial manufacturing. |
Comparison | Faster, lower temperatures, and better control than traditional methods. |
Unlock the potential of advanced materials with SPS—contact our experts today to learn more!