Sputtering is a widely used physical vapor deposition (PVD) technique for creating thin films on substrates. It involves bombarding a target material with high-energy ions, typically from an inert gas like argon, in a vacuum chamber. This process dislodges atoms from the target, which then travel and deposit onto a substrate, forming a thin film. Sputtering is versatile and used in industries such as semiconductors, optics, and packaging. Techniques like RF and DC magnetron sputtering, ion beam sputtering, and reactive sputtering offer flexibility for different materials and applications. The process is highly controllable, enabling the deposition of high-quality, uniform films for advanced technological applications.
Key Points Explained:
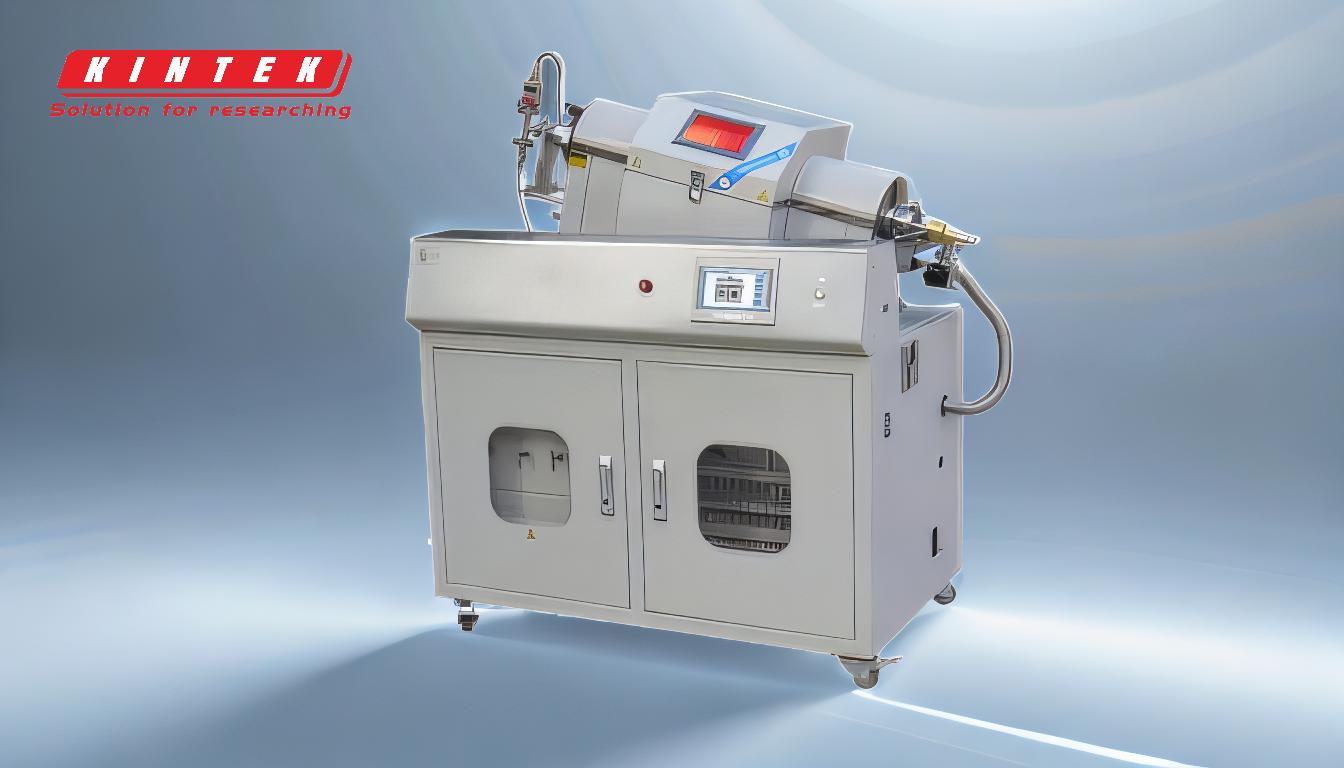
-
Overview of Sputtering:
- Sputtering is a physical vapor deposition (PVD) process used to deposit thin films on substrates.
- It involves bombarding a target material with high-energy ions, typically from an inert gas like argon, in a vacuum environment.
- The dislodged atoms from the target material travel and deposit onto a substrate, forming a thin film.
-
Key Components of the Sputtering Process:
- Vacuum Chamber: The process occurs in a vacuum to minimize contamination and ensure efficient deposition.
- Target Material: The material to be deposited, which is bombarded by ions.
- Substrate: The surface onto which the thin film is deposited, such as a silicon wafer or glass.
- Sputtering Gas: Typically an inert gas like argon, which is ionized to create the plasma.
- Power Supply: A voltage is applied to generate the plasma and accelerate ions toward the target.
-
Steps in the Sputtering Process:
- Ion Generation: A plasma is created by ionizing the sputtering gas, typically argon.
- Bombardment: High-energy ions from the plasma bombard the target material, dislodging atoms.
- Transport: The dislodged atoms travel through the vacuum and deposit onto the substrate.
- Condensation: The atoms condense on the substrate, forming a thin film.
-
Types of Sputtering Techniques:
- DC Magnetron Sputtering: Uses a direct current (DC) power supply and is suitable for conductive materials.
- RF Magnetron Sputtering: Uses radio frequency (RF) power, making it suitable for both conductive and non-conductive materials.
- Ion Beam Sputtering: Uses a focused ion beam for precise control over the deposition process.
- Reactive Sputtering: Involves introducing a reactive gas (e.g., oxygen or nitrogen) to form compound films during deposition.
-
Applications of Sputtering:
- Semiconductors: Used in the fabrication of integrated circuits and transistors.
- Optics: Creates reflective coatings for mirrors and anti-reflective coatings for lenses.
- Packaging: Deposits thin films on materials like potato chip bags for barrier properties.
- Solar Panels: Forms thin-film photovoltaic layers for solar cells.
- Data Storage: Used in the production of hard disk drives and optical disks.
-
Advantages of Sputtering:
- Versatility: Can deposit a wide range of materials, including metals, ceramics, and polymers.
- Uniformity: Produces highly uniform and dense thin films.
- Control: Offers precise control over film thickness and composition.
- Quality: Results in high-quality films with excellent adhesion and minimal defects.
-
Challenges and Considerations:
- Cost: Requires specialized equipment, making it relatively expensive.
- Complexity: The process involves multiple parameters (e.g., pressure, power, gas flow) that must be carefully controlled.
- Material Limitations: Some materials may be difficult to sputter due to low sputtering yields or reactivity issues.
By understanding these key points, one can appreciate the versatility and precision of the sputtering process, making it a cornerstone of modern thin film deposition technologies.
Summary Table:
Aspect | Details |
---|---|
Process Overview | Bombards target material with high-energy ions in a vacuum to deposit thin films. |
Key Components | Vacuum chamber, target material, substrate, sputtering gas, power supply. |
Steps | Ion generation, bombardment, transport, condensation. |
Techniques | DC/RF magnetron, ion beam, reactive sputtering. |
Applications | Semiconductors, optics, packaging, solar panels, data storage. |
Advantages | Versatility, uniformity, precise control, high-quality films. |
Challenges | Cost, complexity, material limitations. |
Discover how sputtering can enhance your thin film applications—contact our experts today!