The sputtering rate is a critical parameter in thin film deposition processes, representing the rate at which target material is ejected and deposited onto a substrate. It is influenced by factors such as the sputter yield, ion energy, target material properties, and sputtering conditions. The sputtering rate can be calculated using a specific equation that incorporates the sputter yield, molar weight of the target, material density, and ion current density. Understanding and controlling the sputtering rate is essential for achieving uniform and high-quality thin films in applications such as semiconductor manufacturing, optical coatings, and surface engineering.
Key Points Explained:
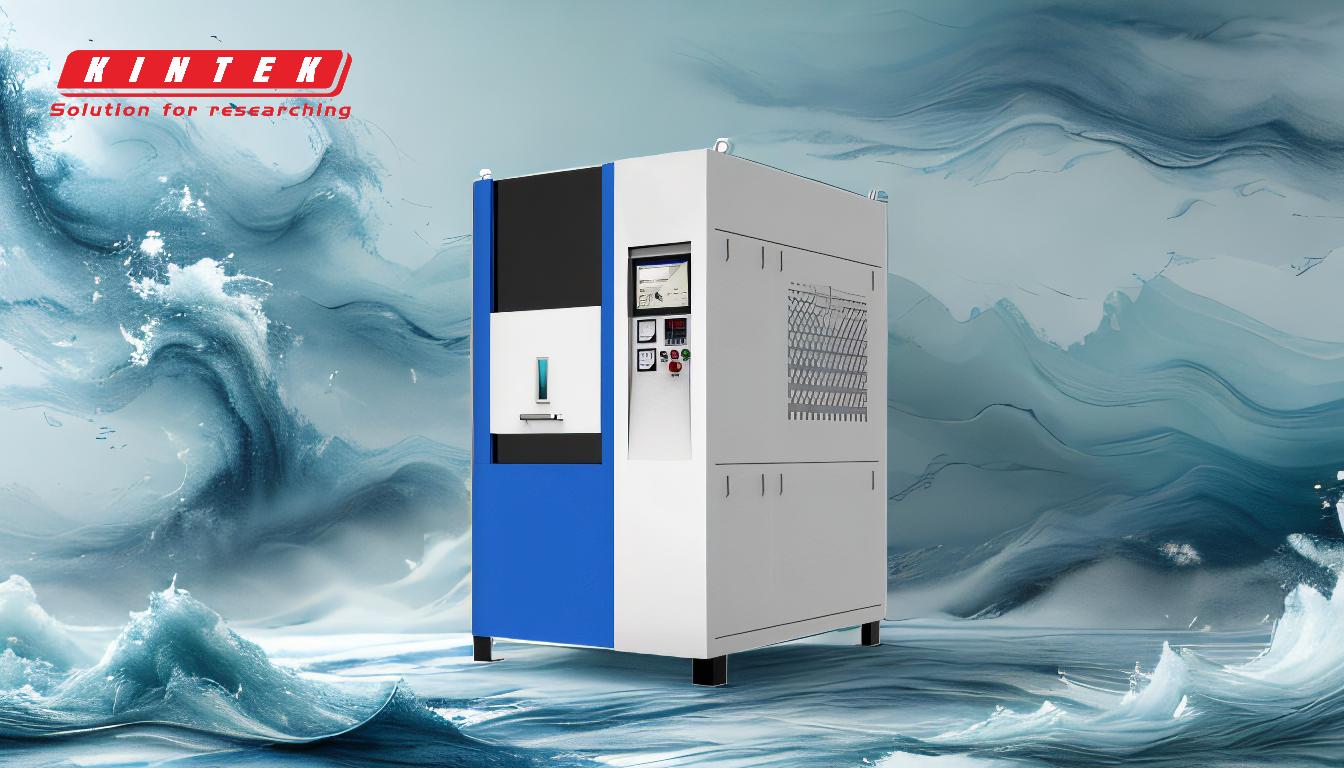
-
Definition of Sputtering Rate:
- The sputtering rate is defined as the number of monolayers per second sputtered from a target's surface. It quantifies how quickly material is removed from the target and deposited onto the substrate.
- Mathematically, it is represented by the equation:
[ \text{Sputtering rate} = \frac{MSj}{pN_A e} ]
where:- ( M ) = molar weight of the target material,
- ( S ) = sputter yield (number of target atoms ejected per incident ion),
- ( j ) = ion current density,
- ( p ) = material density,
- ( N_A ) = Avogadro's number,
- ( e ) = electron charge.
-
Factors Influencing Sputtering Rate:
-
Sputter Yield (S): The number of target atoms ejected per incident ion. It depends on:
- Incident ion energy,
- Mass of the ions and target atoms,
- Angle of incidence,
- Surface binding energy of the target material.
- Ion Current Density (j): The density of ions bombarding the target surface. Higher ion current density increases the sputtering rate.
-
Target Material Properties:
- Molar weight (( M )): Heavier atoms may have lower sputtering rates due to higher binding energies.
- Material density (( p )): Denser materials may require more energy to sputter.
-
Sputtering Conditions:
- Type of power source (DC or RF): DC sputtering is more common for conductive materials, while RF sputtering is used for insulators.
- Chamber pressure: Optimal pressure ensures efficient energy transfer and uniform deposition.
- Kinetic energy of emitted particles: Higher energy improves surface mobility and film quality.
-
Sputter Yield (S): The number of target atoms ejected per incident ion. It depends on:
-
Impact of Sputtering Rate on Thin Film Deposition:
- Uniformity: A consistent sputtering rate is crucial for achieving uniform thin films. Variations in the rate can lead to uneven thickness and defects.
- Film Quality: The sputtering rate affects the microstructure, density, and adhesion of the deposited film. Controlled rates ensure high-quality films with desired properties.
- Process Efficiency: Optimizing the sputtering rate improves material utilization and reduces waste, making the process more cost-effective.
-
Practical Considerations for Equipment and Consumable Purchasers:
- Target Material Selection: Choose materials with appropriate molar weight, density, and binding energy to achieve the desired sputtering rate.
- Power Source Compatibility: Ensure the sputtering system (DC or RF) is compatible with the target material and application requirements.
- Process Control: Invest in systems with precise control over ion energy, current density, and chamber pressure to maintain consistent sputtering rates.
- Cost Efficiency: Evaluate the trade-offs between sputtering rate, film quality, and operational costs to select the most economical solution.
-
Applications of Sputtering Rate Control:
- Semiconductor Manufacturing: Precise control of sputtering rates is essential for depositing thin films in integrated circuits and microelectronics.
- Optical Coatings: Uniform sputtering rates ensure high-quality reflective and anti-reflective coatings for lenses and mirrors.
- Surface Engineering: Controlled sputtering rates are used to modify surface properties, such as hardness, wear resistance, and corrosion resistance.
By understanding the factors influencing the sputtering rate and their impact on thin film deposition, equipment and consumable purchasers can make informed decisions to optimize their processes and achieve high-quality results.
Summary Table:
Aspect | Details |
---|---|
Definition | Number of monolayers per second sputtered from a target's surface. |
Equation | ( \text{Sputtering rate} = \frac{MSj}{pN_A e} ) |
Key Factors | Sputter yield, ion current density, target material properties, conditions. |
Impact on Deposition | Uniformity, film quality, process efficiency. |
Applications | Semiconductor manufacturing, optical coatings, surface engineering. |
Optimize your thin film deposition process—contact our experts today for tailored solutions!