Sintering strength refers to the mechanical properties and structural integrity achieved through the sintering process, which involves heating compacted powder materials to a temperature below their melting point to bond particles together. This process is crucial in manufacturing high-performance materials, including dental restorations, ceramics, and metals. The strength of sintering is influenced by factors such as temperature control, atmosphere regulation, and the material's inherent properties. A well-controlled sintering process ensures high dimensional precision, reduced micro-porosity, and optimal functional performance of the final product. Sintering furnaces play a pivotal role in achieving these outcomes by maintaining precise thermal and atmospheric conditions.
Key Points Explained:
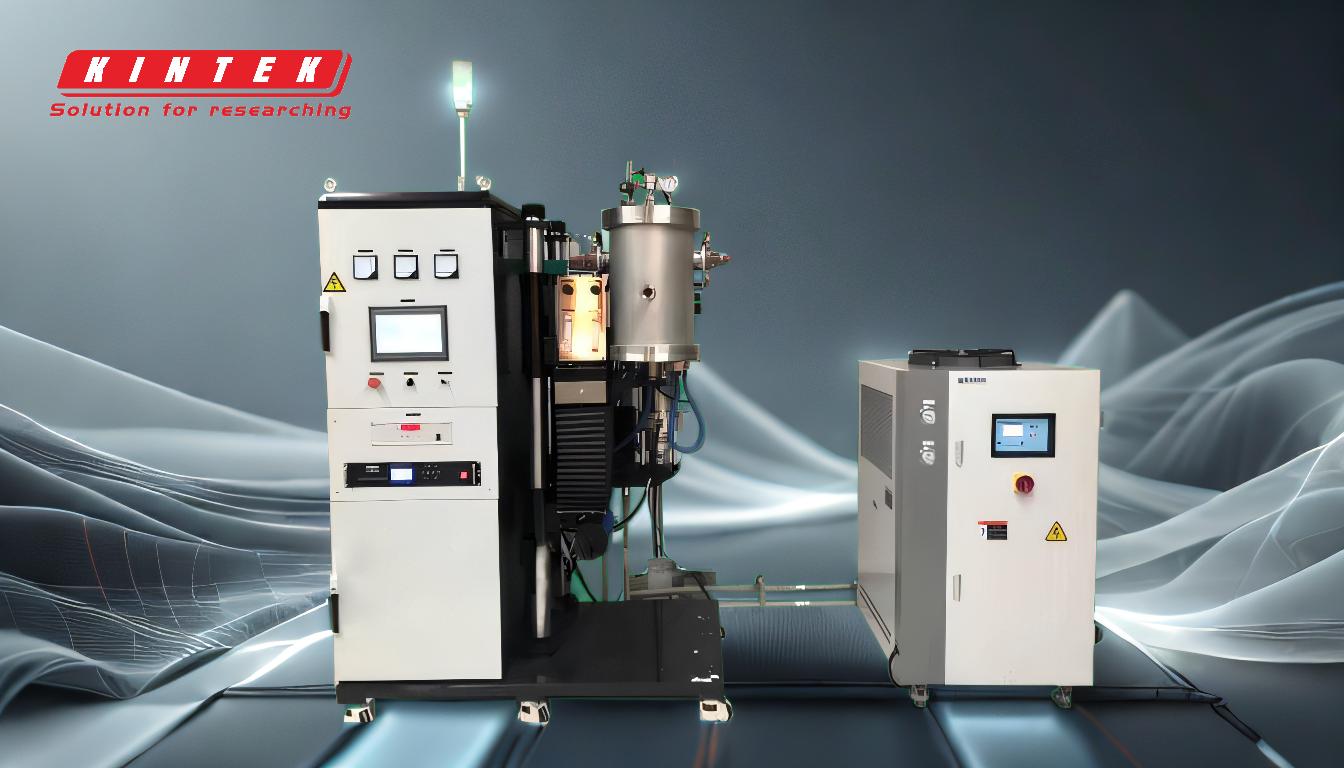
-
Definition of Sintering Strength:
- Sintering strength refers to the mechanical durability and structural cohesion of a material after undergoing the sintering process. It is achieved by heating compacted powder particles to a temperature below their melting point, allowing them to bond without liquefaction. This process enhances the material's density, reduces porosity, and improves its mechanical properties, such as hardness and tensile strength.
-
Role of Temperature Control:
- Temperature is a critical factor in sintering. Precise control ensures that the material reaches the optimal bonding temperature without melting. In a sintering furnace, resistance or induction heating elements are used to generate and maintain the required temperature. Advanced thermal control systems, including temperature sensors and controllers, ensure consistent heating, which is essential for achieving uniform sintering and high material strength.
-
Importance of Atmosphere Regulation:
- The sintering atmosphere, whether inert, reducing, or vacuum, significantly impacts the final product's quality. Atmosphere control prevents oxidation, contamination, or unwanted chemical reactions during sintering. For example, in dental sintering furnaces, an inert atmosphere ensures the stability and biocompatibility of dental restorations. Proper atmosphere regulation also minimizes defects like cracks or warping, enhancing the material's strength.
-
Micro-Porosity and Dimensional Precision:
- After sintering, the material often retains a certain level of micro-porosity, which can influence its mechanical properties. Controlled sintering reduces porosity to an acceptable level, ensuring high dimensional precision and functional performance. This is particularly important in applications like dental restorations, where precision and durability are critical.
-
Applications of Sintering Furnaces:
- Sintering furnaces are indispensable in various industries, including dentistry, ceramics, and metallurgy. They enable the production of thermally resistant molds, high-strength components, and biocompatible dental prosthetics. By maintaining temperatures below the material's melting point, sintering furnaces shape the material without compromising its structural integrity.
-
Factors Influencing Sintering Strength:
- Several factors contribute to the strength of sintered materials, including:
- Material Properties: The composition and particle size of the powder affect bonding and densification.
- Heating Rate: Gradual heating prevents thermal shock and ensures uniform sintering.
- Holding Time: Prolonged exposure to sintering temperatures enhances particle bonding and reduces porosity.
- Cooling Rate: Controlled cooling prevents stress-induced defects and maintains material strength.
- Several factors contribute to the strength of sintered materials, including:
-
Advantages of Sintering:
- Sintering offers numerous benefits, such as:
- High Strength-to-Weight Ratio: Sintered materials are lightweight yet strong, making them ideal for aerospace and automotive applications.
- Cost-Effectiveness: The process minimizes material waste and reduces production costs.
- Versatility: Sintering can be applied to a wide range of materials, including metals, ceramics, and polymers.
- Sintering offers numerous benefits, such as:
In conclusion, the strength of sintering is a result of precise temperature and atmosphere control, material properties, and process optimization. Sintering furnaces are essential tools in achieving high-quality, durable materials for various industrial applications. By understanding and controlling these factors, manufacturers can produce components with superior mechanical properties and dimensional accuracy.
Summary Table:
Aspect | Details |
---|---|
Definition | Mechanical durability and structural cohesion achieved through sintering. |
Key Factors | Temperature control, atmosphere regulation, material properties. |
Applications | Dental restorations, ceramics, metals, and high-performance components. |
Advantages | High strength-to-weight ratio, cost-effectiveness, and material versatility. |
Role of Sintering Furnace | Ensures precise thermal and atmospheric conditions for optimal results. |
Unlock the full potential of sintering for your materials—contact our experts today!