Quenching is a critical process in heat treatment that involves rapid cooling of a metal to achieve desired mechanical properties, such as hardness and strength. The temperature and time for quenching depend on the type of metal, the desired properties, and the specific application. The process typically involves heating the metal to a specific temperature (austenitizing temperature) and then rapidly cooling it in a quenching medium like water, oil, or air. The exact temperature and time vary based on the material and the intended outcome, but the goal is to achieve a uniform and controlled transformation in the metal's microstructure.
Key Points Explained:
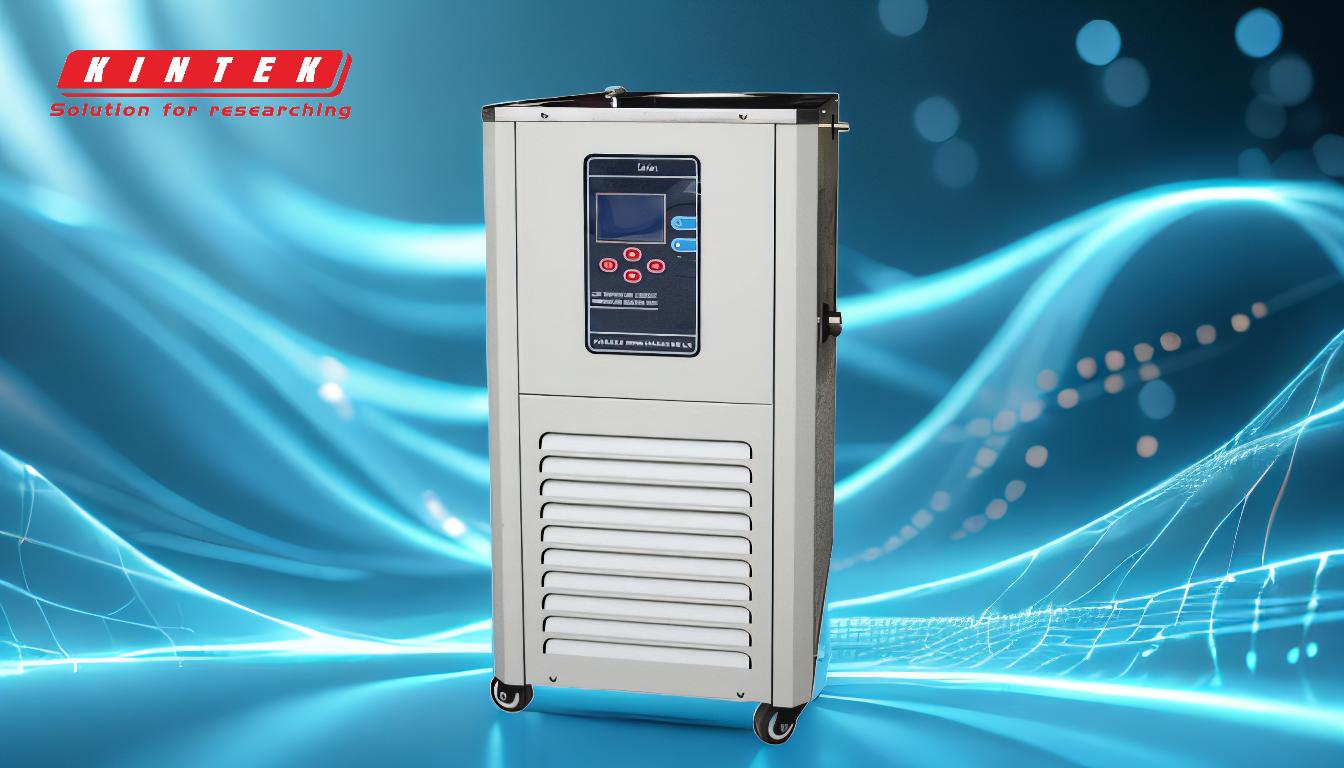
-
Austenitizing Temperature:
- The temperature at which the metal is heated before quenching is crucial. For most steels, this temperature is typically between 800°C to 900°C, depending on the specific alloy composition. This temperature ensures that the metal's microstructure transforms into austenite, a phase that allows for the desired hardening during quenching.
-
Soak Time:
- The soak time, or the duration the metal is held at the austenitizing temperature, is essential for achieving uniform heating throughout the workpiece. This time can range from a few minutes to several hours, depending on the size, shape, and type of metal. For example, in vacuum heat treatment, soak times can range from three to 24 hours, as mentioned in the reference.
-
Quenching Medium and Cooling Rate:
- The choice of quenching medium (water, oil, air, or polymer solutions) significantly affects the cooling rate and, consequently, the final properties of the metal. Water provides the fastest cooling rate, making it suitable for high-hardness applications, while oil offers a slower cooling rate, reducing the risk of cracking or distortion.
-
Material-Specific Considerations:
- Different metals and alloys require specific quenching temperatures and times. For instance, tool steels may require higher temperatures and longer soak times compared to carbon steels. The technical requirements, service conditions, and performance needs of the workpiece, as highlighted in the reference, play a significant role in determining these parameters.
-
Controlled Environment:
- Modern heat treatment processes, such as vacuum heat treatment, use computer-controlled systems to ensure repeatability and uniformity. This minimizes the risk of defects and ensures consistent results across multiple batches.
-
Post-Quenching Processes:
- After quenching, additional processes like tempering may be required to reduce brittleness and improve toughness. The temperature and duration of tempering are also carefully controlled to achieve the desired balance of hardness and ductility.
By carefully selecting the heating temperature, soak time, and quenching medium, manufacturers can achieve the desired mechanical properties in the metal while minimizing deformation and ensuring uniformity. The process requires a deep understanding of the material's properties and the intended application to optimize the quenching parameters effectively.
Summary Table:
Parameter | Details |
---|---|
Austenitizing Temperature | 800°C to 900°C for most steels, depending on alloy composition. |
Soak Time | Few minutes to several hours, depending on metal type and size. |
Quenching Medium | Water (fast cooling), oil (slower cooling), air, or polymer solutions. |
Material-Specific | Tool steels require higher temperatures and longer soak times than carbon steels. |
Post-Quenching | Tempering may be needed to reduce brittleness and improve toughness. |
Need help optimizing your quenching process? Contact our experts today for tailored solutions!