Sintering is a critical process in metallurgy and materials science, where powdered metals are heated to high temperatures below their melting points to fuse particles together, creating a solid structure. The sintering temperature varies depending on the material and desired properties, typically ranging between 750°C and 1300°C (1382°F to 2372°F). This process is conducted in controlled environments, often using inert or reducing atmospheres to prevent oxidation and ensure proper bonding. The choice of temperature, atmosphere, and supporting materials plays a significant role in achieving the desired mechanical and physical properties of the sintered product.
Key Points Explained:
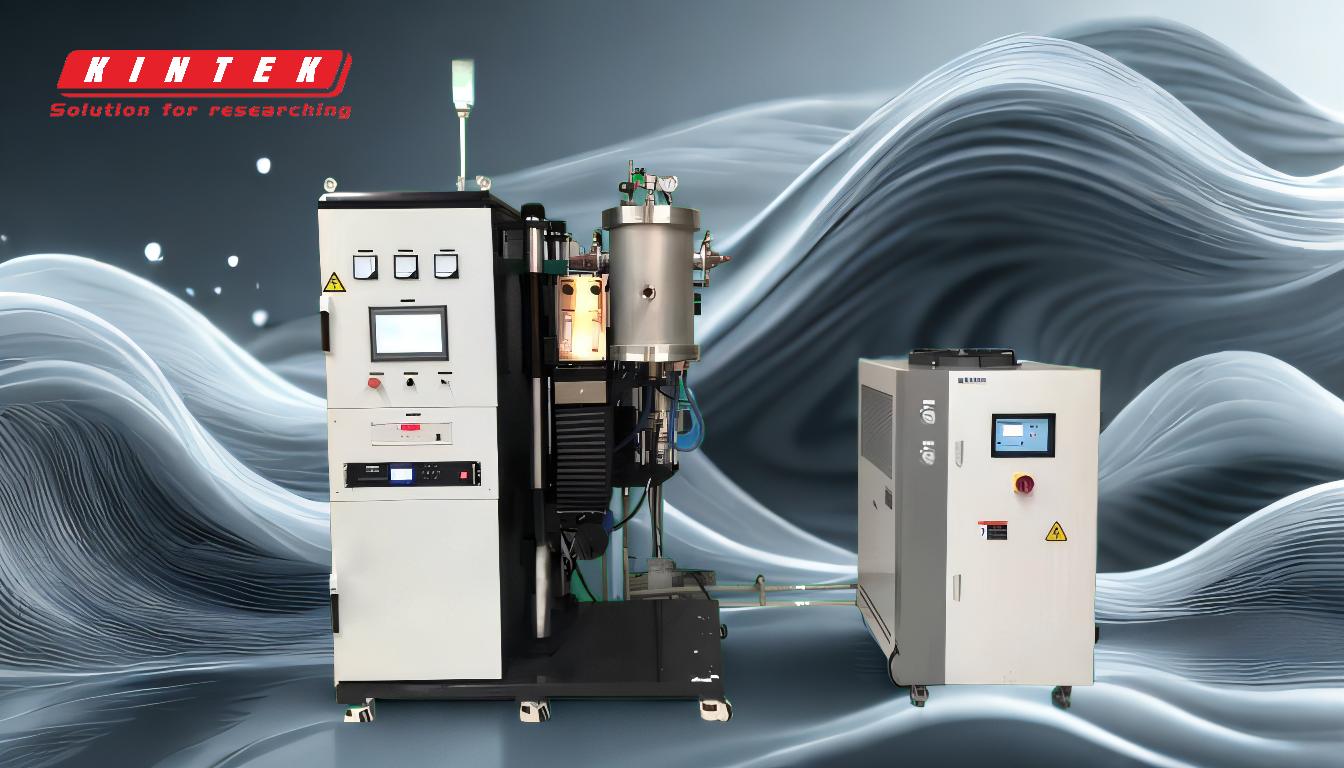
-
Temperature Range for Sintering Metals:
- Sintering temperatures generally range from 750°C to 1300°C (1382°F to 2372°F), depending on the material and application.
- For most metals, sintering occurs at temperatures below the melting point of the primary constituent to avoid liquefaction while still enabling particle fusion.
- Example: Copper, which has a melting point of 1085°C, is typically sintered at around 850°C to 950°C.
-
Factors Influencing Sintering Temperature:
- Material Composition: Different metals and alloys have unique sintering temperature requirements. For instance, steel may require higher temperatures than copper or bronze.
- Desired Properties: The mechanical strength, density, and porosity of the final product influence the choice of sintering temperature.
- Atmosphere: The type of atmosphere (inert, reducing, or oxidizing) used during sintering can affect the required temperature and the final product quality.
-
Controlled Atmosphere for Sintering:
- Sintering is often performed in inert or reducing atmospheres (e.g., nitrogen, hydrogen, or endothermic gas) to prevent oxidation and contamination.
- In vacuum sintering, pure metals are sintered without surface contamination, making it ideal for high-purity applications.
- Shielding gases are essential for sintering at atmospheric pressure to maintain the integrity of the metal.
-
Supporting Materials and Techniques:
- Refractory materials like Al2O3 (for copper and bronze) or Steel Blend (for steels) are used to support the shape of the sintered part.
- Sintering Carbon is employed to manage oxygen exposure and ensure a controlled environment.
-
Comparison with Melting:
- Sintering occurs at lower temperatures than melting, as it relies on particle fusion rather than complete liquefaction.
- Melting requires temperatures high enough to turn the material into a liquid, whereas sintering achieves bonding without reaching the melting point.
-
Applications and Metals Suitable for Sintering:
- Most metals, including pure metals and alloys, can be sintered. Common examples include copper, bronze, steel, and titanium.
- Sintering is widely used in manufacturing processes such as powder metallurgy, 3D printing, and ceramic production.
By understanding these key points, purchasers of equipment and consumables can make informed decisions about the sintering process, ensuring optimal results for their specific applications.
Summary Table:
Aspect | Details |
---|---|
Temperature Range | 750°C to 1300°C (1382°F to 2372°F) |
Key Influencing Factors | Material composition, desired properties, and sintering atmosphere |
Controlled Atmospheres | Inert (e.g., nitrogen, hydrogen) or vacuum for oxidation prevention |
Supporting Materials | Al2O3, Steel Blend, and Sintering Carbon for shape support and environment |
Applications | Powder metallurgy, 3D printing, ceramic production, and more |
Optimize your sintering process with expert guidance—contact us today!