The temperature of a rotary kiln varies significantly depending on its application, design, and the materials being processed. Generally, rotary kilns operate within a broad temperature range, from 200°C to 2500°C, to accommodate diverse industrial processes. For instance, flames inside the kiln can reach up to 1900°C to heat raw materials to approximately 1500°C. Indirect rotary kilns typically maintain furnace tube temperatures between 1200-1300°C, with material temperatures below 1150°C. Operational efficiency and temperature control are influenced by factors such as material properties, kiln design, and process requirements. Understanding these variables is crucial for optimizing kiln performance and achieving desired outcomes.
Key Points Explained:
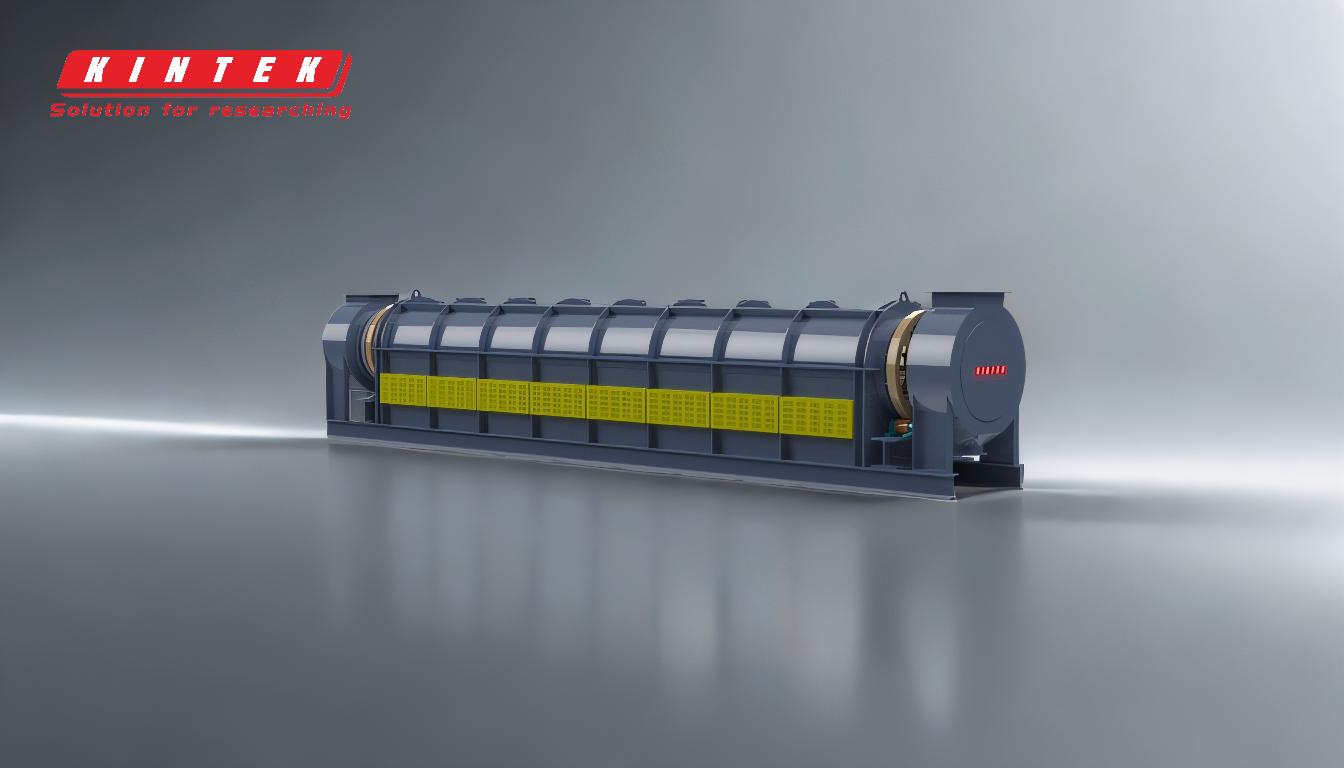
-
Temperature Range of Rotary Kilns:
- Rotary kilns operate across a wide temperature spectrum, typically ranging from 200°C to 2500°C. This flexibility allows them to support various industrial processes, from low-temperature drying to high-temperature calcination or reduction.
-
Flame and Material Temperatures:
- During operation, flames within the kiln can reach temperatures as high as 1900°C (3452°F), which is necessary to heat raw materials to approximately 1500°C (2732°F). This high temperature ensures effective thermal processing of materials.
-
Indirect Rotary Kiln Temperatures:
- In indirect rotary kilns, the furnace tube temperature is maintained between 1200-1300°C, while the material being processed typically remains below 1150°C. This setup is ideal for processes requiring precise temperature control and minimal direct contact between flames and materials.
-
Factors Influencing Kiln Temperature:
- The operating temperature of a rotary kiln is influenced by several factors, including:
- Material Properties: Particle size, bulk density, abrasiveness, corrosiveness, specific heat, and thermal conductivity.
- Process Requirements: Desired temperature profiles, heat of reaction, and chemical composition of the materials.
- Kiln Design: Inclination angle, rotation speed, material flow rate, and discharge rate.
- The operating temperature of a rotary kiln is influenced by several factors, including:
-
Operational Efficiency and Temperature Control:
- Efficient operation of a rotary kiln depends on maintaining optimal temperatures, which are influenced by:
- Residence Time: The duration materials spend in the kiln.
- Charge Holdup: The amount of material retained at the discharge end.
- Reducing Conditions: Temperature, reactivity, and quantity of reductants used in the process.
- Efficient operation of a rotary kiln depends on maintaining optimal temperatures, which are influenced by:
-
Applications and Temperature Variations:
- Rotary kilns are used in a variety of industries, each requiring specific temperature ranges:
- Low-Temperature Processes: Such as drying or preheating, typically operating between 200°C to 600°C.
- High-Temperature Processes: Such as calcination or smelting, operating between 1200°C to 2500°C.
- Rotary kilns are used in a variety of industries, each requiring specific temperature ranges:
-
Design Considerations for Temperature Management:
- The design of a rotary kiln must account for:
- Heat Generation: From volatilization or combustion of materials.
- Retention Time: Ensuring materials are exposed to the required temperature for the necessary duration.
- Bed Profile: Managing how full the kiln should be to achieve uniform heating.
- The design of a rotary kiln must account for:
-
Industrial Examples:
- Cement Production: Typically operates at temperatures around 1450°C to facilitate clinker formation.
- Lime Calcination: Requires temperatures of 900-1200°C to convert limestone into lime.
- Metal Smelting: Can involve temperatures exceeding 2000°C for processes like iron or aluminum production.
By understanding these key points, equipment and consumable purchasers can make informed decisions about selecting the right rotary kiln for their specific needs, ensuring optimal performance and efficiency.
Summary Table:
Key Aspect | Details |
---|---|
Temperature Range | 200°C to 2500°C |
Flame Temperature | Up to 1900°C (3452°F) |
Material Temperature | ~1500°C (2732°F) |
Indirect Kiln Tube Temp | 1200-1300°C |
Material Temp (Indirect) | Below 1150°C |
Influencing Factors | Material properties, process requirements, kiln design |
Applications | Cement production (1450°C), lime calcination (900-1200°C), metal smelting (>2000°C) |
Need a rotary kiln tailored to your industrial needs? Contact our experts today for a customized solution!