The temperature of PECVD (Plasma-Enhanced Chemical Vapor Deposition) oxide varies depending on the specific process and equipment used. Generally, PECVD operates at relatively low temperatures compared to thermal CVD, typically ranging from near room temperature (RT) to around 350°C, with some processes extending up to 400°C or higher. This low-temperature range is advantageous for temperature-sensitive substrates, such as those used in semiconductor manufacturing. Higher temperatures within this range tend to produce higher-quality films with lower hydrogen content and slower etch rates, while lower temperatures may result in films more prone to defects like pinholes.
Key Points Explained:
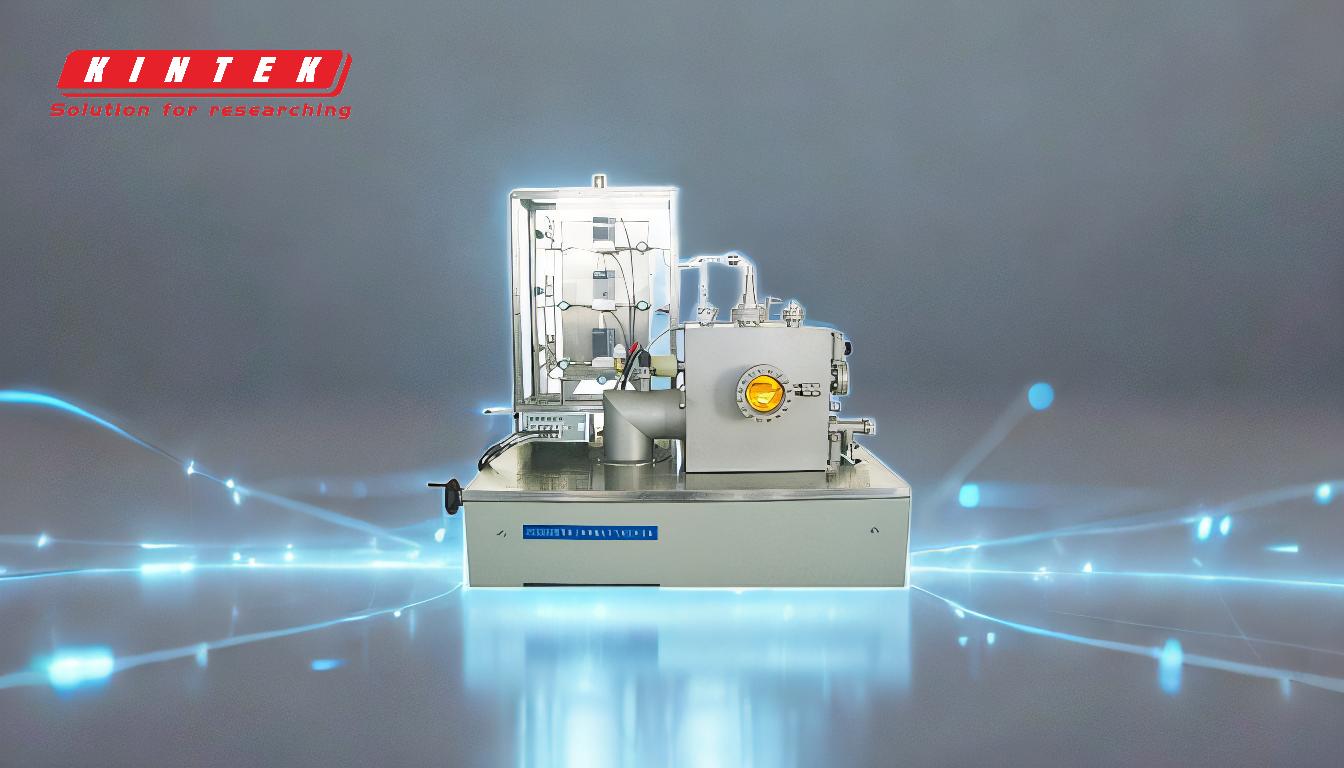
-
Typical Temperature Range for PECVD Oxide:
- PECVD processes typically operate between 200°C and 400°C, with some processes extending as low as 80°C or as high as 600°C.
- The most commonly cited range is 200°C to 350°C, which balances film quality and substrate compatibility.
-
Benefits of Low-Temperature Processing:
- PECVD is designed to work at low temperatures, often starting near room temperature (RT) with no intentional heating, making it suitable for temperature-sensitive substrates.
- This is particularly useful in applications where high temperatures could damage the substrate or other materials in the device.
-
Impact of Temperature on Film Quality:
-
Higher temperatures (e.g., 350°C to 400°C) result in higher-quality films with:
- Lower hydrogen content, which improves film stability and reduces defects.
- Slower etch rates, making the films more resistant to wet and dry plasma etching processes.
-
Lower temperatures (e.g., 80°C to 250°C) can lead to films that are:
- Amorphous and non-stoichiometric, meaning they lack a well-defined crystalline structure and precise chemical composition.
- More prone to pinholes and other defects, which can compromise film integrity.
-
Higher temperatures (e.g., 350°C to 400°C) result in higher-quality films with:
-
Process Flexibility:
- PECVD equipment can operate across a wide temperature range, from near room temperature up to 400°C or higher, depending on the specific application and equipment capabilities.
- Some systems are designed to handle temperatures as high as 540°C, though this is less common.
-
Pressure Considerations:
- PECVD processes typically operate at low pressures, in the range of 1 to 2 Torr, which complements the low-temperature processing to achieve high-quality films.
-
Trade-offs in Temperature Selection:
- Higher temperatures are preferred for applications requiring high-quality, defect-free films, but they may not be suitable for all substrates.
- Lower temperatures are advantageous for temperature-sensitive materials, but may require additional post-processing to improve film quality.
-
Equipment Limitations:
- The maximum temperature for PECVD equipment is typically around 350°C to 400°C, though some specialized systems can handle higher temperatures up to 540°C.
By understanding these key points, a purchaser can make informed decisions about the appropriate temperature settings for their specific PECVD oxide deposition needs, balancing film quality, substrate compatibility, and process requirements.
Summary Table:
Aspect | Details |
---|---|
Typical Temperature Range | 200°C to 400°C (commonly 200°C to 350°C), with some processes at 80°C to 600°C. |
Low-Temperature Benefits | Suitable for temperature-sensitive substrates, starting near room temperature. |
High-Temperature Effects | Higher-quality films with lower hydrogen content and slower etch rates. |
Low-Temperature Effects | Films may be amorphous, non-stoichiometric, and prone to defects like pinholes. |
Process Flexibility | Operates from near room temperature up to 400°C or higher, depending on equipment. |
Pressure Range | Typically 1 to 2 Torr, complementing low-temperature processing. |
Trade-offs | Higher temps for quality vs. lower temps for substrate compatibility. |
Equipment Limits | Max temperature typically 350°C to 400°C, with some systems up to 540°C. |
Need help selecting the right PECVD oxide temperature for your application? Contact our experts today for tailored solutions!