Plasma deposition, particularly in processes like Plasma-Enhanced Chemical Vapor Deposition (PECVD), operates at significantly lower temperatures compared to traditional Chemical Vapor Deposition (CVD). While CVD typically requires temperatures around 1000°C, plasma deposition can achieve similar results at much lower temperatures, often between 200-400°C. This is because the plasma provides the necessary energy to activate chemical reactions without relying solely on thermal energy. The lower temperature range is beneficial for substrates that cannot withstand high temperatures, such as polymers or certain metals. Additionally, the use of plasma allows for better control over film properties and reduces thermal stress, which is a common issue in high-temperature processes like CVD.
Key Points Explained:
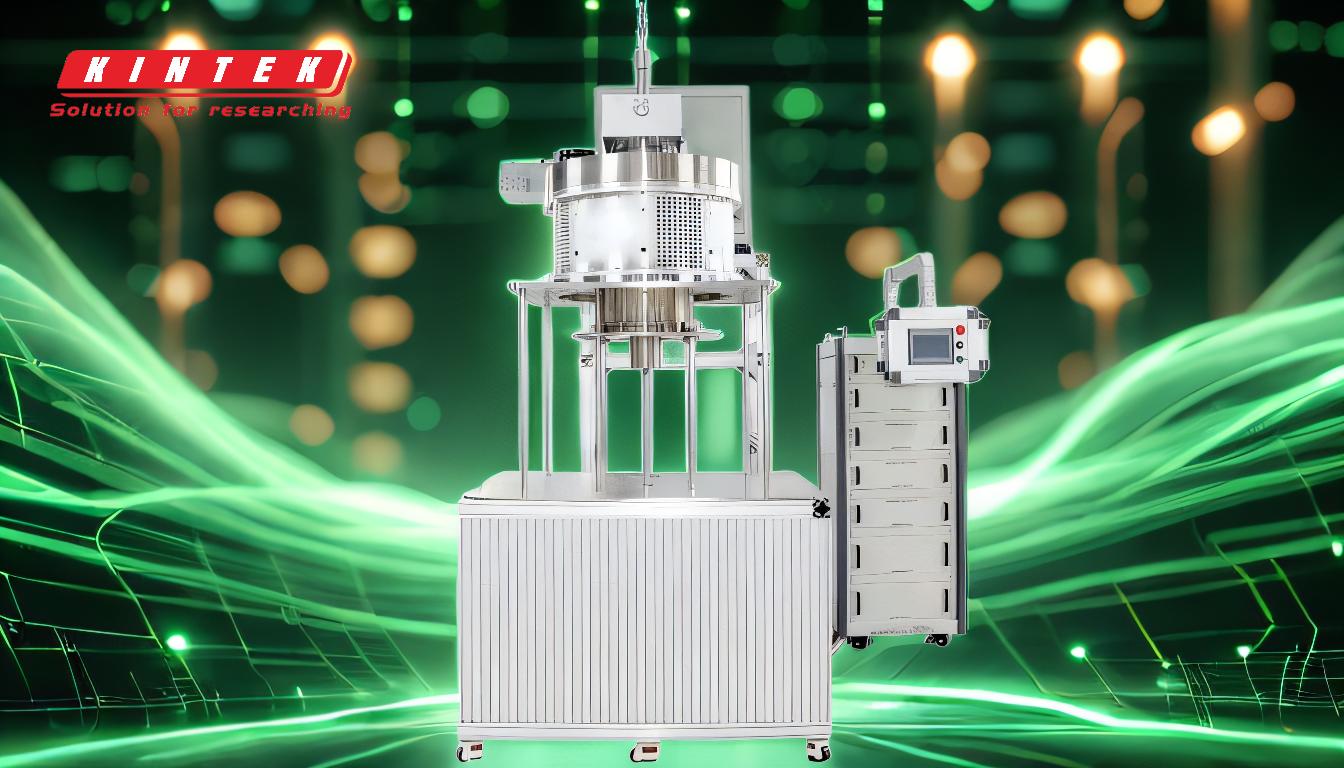
-
Temperature Range in Plasma Deposition:
- Plasma deposition, including PECVD, typically operates at temperatures between 200-400°C. This is significantly lower than the 1000°C required for traditional chemical vapor deposition (CVD).
- The lower temperature is achieved by using plasma to provide the energy needed for chemical reactions, rather than relying solely on thermal energy.
-
Advantages of Lower Temperatures:
- Substrate Compatibility: Many substrates, such as polymers and certain metals, cannot withstand the high temperatures required for CVD. Plasma deposition allows these materials to be coated without damage.
- Reduced Thermal Stress: High temperatures can cause thermal stress due to differences in thermal expansion between the substrate and the deposited film. Lower temperatures in plasma deposition minimize this issue, leading to better film adhesion and fewer defects.
-
Comparison with CVD:
- Temperature: CVD processes typically require temperatures around 1000°C, which is much higher than the 200-400°C range of plasma deposition.
- Energy Source: In CVD, thermal energy drives the chemical reactions, while in plasma deposition, the energy is provided by the plasma, allowing for lower temperatures.
- Applications: The lower temperature range of plasma deposition makes it suitable for a wider range of applications, including those involving temperature-sensitive materials.
-
Thermal Stress Considerations:
- In CVD, thermal stress is a significant concern, especially during the cooling phase after deposition. The difference in thermal expansion coefficients between the substrate and the film can lead to cracking or delamination.
- Plasma deposition reduces the risk of thermal stress by operating at lower temperatures, which minimizes the thermal expansion mismatch and results in more stable films.
-
Process Control and Film Properties:
- The use of plasma in deposition processes allows for better control over film properties such as thickness, uniformity, and composition.
- The lower temperatures also enable more precise control over the deposition process, reducing the likelihood of unwanted side reactions or degradation of the substrate.
In summary, plasma deposition offers a lower-temperature alternative to traditional CVD, making it suitable for a broader range of materials and applications. The use of plasma as an energy source allows for precise control over the deposition process, resulting in high-quality films with minimal thermal stress. This makes plasma deposition an attractive option for industries requiring coatings on temperature-sensitive substrates.
Summary Table:
Aspect | Plasma Deposition | Traditional CVD |
---|---|---|
Temperature Range | 200-400°C | ~1000°C |
Energy Source | Plasma | Thermal Energy |
Substrate Compatibility | Polymers, Metals | Limited by High Temp |
Thermal Stress | Minimal | High Risk |
Applications | Broad, Sensitive Materials | High-Temp Materials |
Learn how plasma deposition can enhance your material coating process—contact our experts today!