The temperature for sintering ceramics, particularly in dental applications, typically ranges between 1200°C and 1400°C. This high temperature is essential to facilitate atomic diffusion across particle boundaries, enabling particles to fuse together without reaching the material's melting point. The process involves several stages, including powder preparation, heating, particle merging, and solidification. For materials like zirconia, the sintering temperature often exceeds 1100°C to 1200°C, with some furnaces operating closer to 1500°C to achieve maximum density. The precise temperature depends on the material's properties and the desired outcome, ensuring optimal density and structural integrity.
Key Points Explained:
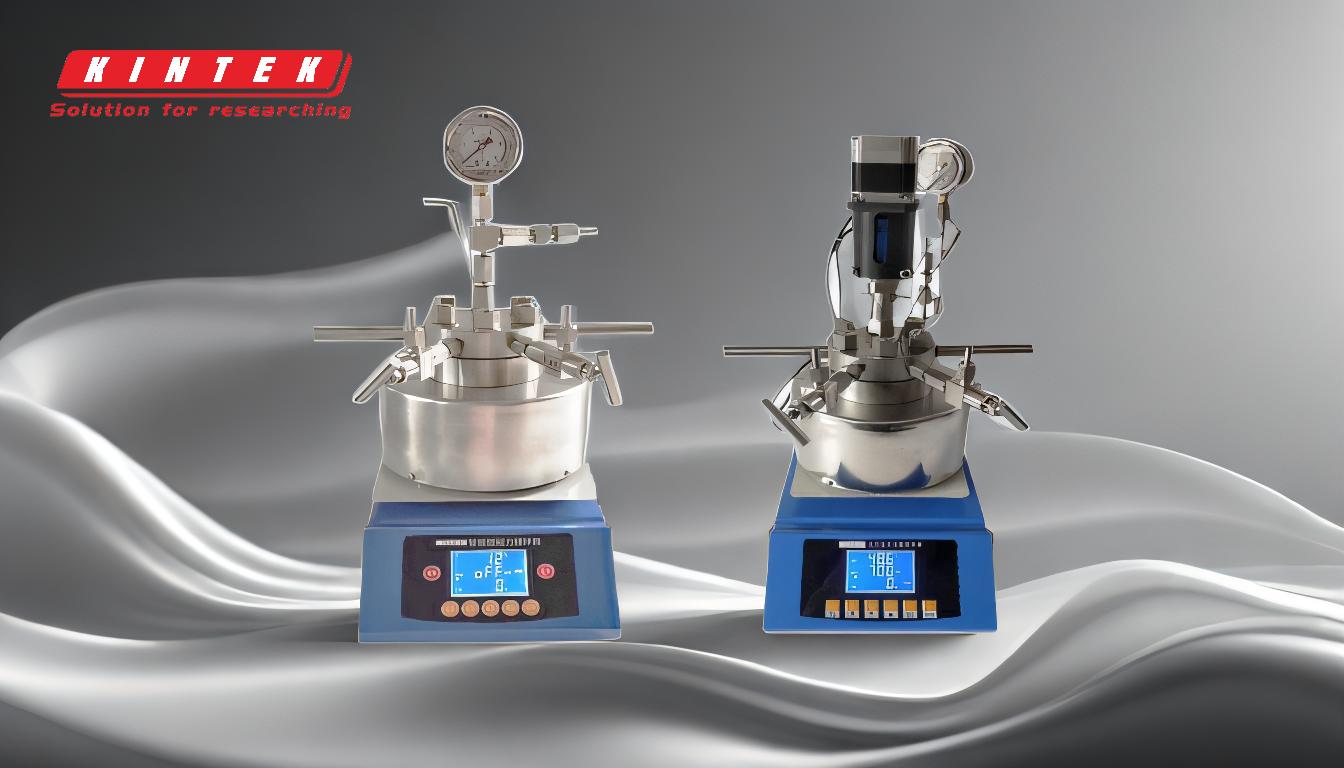
-
Temperature Range for Sintering Ceramics:
- The sintering process typically requires temperatures between 1200°C and 1400°C for ceramics, especially in dental applications.
- This range is critical because it allows atoms to diffuse and particles to fuse without liquefying the material.
- For zirconia, the transformation from monoclinic to polytetragonal crystalline states occurs around 1100°C to 1200°C, but higher temperatures (up to 1500°C) are often used to achieve near-theoretical maximum density.
-
Role of Temperature in Sintering:
- Temperature is a key factor in sintering as it must be high enough to enable atomic diffusion and particle bonding but below the material's melting point to prevent liquefaction.
- The sintering furnace must maintain precise temperature control to ensure the material achieves the desired density and structural properties.
-
Stages of the Sintering Process:
- Powder Preparation: The raw material is prepared into a compact form using methods like cold welding, 3D printing, or pressing.
- Heating and Consolidation: The compact is heated to just below its melting point, activating crystalline microstructures and initiating particle bonding.
- Particle Merging: Particles densify and merge, a process that can be accelerated using techniques like liquid phase sintering (LPS).
- Solidification: The material cools and solidifies into a unified, dense structure.
-
Material-Specific Considerations:
- For zirconia, the sintering temperature is critical for achieving the desired crystalline transformation and density.
- Sintering furnaces often operate at higher temperatures (e.g., 1500°C) to ensure maximum density, which can reach up to 99% of the theoretical maximum.
-
Importance of Precise Temperature Control:
- Sintering furnaces must maintain temperatures below the material's melting point to avoid liquefaction while ensuring sufficient heat for particle fusion.
- This precision is crucial for achieving the desired mechanical and structural properties in the final product.
-
Applications and Implications:
- In dental applications, sintering is used to create high-strength ceramic restorations like crowns and bridges.
- The ability to control sintering temperature directly impacts the quality, durability, and performance of the final product.
For more information on sintering furnaces, you can refer to this detailed guide: sintering furnace.
Summary Table:
Aspect | Details |
---|---|
Temperature Range | 1200°C–1400°C (up to 1500°C for zirconia) |
Key Role of Temperature | Enables atomic diffusion and particle bonding without liquefaction |
Stages of Sintering | Powder preparation, heating, particle merging, solidification |
Material-Specific Factors | Zirconia requires 1100°C–1200°C for crystalline transformation |
Precision Importance | Ensures optimal density, structural integrity, and mechanical properties |
Applications | Dental restorations (crowns, bridges) and high-strength ceramic components |
Need precise sintering solutions for your ceramics? Contact our experts today to learn more!