The temperature of the heat of the arc in arc welding is a critical factor that influences the welding process, material properties, and the quality of the weld. Based on the provided references, the arc temperature in welding processes can be inferred to be extremely high, typically in the range of 3000°C to 3500°C. This high temperature is necessary to melt the base metals and filler materials, ensuring proper fusion and adhesion. Below is a detailed explanation of the key points related to this topic.
Key Points Explained:
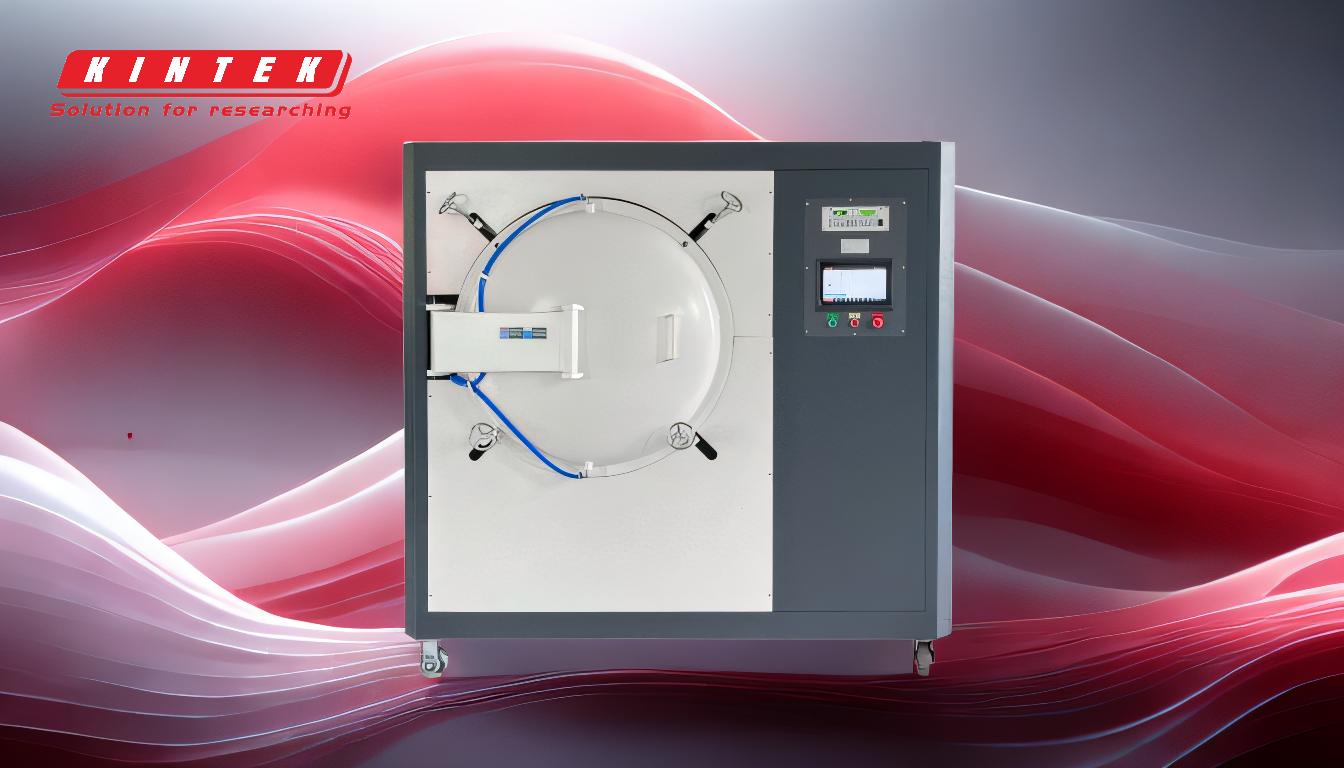
-
Arc Temperature in Welding
- The electric arc in welding processes generates temperatures between 3000°C and 3500°C, as referenced in the context of electric arc furnaces. This temperature range is consistent with the heat required to melt metals and create strong welds.
- The high temperature ensures that the base metals and filler materials reach their melting points, allowing for proper fusion and bonding.
-
Heat Generation and Deposition Rates
- Arc welding is characterized by high deposition rates, typically ranging from 1-3 µm/h, as mentioned in the reference. This efficiency is due to the intense heat of the arc, which rapidly melts and deposits material.
- Despite the high arc temperature, the heat input to the substrate is relatively low, allowing welding to occur at substrate temperatures below 100°C. This minimizes thermal distortion and damage to the workpiece.
-
Ionization and Adhesion
- The high ionization of the arc plasma results in excellent adhesion of the deposited material. This is crucial for creating dense, durable coatings and strong welds.
- The intense heat of the arc ensures that the molten metal bonds effectively with the base material, reducing the risk of defects such as porosity or incomplete fusion.
-
Flexibility in Welding Applications
- The ability to position cathodes in any orientation, as mentioned in the reference, highlights the flexibility of arc welding systems. This adaptability allows for welding in complex or hard-to-reach areas.
- The high arc temperature ensures consistent performance across various welding configurations, making arc welding suitable for a wide range of applications.
-
Implications for Material Selection and Welding Parameters
- The extreme heat of the arc necessitates careful selection of welding parameters, such as current, voltage, and travel speed, to control the heat input and prevent overheating or underheating.
- Materials with high melting points, such as stainless steel or titanium, can be effectively welded using arc welding due to the high arc temperature.
-
Comparison with Other Welding Processes
- Arc welding's high arc temperature distinguishes it from other processes like gas welding or laser welding, which may operate at lower temperatures or with different heat transfer mechanisms.
- The ability to achieve such high temperatures with relatively simple equipment makes arc welding a cost-effective and versatile option for many industries.
In summary, the temperature of the heat of the arc in arc welding is typically between 3000°C and 3500°C, as evidenced by the reference to electric arc furnaces. This high temperature is essential for melting metals, ensuring strong adhesion, and achieving high deposition rates. The flexibility and efficiency of arc welding make it a widely used process in various industrial applications.
Summary Table:
Key Aspect | Details |
---|---|
Arc Temperature Range | 3000°C to 3500°C |
Deposition Rates | 1-3 µm/h |
Substrate Temperature | Below 100°C |
Adhesion Quality | Excellent, due to high ionization |
Flexibility | Welding in any orientation, suitable for complex applications |
Material Compatibility | Effective for high-melting-point metals like stainless steel and titanium |
Comparison with Others | Higher temperature than gas or laser welding, cost-effective and versatile |
Need expert advice on arc welding for your project? Contact us today to get started!