Annealing hardening, a critical process in metallurgy, involves heating materials to specific temperatures to alter their physical and sometimes chemical properties, followed by controlled cooling. The temperature range for annealing hardening varies significantly depending on the material being treated, typically ranging from 500°C to 1200°C. For instance, steel is often annealed at temperatures between 700°C and 900°C, while aluminum alloys might require lower temperatures, around 300°C to 500°C. The process aims to reduce hardness, increase ductility, and eliminate internal stresses, making the material more workable and less prone to cracking. Understanding the precise temperature range for a specific material is crucial to achieving the desired mechanical properties and ensuring the material's performance in its intended application.
Key Points Explained:
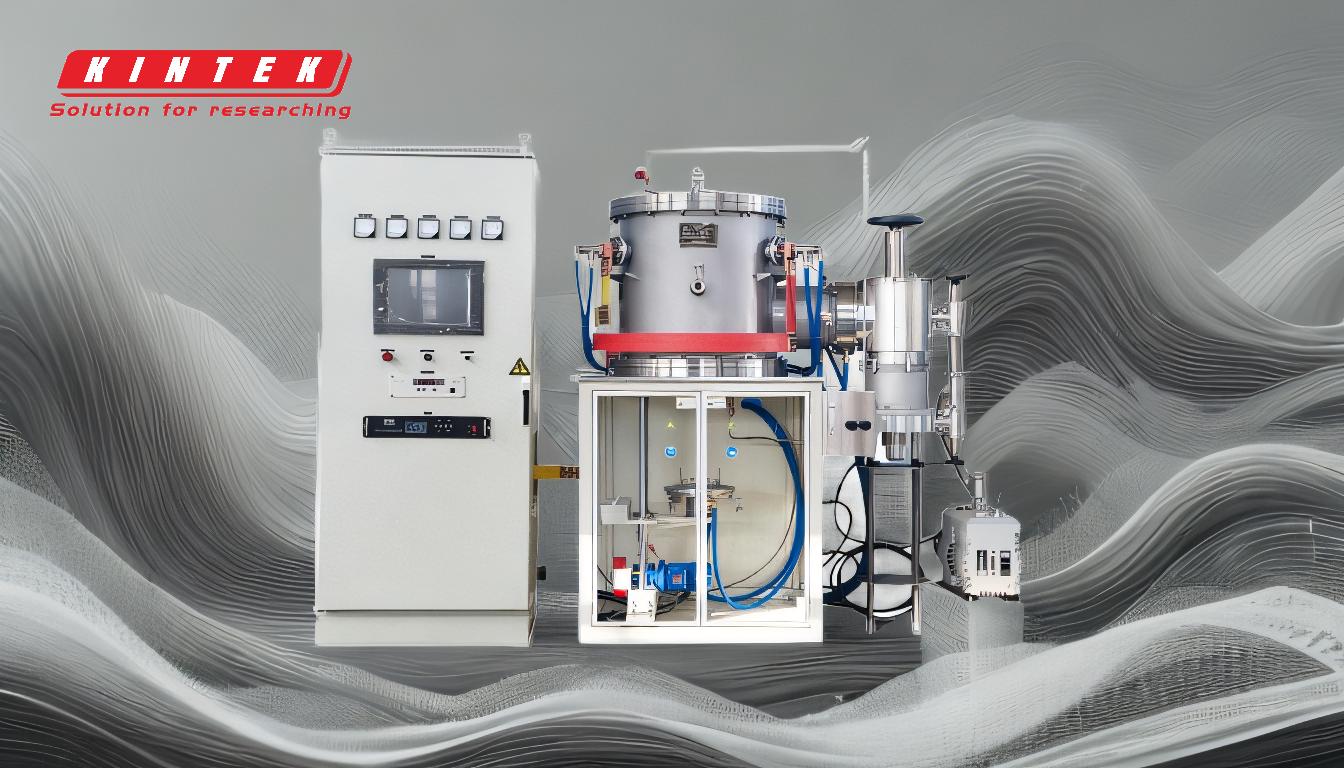
-
Definition and Purpose of Annealing Hardening:
- Definition: Annealing hardening is a heat treatment process where a material is heated to a specific temperature, held at that temperature for a period, and then cooled at a controlled rate.
- Purpose: The primary goals are to reduce hardness, increase ductility, and relieve internal stresses within the material. This makes the material easier to machine, form, or weld.
-
Temperature Range Variability:
- Material Dependency: The temperature range for annealing hardening is highly dependent on the type of material being treated. Different materials have different critical temperatures at which their microstructure changes.
- Steel: For steel, the annealing temperature typically ranges from 700°C to 900°C. This range allows for the transformation of the microstructure, which can significantly alter the material's properties.
- Aluminum Alloys: Aluminum and its alloys generally require lower annealing temperatures, usually between 300°C and 500°C. This is because aluminum has a lower melting point compared to steel.
- Other Metals: Other metals like copper, brass, and titanium have their own specific annealing temperature ranges, which must be adhered to for optimal results.
-
Importance of Controlled Cooling:
- Cooling Rate: After reaching the annealing temperature, the material must be cooled at a controlled rate. Rapid cooling can lead to the formation of undesirable microstructures, while slow cooling helps in achieving the desired properties.
- Cooling Methods: Common cooling methods include furnace cooling, air cooling, and controlled atmosphere cooling, each chosen based on the material and the desired outcome.
-
Impact on Material Properties:
- Hardness and Ductility: Proper annealing reduces the material's hardness, making it more ductile and easier to work with. This is particularly important in manufacturing processes where the material needs to be shaped or formed.
- Stress Relief: Annealing helps in relieving internal stresses that may have been introduced during previous manufacturing processes, such as machining or welding. This reduces the risk of material failure under stress.
- Grain Structure: The process also affects the grain structure of the material, leading to a more uniform and refined microstructure, which enhances the material's overall performance.
-
Practical Considerations for Equipment and Consumables Purchasers:
- Selection of Annealing Equipment: Purchasers should consider the specific temperature requirements of the materials they will be processing. This includes selecting furnaces that can achieve and maintain the necessary temperatures with precision.
- Energy Efficiency: Given the high temperatures involved, energy-efficient furnaces can lead to significant cost savings over time.
- Safety and Compliance: Ensuring that the equipment meets safety standards and regulatory requirements is crucial, especially when dealing with high-temperature processes.
- Maintenance and Durability: The durability of the equipment and the ease of maintenance are important factors, as frequent repairs or replacements can be costly and disrupt production.
-
Conclusion:
- Precision and Control: The success of the annealing hardening process relies heavily on precise temperature control and appropriate cooling rates. Understanding the specific needs of the material being treated is essential for achieving the desired properties.
- Economic and Operational Efficiency: For equipment and consumables purchasers, investing in the right annealing equipment and understanding the process's nuances can lead to improved material performance, reduced costs, and enhanced operational efficiency.
In summary, the temperature range for annealing hardening is a critical parameter that varies widely depending on the material. Proper control of this range, along with controlled cooling, is essential for achieving the desired material properties. For purchasers, selecting the right equipment and understanding the process's intricacies are key to ensuring successful outcomes in material treatment.
Summary Table:
Material | Annealing Temperature Range | Key Purpose |
---|---|---|
Steel | 700°C - 900°C | Reduce hardness, increase ductility |
Aluminum Alloys | 300°C - 500°C | Lower melting point, stress relief |
Copper | 400°C - 700°C | Improve workability, refine grain structure |
Titanium | 700°C - 900°C | Enhance strength, relieve internal stresses |
Ensure optimal material performance with precise annealing hardening—contact our experts today for tailored solutions!